Top 5 Areas to Consider Automation of Plating Operations
Automation for finishing operations can lead to improvements in process time, repeatability and consistency of quality. Yet, processes that make sense to explore for these operational efficiencies may not always be readily apparent.
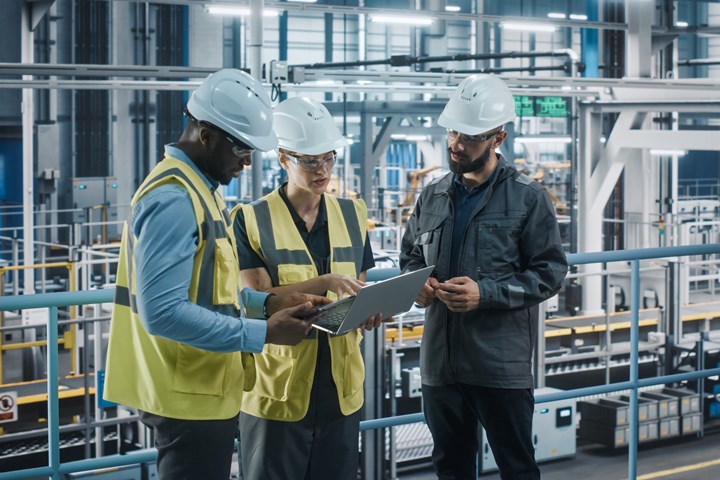
When talking with many plating shops about automation, the most common reply is, “Well, we’ve always done it this way,” often followed by, “It’s too expensive.” These can be some of the most damaging phrases in the language. If you think about the process, ask some questions. Can we operate within a tighter process window? Is our final finish more consistent? Do we get real-time data collection/warehousing? Do we get real-time alarm notification? What about time and cost improvements? Can real-time analysis reduce overhead? How consistent is our manual testing? Can we minimize chemical feed for better inventory management and reduced waste? Are other value-added tasks being done sporadically because we do not have the resources available to do these tasks?
If you do not like the answers to the above questions, take a look at the judicious use of automation.
Where Might We Find Operational Efficiencies?
Five areas to consider include:
- Pretreatment
- The process — the final finish/product
- Incoming and reuse water
- Utilities
- Wastewater treatment
Pretreatment
In an industrial manufacturing process, pretreatment is one of the most important steps in the process. All industrial parts need to be cleaned, degreased, and properly dried to ensure adhesion of intermediate or final finishes. This applies to plating, anodizing, powder coating and paint. Most of these pretreatment systems include alkaline or acid cleaners, often more than one cleaning stage. They may have a conversion coating stage such as iron or zinc phosphate or non-phosphate containing zirconium. Rinse bath cleanliness is key in stopping chemical reactions taking place, removing emulsified oils, and minimizing carry-over from one stage to the next.
Monitoring and control in pretreatment is possible via numerous methods. Manual controls include total and free acid or alkali for cleaners. Conversion coatings and sealers are all monitored for total and free acid and in the case of zinc phosphates, the activator, accelerator and zinc are monitored while sealers are monitored for the active ingredient. Chrome containing conventional pretreatments which include chrome phosphate, chromate and rinses are monitored for total and free acid, hexavalent and total chrome, and the accelerator. Dried-in-place pretreatments containing chrome are monitored for hexavalent chrome while non-chrome systems monitor free acid and active ingredients1.
Automation utilizing control equipment may be accomplished in all these pretreatments. Conductivity is used to control cleaner concentrations, water flow to rinse tanks, sealer active ingredients, and non-chrome dried-in-place pretreatments. Control of pH is key for cleaner rinses, iron phosphate, and chrome and non-chrome dried-in-place pretreatments.
Figure 1 shows how a multi-I/O, microprocessor controller is used to monitor and control a multi-stage washer.
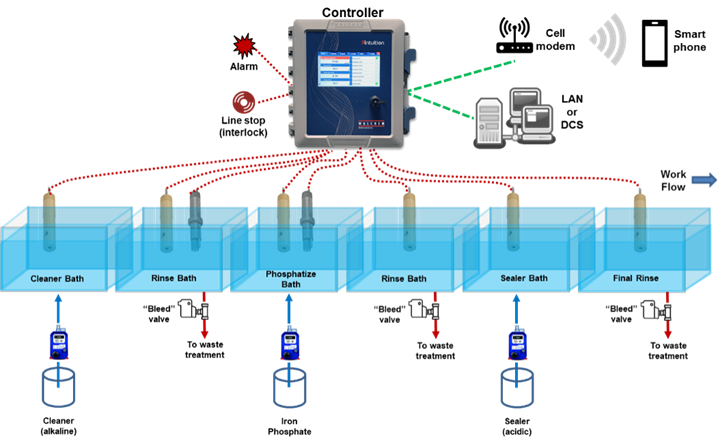
Figure 1: 5-stage pretreatment system.
