Share
Custom Fabrication & Supplies (CFS) is perhaps best known for its standard masking products, including a wide range of tapes, plugs, die-cuts and more. But this manufacturer is in fact a custom converter with a wide range of engineering expertise and production capabilities to serve diverse masking requirements for powder coating, electrocoating, wet spray, anodizing and plating. Their approach to masking applications, whether through technical support to select a better masking product or by engineering a custom solution, provides a good example of how to go about solving masking problems.
While CFS is certainly no stranger to versatility and customization, it has taken a dramatic step up in its capabilities by doubling the size of its Franklin, WI, plant and packing it with an array of new production equipment. According to CFS VP Brian Asik, besides providing broader capabilities, the upgrade brings more high-speed production equipment and automation to the mix, increasing capacity as much as 10 times over prior levels.
We should note that CFS already had a wide variety of converting equipment in-house including precision die cutting, flash cutting and slitting equipment for converting tapes and pressure-sensitive materials. They even have 3D printers which allow CFS to quickly deliver prototypes or short-run products, often with next-day delivery, which they can do for die cuts as well.
But the new equipment takes CFS’s game to a whole new level. Here's a look at some of the new capabilities.
Rotary Laser Die Cutting
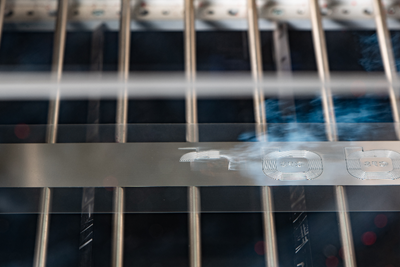
Delta Modtech Precision rotary press with in-line laser cutting
Rotary die cutters have long been a staple of the masking business, most often applied to standard peel-and-stick shapes. CFS’s new Delta Modtech Precision rotary press with in-line laser cutting raises the bar with the ability to cut custom masks with remarkable precision. Some better die cutters can achieve tolerances of 50 thousandths of an inch (0.010”) with hard tooling. With CFS’s new laser cutter they can hold tolerances of 0.003” or better. Completely computer controlled with quick change tooling, the machine can cut and laminate multiple materials together, as is often done with masking products, with remarkable accuracy.
While rotary die cutters are extremely efficient, they do require tooling, which must be manufactured, and some degree of mechanical setup time. Laser cutters are largely free of these limitations and provide almost limitless capabilities to generate custom mask forms. Laser die cutting technology can be leveraged to produce rapid prototypes and production die cuts with extreme precision. It can be a stand-alone process or can be used in-line with hard tooling to create complex shapes and multi-layer laminations. Unlike traditional die cutting methods, the laser can create tricky patterns and fine details which are otherwise impossible. This highly repeatable method enables the smallest holes, slots and perforations to be cut.
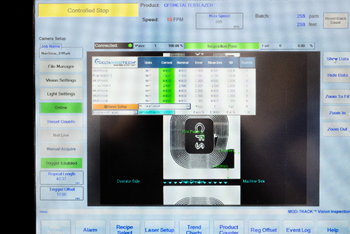
The Edge laser is equipped with an integrated MOD-Track machine vision system.
In addition, the Edge® laser is equipped with an integrated MOD-Track® machine vision system. Vision setup and real-time results can be viewed and adjusted on the touchscreen operator interface. The software enables shop floor adjustments to vision acceptance criteria without needing an engineer to make changes. On-screen measurement tools are a real-time saver for operations with frequent product changes. This system also tracks each part and can supply a spreadsheet detailing the measurements of every part produced. This all means CFS can respond more quickly to intricate custom jobs and economically produce smaller run volumes, all while maintaining the industry’s most precise final products.
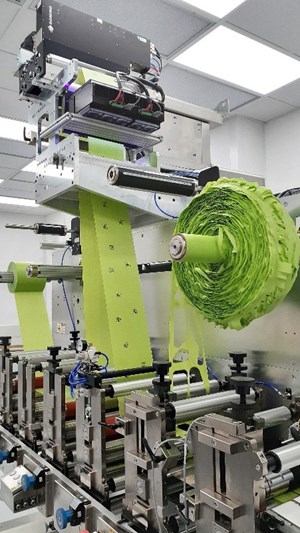
The Delta ModTech machine, which came on-line in 2018, is housed in the company’s ISO 7 clean room.
Die Cutters with Data Printing
The original Delta ModTech machine which came on-line in 2018 is housed in the company’s ISO 7 clean room and features the ability to print bar codes or other markings in a fast, continuous process. The printing capabilities can be used in a variety of ways to enhance finishers’ masking operations. For example, application instructions can be printed right on the mask, or a QR code can be added to enable in-process inspection or generate an automatic inspection report.
The Delta die cutting presses are in addition to CFS’s three Atom FlashCut Flex models which are computer-controlled machines that combine cutting and milling operations on materials up to 5” in thickness. These die-less machines use oscillating knives to cut masking materials exactly to masking shape specifications and can work directly from CAD files.
