Non-PFAS Wetting Agents for Decorative Chromium(VI) Plating
This article is based on a presentation given at NASF SUR/FIN 2022, in Rosemont, Illinois, in Session 6, Responses to PFAS / PFOA. It follows the case study of three facilities’ conversion from PFAS-containing wetting agents to non-PFAS equivalents, eliminating PFAS and moving forward with a smaller and more sustainable environmental footprint. The journey of conversion from PFAS-containing wetting agents in both chromic-sulfuric etch and hexavalent decorative plating tanks can be complicated and winding due to deep rooted standard industry practices, as well as state and federal regulations. Outlined here is a clear course of action that led to eliminating PFAS from the facilities’ wetting agent strategies.
A Paper* based on a Presentation given at NASF SUR/FIN 2022 (Rosemont, Illinois)
by
Paul Madden, CEF*
Product Marketing Manager for Decorative and POP Applications
Atotech USA LLC
1750 Overview Drive
Rock Hill, SC USA
Editor’s Note: The following is a paper based on a presentation given at NASF SUR/FIN 2022, in Rosemont, Illinois on June 7, 2022, in Session 6, Responses to PFAS / PFOA. A pdf of this article can be accessed and printed HERE; the complete Powerpoint presentation is available by clicking HERE.
ABSTRACT
Introduction
This paper closely follows the case study of three facilities’ conversion from PFAS-containing wetting agents to non-PFAS equivalents, eliminating all new additions of PFAS and moving forward with a smaller and more sustainable environmental footprint. The journey of conversion from PFAS-containing wetting agents in both chromo-sulfuric etch and hexavalent decorative plating tanks can be complicated and winding due to deep rooted standard industry practices, as well as state and federal regulations. Outlined here is a clear and direct course of action that led to eliminating PFAS from the facilities’ wetting agent strategies. In recent months, these new wetting agents have been installed and tested in multiple facilities across the US. This presentation follows three of those facilities and highlights their experiences.
Reasons for PFAS conversion
Why is the Cr(VI) plating industry so active in converting to non-PFAS mist suppressant products? Multiple reports from various facilities indicate that pollution liability insurance is becoming harder to find. Some facilities are reporting they have not been quoted because of their use of PFAS.
There is uncertainty of the future of regulations. Currently in the works is the PFAS Action Act, that would allow the EPA to designate per- and polyfluoroalkyl substances as hazardous. Designating these compounds as hazardous would have a major effect on disposal, transportation and handling of these products. Further, there is the PFAS Strategic Roadmap, which sets timelines by which the EPA plans to take specific actions to safeguard public health, protect the environment and hold polluters accountable. Finally, the Preliminary Effluent Guidelines Program Plan 15, will commence a rulemaking process to establish standards for PFAS in wastewater discharges focusing on chromium plating, chemical manufacturers and formulators.
There is the potential for additional long-term post-wastewater treatment costs. This could be carbon units polishing your discharge or remediation of local ground water. Finally, there is the availability of alternative and sustainable technology, a working non-PFAS alternative.
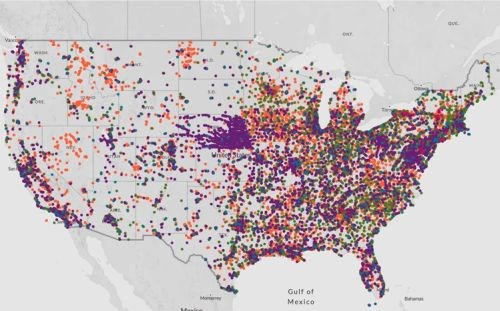
Figure 1 – Suspected industrial discharges of PFAS
Source: EWG - https://www.ewg.org/interactive-maps/2021_suspected_industrial_discharges_of_pfas/map/
Continuing with this thought, Fig. 1 shows a map assembled by the Environmental Working Group, EWG, an environmental activist group specializing in research and advocacy in many areas, including drinking water pollutants. The map shows all suspected industrial dischargers of PFAS compounds. Not all of these dots are plating or finishing facilities, and many are from other industries such as gas stations, airports, paper/textile, airport bases, wherever PFAS could be discharged. This is an interactive map that allows one to scroll, zoom, and click for more information about each dot. Clicking a dot would display information about that facility and the suspected nature of the PFAS discharge. Significantly, the map even lists suspected PFAS dischargers.
