Causes for Cross Contamination
Cross contamination of powder coatings is often the result of poor habits in the powder room. Powder coating consultant Rodger Talbert offers an example of how to mitigate cross contamination.
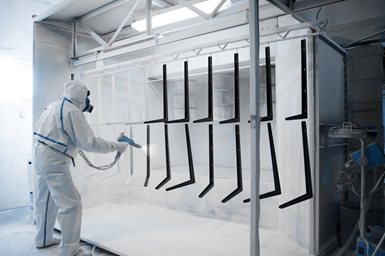
Q: We are a manufacturer of lawn mowers and small tractors with internal powder coating capabilities. We have four standard colors that we use a lot of and a number of other colors that we use less of on a daily basis. We have three powder booths in a large powder room. One booth runs only color 1, one runs only color 2 and the third booth is used for all other colors. All three booths use a cartridge module type of reclaim. We reclaim the color 1 and color 2, but all other colors are sprayed to waste in booth three.
We have always had some minor cross contamination, but it was not a big problem when we started. However, lately it has become a major issue that is causing a lot of rework cost. The color 1 parts often have a large number of specks of color 2 in the finish after cure. The only thing we have changed is our production volume. We started out running 12 load bars per hour and we now run 18 load bars an hour on one shift. We use a power-and-free rail system to send different load bars to the right booth and to stop heavy loads for load/unload and other processes.
Can you tell us what to look for in our system that might cause this problem? We are not sure if it is coming from the application area or the cure oven.
A: The good news is that the problem can be found in one of those two areas you mentioned. The bad news is that the fix may not be easy.
Cross-contamination is often the result of poor habits in the powder room. The application equipment is not thoroughly cleaned during color changes, traces of other colors collect in tight areas of the booth or reclaim system or powder is blown around the room with a compressed air hose. Based on the description of the system, the layout and the dedicated booths, this does not appear to be an issue here.
I would say that you have issues in two potential areas; color 1 parts from booth one are stopped inside the room, fairly close to the opening of booth two where color 2 is applied. With the power and free rail, you are coating color 2 while load bars of color 1 parts are sitting nearby. It is likely that this situation is occurring much more frequently with the production increase you mentioned. It is probable that some color 2 is drifting onto the color 1 parts while they are stopped.
The other question is the cure oven. With all three booths running all the time, you are mixing a lot of uncured colors inside that oven and some powder is bound to drift from one to another.
I recommend that you test to see what the worst problem is, the booth area or the oven. Set up a load of panels and run them through the color 1 booth and stop them the way you usually do. Take them down and cure them in your batch oven to isolate them from the in-line cure oven. Set up another load of panels and coat them in the batch booth in color 1. Run them through the in-line cure oven. Check these panels for the cross-contamination issue. Is suspect you will find that booth samples are contaminated. See if that is so and which one is worse.
In the case of the booths, you need to change the layout so that they are isolated or farther apart. You cannot hold parts that close to another booth. In the case of the cure oven, you may need to install a radiant zone at the entrance to get the powder partially gelled before it hits the air movement of the convection oven. The layout may have worked well at 12 bars an hour, but there is too much activity and spray action going on with the increase.
About the Author

Rodger Talbert
Rodger Talbert began his career in coatings in 1976 when he went to work for a small company that does metal fabrication and custom coating. He worked there for 10 years, rising to the position of VP of Sales and Marketing. He left there to work as a sales engineer for a larger company that designs and builds coating systems, and worked there for seven years. In 1993, Talbert started his own business as a consultant. He ran his own corporation for 15 years before joining The Powder Coating Institute as technical director in 2009. He served as the PCI Executive Director until June 2012.
Related Content
How to Choose Between Sulfate and Chloride-Based Trivalent Chromium
There are several factors to consider when choosing between sulfate and chloride-based baths for trivalent chromium plating. Mark Schario of Columbia Chemical discusses the differences and what platers should keep in mind when evaluating options.
Read MoreImproving Transfer Efficiencies in Coating Operations
There are many methods for addressing electrostatic grounding in metal painting processes, and Tim Ulshafer from Mueller Electric says the best method for your process is a simple and worthwhile exercise.
Read MoreTop Reasons to Switch to a Better Cleaning Fluid
Venesia Hurtubise from MicroCare says switching to the new modern cleaning fluids will have a positive impact on your cleaning process.
Read MoreUnderstanding and Managing White Spots on Anodized Aluminum
Having trouble with spotting defects when anodizing? Taj Patel of Techevon LLC offers a helpful overview of the various causes of white spots and potential solutions.
Read MoreRead Next
Episode 42: An Interview with Robin Deal, Hubbard-Hall
Hubbard-Hall wastewater treatment specialist Robin Deal discusses the latest trends in wastewater management.
Read MoreThe 2024 Ford Mustang: All the Colors Available
Although Chevrolet has announced the end of the Camaro and Dodge is offering “Last Call” editions of the Charger and Challenger, the Ford Mustang is launching to its seventh generation.
Read MorePowder Coating 4.0: Smarter, Faster, More Efficient and Connected
New tools reduce cost and waste, lower manufacturing footprint of powder coating operations.
Read More