Glass Bead Blasting as Plating Pretreatment
What are the best practices for using blasting in preparation for plating? Angelo Magrone of Bales Metal Surface Solutions discusses the ins and outs of glass bead blasting.
Q. Should I blast parts before plating? When should I use blasting vs. chemical cleaning?
A.Let’s take a minute and talk about glass bead blasting. Glass bead blasting is a process used for treating the surface of many different materials for cleaning, finishing, or deburring by applying blast media to a surface, using pressurized air to propel it.
When parts are turned or machined, micro cracks and burrs, and other irregularities of the surface can form. Although these irregularities may not affect the plating, they can cause issues when the parts are in service.
Does blasting damage parts?
Glass bead blasting is not the same as sandblasting. Glass beads are round and smooth, not coarse and jagged like sand. While sand will do the job, it wears the surface down and typically takes away the top layer of material. With the glass beads, it is a peening action to improve the surfaces properties, smooth out micro-cracks, tool marks, and micro burs, and reduce micro pores sizes that you see in powdered or cast metals leaving you a smooth burr-free surface to plate.
Where in the process is it best to blast?
Blasting should not take place until all surface contaminants are removed. Oils and grease impede the effectiveness of the peening action, not to mention soil the media making it less effective for future jobs and causing more frequent change-outs.
Resist the urge to put parts right into your plating tanks after the blasting process. The glass beading process can and will break down the beads, causing dust. This dust sticks to the parts, which will need to be blown off with compressed air and cleaned again in your alkaline cleaner. Remember, we still want the parts to be as clean as possible for plating. Skipping this step can cause missed plating, peeling, flaking, and, if gone undetected, premature part failure in the field.
Advantages and disadvantages of glass bead blasting
Media is generally inexpensive, and many types are reusable. Different media grades are available for various applications specifying a brighter or duller finish. Blasting can remove paint, rust, calcium deposits, scale, and other oxidation. One of the more complex soils (soil meaning anything on the substrate that will interfere with the bond, adhesion or uniformity of the finished deposit) is heat scale — bead blasting is a cost-effective process for removing the heat scale. It quickly gets into hard-to-reach areas like keyways, corners and holes. In addition, glass media is recyclable, making it cost-effective and eco-friendly. You can also use it on most metals, including stainless steel.
It is important to note there are some important considerations. Glass bead blasting needs to be done in a temperature-controlled environment. Hot and humid locations can clump the media, making it unusable. You must always wear gloves after processing parts as fingerprints can and will oxidize on certain materials, causing the need to re-blast. Also, certain materials will oxidize or rust if not processed right away and left in a humid environment.
About the Author
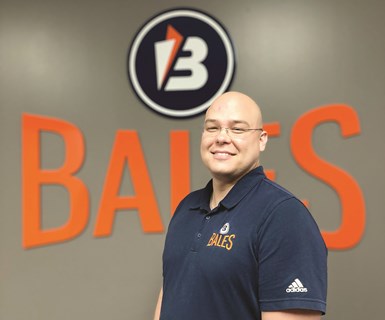
Magrone
Photo Credit: Bales Metal Surface Solutions
Angelo Magrone
Angelo Magrone is operations manager for Bales Metal Surface Solutions. Visit balesusa.com.
Related Content
A Chromium Plating Overview
An overview of decorative and hard chromium electroplating processes.
Read MoreChoosing and Troubleshooting Copper Electroplating Processes
Learn more on this inexpensive and highly efficient process.
Read MoreProducts Finishing Reveals 2023 Qualifying Top Shops
Each year PF conducts its Top Shops Benchmarking Survey, offering shops a tool to better understand their overall performance in the industry. The program also recognizes shops that meet a set of criteria to qualify as Top Shops.
Read MoreAutomated Electroplating Systems
Simultaneous engineering reduces energy and resource consumption.
Read MoreRead Next
Coping With Staffing Shortages
Tom Mastalerz, business development manager at Columbia Chemical, discusses strategies for optimizing operational efficiencies to help combat staffing shortages.
Read MoreUsing Ion Exchange in Trivalent Chromium Systems
Shane Moore of Pavco discusses the role of ion exchange technology in trivalent chromium systems for maintaining a consistent deposit.
Read MoreLonger, Cleaner Plating Bath Life
Angelo Magrone of Bales Metal Surface Solutions suggests adding an agitation and filtration system to keep plating pretreatment tanks cleaner, longer.
Read More