Mitigating Inconsistencies From Liquid Coating Tank Changes
Mike Bonner of Saint Clair Systems discusses strategies for keeping liquid coatings homogenous and mitigating inconsistencies when changing process drums.
Q: The other day I got a call from a friend who is a production manager at a coating facility. He asked if I could settle an argument between his operator and his process engineer. The operator said it was better for him to let the drum get empty and then switch to the next drum, while the process engineer said that the process drum should be treated as a “day tank” and kept full all the time.
A: This is a pretty common question,and the answer isn’t that simple. The problem is that the answer changes based on the situation, which can be clearly defined by five fundamental questions:
- What is the size of your process (day) tank?
- What is the size of your bulk supply?
- What is your rate of consumption?
- How long is your run?
- Do you have a manual or an automatic fill system?
What makes their situation a perfect example is that they have two processes in series: a prime booth that always runs the same coating supplied from 300-gallon totes, and a finish booth supplied from 50-gallon drums which change colors many times a day. In the finish booth, they often do custom colors where a partial drum of paint is purchased for a particular run, but they also do repetitive runs where the same color is used every week to meet just-in-time shipments. Both booths use a 50-gallon drum for their day tank.
So, let’s start with the prime booth.
In this case, we have a continuous operation with a bulk supply that can fill the day tank six times. The key is to keep the coating homogenous and to mitigate any changes between totes. The best way to do this is with a continuous feed running at the rate of consumption so the level in the day tank is always constant. This is fairly easy with an automatic fill system, but as noted in this scenario, the system is handled manually by the operator. It is necessary to minimize the demand on the operator but still keep the coating consistent. To do this, the best approach is to add when the day tank is between half-full and three-quarters full and to stop adding when between the three-quarter and full point. This will ensure that less than 50% new coating is mixed into the day tank. Think of it like painting your house — best practice says to mix paint cans together to minimize any shade or consistency differences. Here we’re doing the same thing. In addition, this will ensure that any temperature difference between the day tank and the tote will be cut in half by the blending and therefore the viscosity will be more consistent. This will also smooth tote changes and differences, just like in the paint can example. This is pretty much in line with the process engineer’s approach.
Now let’s turn our attention to the finish coating booth. This is a little more difficult as there are multiple situations to address.
The easiest is a custom color where the run is short enough that a partial drum of paint is purchased. In this case, the drum can be run from start to finish with no make-up required. In short, the operator is right in this situation — run to the end and then change drums — except in this case, the new drum is also a new color.
The most complicated situation comes with repetitive colors. These present a different situation every time they are run. But it is important that they be the same every time — especially if the weekly batches can get mixed in the end product.
When the color is run for the first time, the process drum will be full, less whatever it takes to fill the system. This is where the rate of consumption and length of run come into play. If the run is long enough to consume the entire drum, then it’s just like the custom color scenario — run to the bottom and stop — no make-up. Even if you have some paint left over when you drain down the system, it can be used to start the next run and combined with the next full drum to minimize any change in performance.
If the run will require more than is in the process drum, then make-up is required. In this instance, revert back to the “add around the three-quarter point” mode of operation described for the primer booth. The difference will be that the bulk supply will be a 50-gallon drum instead of a 300-gallon tote. Why not run to the bottom and then switch to the next drum? The need for consistency. You want to blend out any differences between the process drum and the bulk supply drum by mixing them no more than 50-50. And if you go across more than one or two bulk supply drums, you gradually transition from one to the next which keeps your variation to a minimum for all parameters like color, gloss, viscosity, etc.
This is where a skilled operator shows his/her value. Even with an automated make-up system, knowing when to use it and when to turn it off requires a situational analysis that only an expert can provide.
In short, they’re both right!
About the Author
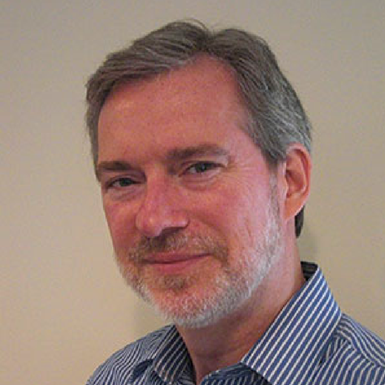
Mike Bonner
Mike Bonner is the vice president of engineering and technology for Saint Clair Systems. Visit viscosity.com.
Related Content
Smart Automotive Paint Booths: Embracing Industry 4.0
Automation, digitization, connectivity, remote process management tools help automakers, suppliers paint parts, vehicles at lower cost, reduced carbon footprint.
Read MoreUnique Coating Reduces Friction of Sliding Ceramic, Metallic, and Polymer Components
An extremely thin, hard diamond-like carbon (DLC) coating decreases the coefficient of friction (COF) of components to nearly zero, while increasing wear resistance.
Read MoreSolving Paint Adhesion Problems
A farm equipment supplier’s quest to find the right cleaning chemistry.
Read MoreCuring Oven Basics
Simply heating up the substrate does not cure the coating. There are many variables to consider when choosing the best cure oven for your application...
Read MoreRead Next
Digitizing Your Job Shop for Increased Production and Profitability
Dean Halonen of ERP software provider Steelhead Technologies discusses how digitizing your metal finishing job shops can help you achieve more production throughput and improve profitability.
Read MoreGetting the Right Mix and Avoiding Cross-Contamination in Manual Spray Processes
Payton Cozart, product manager for Carlisle Fluid Technologies, discusses mixing procedures and options for mitigating paint cross-contamination in spray application processes.
Read MoreReducing Contamination in Your Finishing Application
Justin Hooper of Carlisle Fluid Technologies offers insights for mitigating defects when using 2K urethane paint.
Read More