Photo Credit: All images courtesy Walchem
Process
Many improvements may be realized via automation of the process itself. These include more robust and stable plating baths, operating within a tighter process window, resulting in a more consistent finish. Real-time alarm notification allows operators to correct an issue before it becomes out of control. Time and cost improvements may also be realized. Minimized chemical feed allows for better inventory management and reduced waste. Real-time analysis reduces the cost of manual testing and frees up resources for other important value-added tasks.
Figure 2 is an example of an electroless nickel (EN) bath.
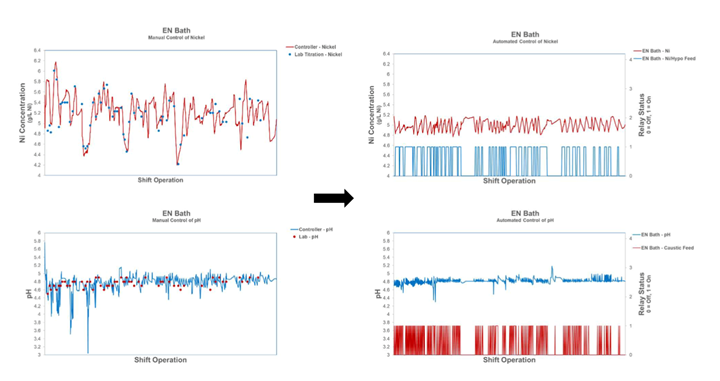
Figure 2: EN bath pre-automation and post-automation2
Both nickel concentration and pH results saw a more than 3-fold improvement. Testing time was reduced by 75% with cost savings nearing $4,000 annually per bath. This freed the operators to focus on other critical aspects of the process, improving the quality and consistency of the plating. LNS use was down 6-8% with the same plating coverage. Reduction in manual testing materials saved $1,700 per bath. Chemistry-related plate out was reduced to near zero, allowing operators to focus on eliminating non-chemistry plate out.
Automation of copper concentration is also possible for electroless copper with the buffer, reducing agent and complexing agent fed in proportion to the copper salt. Micro-etch systems can be controlled on copper to feed fresh etchant in PCB manufacturing.
Conductivity may be used in hard chrome applications3. The conductivity is at its peak in a new bath. Once tramp metals build up during the plating process, the conductivity drops resulting in a drop in the effectiveness and efficiency of the current in the bath. This will negatively impact throwing power, covering power, roughness, and other important facets of plating quality.
In aluminum anodizing, pH, and conductivity controls various points in the process. Dyeing baths and sealing baths use pH control. Conductivity control of sulfuric acid levels in Type II anodizing operations is possible. Conductivity can also control the alkaline cleaner which is critical for final product quality.
Metal concentration in electrolytic nickel and copper baths may be controlled via spectrophotometry and pH adjustment can be automated. Amp-hours meters can be used to automate brighteners and levelers.
Incoming & Reuse Water
The quality of both incoming water and water reused from rinse baths and wastewater treatment will impact the quality of the processes using it.
Incoming water may come from various sources and may be hard or soft and contain minerals that shorten bath lifetimes, create spots, trails, and/or flaky salt deposits.
Water treatment methods include ion exchange, ultrafiltration, and (RO) amongst others used either individually or together to obtain water quality for the function.
Figure 3 below shows a typical RO system and how its various parts can be readily automated using a microprocessor controller.
