How to Avoid Mud Cracking
Julie Holmquist of Cortec Corporation discusses ways to avoid mud cracking defects when applying anticorrosion coatings.
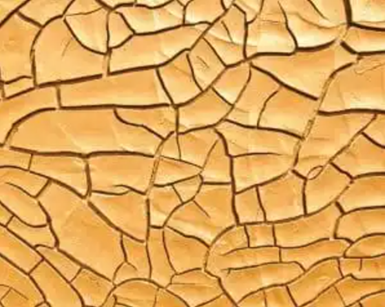
Q: I’m having problems with cracking defects when applying liquid coatings. Do you have any advice for avoiding this kind of defect?
A. No one wants to apply paint or an anticorrosion coating only to come back later and find that it has dried to look like cracked mud. Not only does the texture look bad, but it also leaves behind cracks that go down to the metal surface, making it more susceptible to corrosion. While the problem of mud cracking can only be resolved by removing and reapplying the coating, it is very easy to prevent by following the guidelines below.
Why Does Mud Cracking Happen?
No matter how good a coating is, mud cracking can occur when the coating is applied too thickly. This is because solvents and water evaporate out of the paint at a certain rate as the coating dries. If the coating is too thick, the surface of the coating dries more quickly than the volatiles underneath can evaporate. Once the surface dries, the volatiles are trapped below, and the only way they can escape is by cracking the dry surface layer to get out. While mud cracking can happen with either solvent- or water-based coatings, it is more common in water-based coatings because water evaporates more slowly.
How Can You Prevent Mud Cracking?
The solution for preventing mud cracking is extremely simple: follow the manufacturer’s recommendations for coating thickness. The coating manufacturer already knows how the coating will behave and usually provides both a wet film thickness (WFT) and a dry film thickness (DFT) recommendation on the product data sheet. To avoid mud cracking, the coating applicator simply needs to apply the recommended WFT, measuring coating thickness with a WFT gauge to make sure it is correct.
If only the DFT is listed, the painter can figure out the proper WFT based on the recommended DFT and the percent volume of solids. This percentage tells how much of the coating will remain after the volatiles have evaporated. For example, an approximately 50% volume solids coating such as VpCI-395 will lose about half of its WFT by the time it dries. To get 3 mils (75 µm) DFT, the coating will need to be applied at 6 mils (150 µm) WFT. A coating such as EcoShield VpCI-386 with a 31% volume of solids will lose a little more than two-thirds of WFT by the time it dries, meaning 9.6 mils (240 µm) WFT are needed to achieve 3 mils (75 µm) DFT.
What If You Need a Thicker Coating?
Sometimes, it is necessary to apply a thicker coating than normal. If this is the case, the painter can avoid mud cracking by applying the paint in multiple coats and allowing them to dry in between each application.
Follow Instructions
Often the best way to achieve success is right in front of us. By following WFT recommendations on a coating’s technical data sheet, painters can avoid unnecessary problems and rework caused by mud cracking.
About the Author
Julie Holmquist
Julie Holmquist is a content writer for Cortec Corporation. Visit corteccoatings.com.
Related Content
Fixing Corrosion Between Anodized Aluminum and Steel
Anne Deacon Juhl, Ph.D., with AluConsult, says Galvanic corrosion is due to an electrical contact with a more noble metal or a nonmetallic conductor in a conductive environment.
Read MoreNickel Electroplating
Applications, plating solutions, brighteners, good operating practices and troubleshooting.
Read MoreThe Powder Coating Process
Powder coating is one of the most durable finishes that can be applied to industrial manufactured products, and offers excellent corrosion protection and is very safe because of its lack of volatile organic compounds. To understand the powder coating process you should start with the fundamentals.
Read MoreRead Next
Episode 42: An Interview with Robin Deal, Hubbard-Hall
Hubbard-Hall wastewater treatment specialist Robin Deal discusses the latest trends in wastewater management.
Read MorePowder Coating 4.0: Smarter, Faster, More Efficient and Connected
New tools reduce cost and waste, lower manufacturing footprint of powder coating operations.
Read MoreThe 2024 Ford Mustang: All the Colors Available
Although Chevrolet has announced the end of the Camaro and Dodge is offering “Last Call” editions of the Charger and Challenger, the Ford Mustang is launching to its seventh generation.
Read More