Flat Die Press for Thick Materials
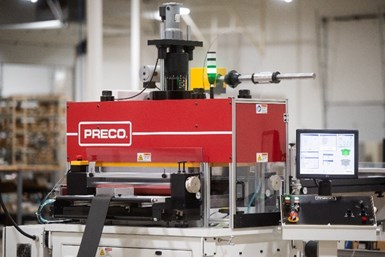
The Preco flatbed press is a perfect option for thicker materials or larger diameter masking which exceeds the 13” limitation of standard rotary die cutting presses.
Thicker materials present a challenge for standard die-cutting machines with greater depths of cut, material deflection and the need for efficient slug removal. CFS has enhanced its capabilities here with a new Preco flatbed hydraulic press. It features fully adjustable stroke height and tonnage settings in a four-post configuration that ensures parallelism between the die board and the cutting surface. This press is designed to promote fast setup, reduction of tool wear, and provides a variety of finishing capabilities. The Preco can also be outfitted with matched metal (male-female) tooling for extreme precision on thick gasket foams. Designed for cutting gaskets, the Preco is a perfect option for thicker materials or larger diameter masking which exceeds the 13” limitation of standard rotary die cutting presses.
High-Speed Slitter/Rewinder
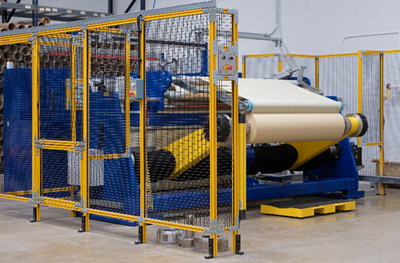
The Elite Cameron high-speed duplex center winder is capable of handling a wide range of materials including papers, label stock, packaging films, laminates and more
Slitters are an important component of tape converting – and therefore masking product production. They allow you to stock large bulk rolls of material and then quickly reduce it to exact material widths for specific jobs or products. Doing this well provides better responsiveness, less waste and better utilization of downstream equipment – all benefits that accrue to the end user in price and/or delivery.
CFS’s new heavy-duty, Elite Cameron high-speed duplex center winder is capable of handling a wide range of materials including papers, label stock, packaging films, laminates and more. And it is fast. Their original slitter/winder ran at 200 feet per minute. The new one is three times the size and runs at 1000 fpm.
The Siat narrow web rewind slitter is a specialty machine with a very unique use. Certain tapes, like 3M 468MP are notoriously difficult to slit using standard single-knife operations. The lack of carrier material causes the tape to “roll” onto subsequent layers, making them challenging to unwind. The Siat can unwind the master roll, slit with razors and precisely rewind onto new cores. This process is slower than traditional methods but provides extremely precise rewind slitting.
CFS has also added a FEBA F600 automatic slitter for a variety of small to large-diameter materials including adhesive and non-adhesive tapes, self-adhesive tapes, VHB, foam & laminated foams, non-asbestos & cork materials, textiles & non-woven fabrics - converting diameters to 24”, log widths to 62”, roll slitting as narrow as 0.062”.
Compression & Transfer Molding
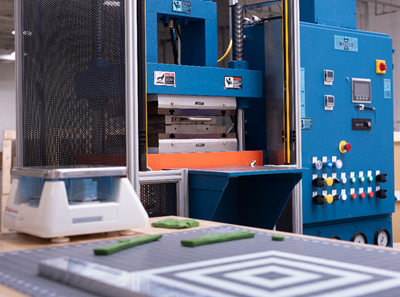
The new compression and transfer molding press offers fast opening and closing speeds, and heat platens can generate temperatures from 500° to 1800°F.
In high-heat applications silicone rubber is an ideal masking material because of its inherent thermal resistance properties. Historically, much of the silicone compression molding is completed overseas. This has become problematic in the past couple of years, with supply chain delays and material shortages. CFS is addressing this issue with new in-house compression and transfer molding capability at the Franklin, WI headquarters. The hydraulic system produces faster opening and closing speeds, and heat platens can generate temperatures from 500° to 1800°F. This in-house capability enables CFS to ship both compression and transfer molded products in a couple of weeks vs a few months after tooling has been approved.
Get Help With Masking Solutions
Masking products are generally inexpensive, but masking failures are not. Whether it’s reworked or scrapped parts, fixing the problem afterward can cost thousands of dollars due to the failure of a $0.75 plug. This is why it’s important to have a masking supplier with broad knowledge about masking products, available materials and finishing processes. The CFS engineering group has a great deal of experience in all these areas and the company is in fact a 3M Preferred Converter.
Most important about CFS’s custom development and manufacturing capabilities are the relationships they have developed with customers over time.
What Brian Asik thinks is most important about CFS’s custom development and manufacturing capabilities are the relationships they have developed with customers over time. Brian’s brother, Henry Asik, opened the doors of CFS in 2000 and Brian has been with him every step of the way. Still family owned and operated, the company has enjoyed exceptional stability over time with key employees working with individual customers for years, gaining a high degree of familiarity with the customers’ processes along the way. Contact the CFS applications team and see firsthand what that means.
For more information please visit the Custom Fabricating & Supplies website.