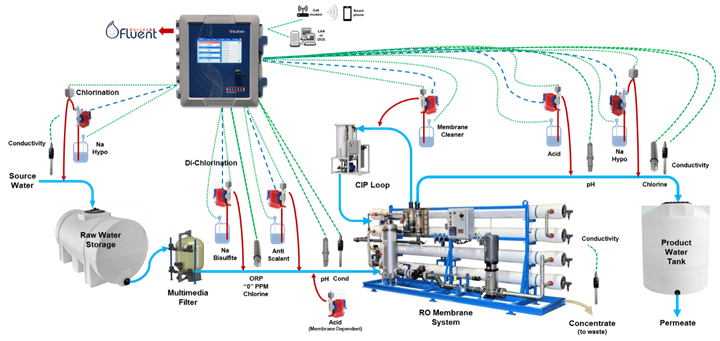
Figure 3: A typical RO system and how it may be automated.
Source water is typically chlorinated before passing through a multimedia filter. Then it is de-chlorinated to extend membrane life and an anti-scalant is fed. The water passes through the RO membrane system. Two separate streams result, the concentrate and the permeate. The RO unit’s concentrate is used with recovery rinse tanks to recover chemical and returned to the plating baths. The permeate is recycled back to the process through the rinse tanks. Recovery rates of 95% are obtained for typical finishing operations4. Rejected permeate can then be sent to waste for further processing.
Utilities
These include cooling water, boiler water and pollution controls, in particular fume scrubbers.
Cooling water temperature control is important in electrolytic solutions for the reaction to perform properly. Temperature requirements range from about 28°F in hard coat anodizing to 130°F for chromium. Temperatures can change due to several factors including tank size, plating room temperatures, parts temperature, and their weights. Cooling towers are also important for air conditioning as well.
With proper control equipment, there are opportunities for reduced water consumption allowing recycled water to be used in both the process and HVAC systems. This also allows for reduced chemical usage whose savings often outweigh the water reduction savings. Reduced corrosion and scale formation resulting in longer equipment lifetimes. Some localities provide sewer credits due to evaporative losses. Finally, proper cooling tower monitoring and control reduces/eliminates the potential for Legionella growth, a serious health concern.
Proper control of a boiler and its condensate is another area for cost-saving opportunities. Use of RO reuse water, along with proper control of condensate return to the boiler feedwater, results in improved heat transfer, reduced corrosion, and scale formation for longer equipment lifetimes. Proper control of the condensate return results in energy savings, reduced chemical usage, less feedwater needs and sewer disposal costs.
In wet air scrubbers, any noxious gas pollutants from the process are removed using a counterflow of water droplets to collect these pollutants. Chemical addition is controlled by pH or ORP depending on the process pollutants. TDS can be controlled via conductivity, draining contaminated water, and adding fresh water. The contaminated water is treated and potentially reused.
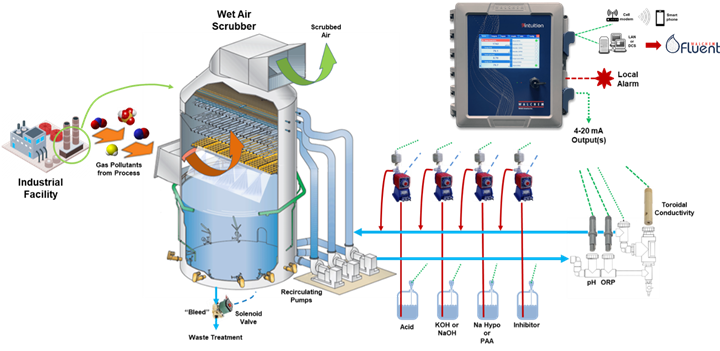
Figure 4: Typical wet air scrubber.
Wastewater Treatment
Treatment may include pH neutralization, metals recovery, water reclamation/reuse, chlorination/de-chlorination, clarification and filtration. Waste may contain heavy metals, oils and grease, and suspended solids often at levels too toxic for release to a POTW or into the watershed and must be further processed. Hydroxide metal precipitation and other post treatments can be noxious and toxic. Further pH neutralization steps are included, and the stream is treated with a polymer flocculent and then to a clarifier. The sludge is collected for further processing in a filter press and hauled away to a disposal site. Water collected in the dewatering process can be further processed before disposal to the POTW, watershed, or reused in the plant. Many steps may be monitored and controlled to meet permit-specific requirements.
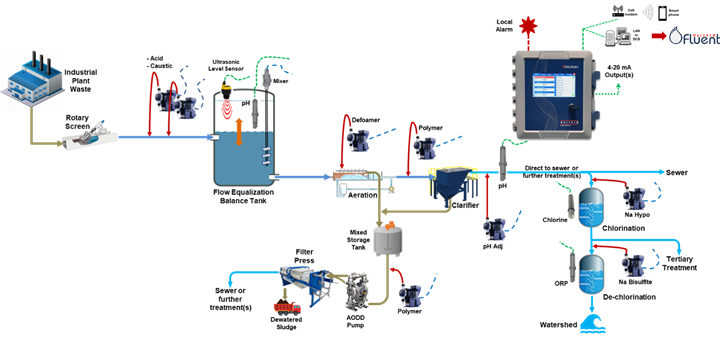
Figure 5: Some typical components in an industrial waste treatment operation.
Conclusions:
Microprocessor-based controllers can be used in many areas within a metal finishing shop. These controllers have the flexibility, I/O, preconfigured control strategies and the capability to create special control algorithms. All data may be collected and stored locally on the controller as well as maintained using a cloud-based account management software tool for remote monitoring and control, and data visualization. The controller can also be directly tied into the plant’s LAN or system management via Modbus TCP.
Take a closer look at the entire plant and determine where you will obtain the best ROI and start adding automation. Once successfully implemented, move to another system in the plant. You will soon see cost savings throughout your entire operation.
References:
- Powder Coating: The Complete Finisher’s Handbook, 4th Edition, The Powder Coating Institute 2012, page 9.
- “Automation and Control of Electroless Nickel Baths,” Robert Rumelfanger, in the June 2021 issue of Products Finishing, pages 20-23.
- “Conductivity in Hard Chrome Plating Baths,” Adam G. Blakeley, in the February 2021 issue of Products Finishing, pages 33-35.
- “Recovery/Recycling Method for Metal Finishers,” Stephen R, Schulte, published September 29, 2011, in Products Finishing.
About the Author
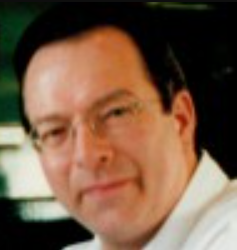
Robert Rumelfanger
Robert Rumelfanger is the Northeast Regional Sales Manager and Metal Finishing/Surface Treatment Champion for Walchem - IWAKI America, Inc. Visit walchem.com/metal-finishing-surface-treatment for more details.
Related Content
Hubbard-Hall Acquires BioConversion Technology
The acquisition adds experience and biologics to the AquaPure product line.
Read MoreNASF/AESF Foundation Research Project #122: Electrochemical Approaches to Treatment of PFAS in Plating Wastewater - 6th Quarterly Report
The NASF-AESF Foundation Research Board has selected a project on addressing the problem of PFAS and related chemicals in plating wastewater streams, studying PFAS destruction via electrooxidation and electrocoagulation. This sixth quarter report covers the continued assessment of eight perfluoroalkyl acids PFAAs most commonly found in wastewaters, by electro-oxidation with a Magnéli phase Ti4O7 anode across a range of anodic potentials in solutions, exploring the reaction mechanisms. To summarize, the PFAAs start to exhibit degradation behavior when the anodic potential reaches a level where water oxidation occurs, suggesting that the hydroxyl free radicals generated via water oxidation play a role in PFAA degradation.
Read MoreNASF/AESF Foundation Research Project #120: Electrochemical Destruction of Perfluorooctanesulfonate in Electroplating Wastewaters – 7th & 8th Quarter Report
This NASF-AESF Foundation research project report covers the seventh and eighth quarters of project work (October 2021-March 2022) at the University of Illinois at Chicago. The major activities reported are: (1) to investigate 6:2 FTS oxidation, a common replacement compound for PFOS in the electroplating industry, and (2) PFAS oxidation in both a wastewater sample procured from an electroplating facility and in synthetic solutions.
Read MoreNovel Wastewater Treatment Targets Micropollutants
Swiss wastewater treatment technology provider Oxyle specializes in advanced wastewater treatment for removal of highly persistent micropollutants such as PFAS.
Read MoreRead Next
Titrations: To Automate or Not to Automate?
What considerations should you keep in mind for automatic titrations? Conor McAnespie of Hanna Instruments discusses the benefits of auto titrators.
Read MoreRacking and Conveyor Automation Solutions
Considerations for automating various operations within a finishing system.
Read MoreAutomation and Control of Electroless Nickel Baths
Spectrophotometric nickel/pH controller enables tighter control of the ENi process, resulting in improved product quality.
Read More