Non-PFAS chemistry
A proprietary non-PFAS based surfactant** has been formulated for use in chromium plating baths. It consists of a two-component system which is added directly to the bath. Both additives reduce surface tension; one additive forms the foam blanket, while the other controls the foam blanket characteristics. The ratio of the two components can be tailored for each application. The bath is controlled by surface tension and/or foam height measurements. A fully converted bath operates around 40-45 dynes/cm. The material breaks down with time and causes no negative impact on bath performance. Adds are made by time, not ampere-hours.
Non-PFAS conversion case studies
1. Bolta US***
This plating facility is a large decorative plating company that supplies the automotive market. The plating line is capable of producing 700k to 1 million m2/year. The line has five chromium tanks, each with a volume of 9,000 L (2,400 gal). Bright and satin nickel finishes are produced for both interior and exterior parts. Bolta worked with the Alabama Department of Environmental Management and EPA Region 4 during the conversion.
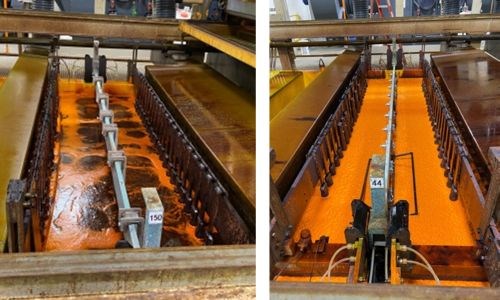
Figure 2 – Comparison of control methods: (L) Conventional PFAS bath; (R) Non-PFAS bath.
For the slide conversion, Bolta first discontinued additions of PFAS-containing wetting agents to the decorative chromium tanks. Compliance was demonstrated by monitoring surface tension and exhaust scrubber operation. The surface tension was allowed to increase to 40 dynes/cm before the conversion began, in order to reduce interaction of the old and new processes. Once the surface tension reached 40 dynes/cm, dosing the new system into the bath began. During the first weeks, the feed rates were adjusted while the material transitioned, while surface tension, foam formation and foam height were continuously monitored. The change in bath appearance is evident in Fig. 2.
In less than one year, Bolta successfully navigated the conversion process and is fully converted to non-PFAS wetting agents in both the etch and decorative chromium tanks while maintaining high quality, workplace and environmental standards.
2. Allied Finishing†
Allied Finishing is automotive decorative plater with a plating line capable of producing ~50,000 m2/year. There are three chromium tanks with a volume of 5000 L (~1,300 gal) each. Allied produces bright nickel-chromium parts for the automotive industry. During the conversion, the company worked closely with the Michigan Department of Environment, Great Lakes and Energy (EGLE).
The conversion involved a new make-up with one tank and slide conversions with the other two tanks on the line. Compliance was demonstrated by monitoring surface tension and exhaust scrubber operation. As production was started with the non-PFAS wetting agent, the process was continuously monitored for surface tension, foam formation and foam height.
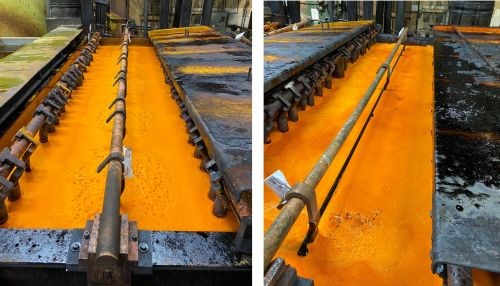
Figure 3 – Comparison of Non-PFAS baths: (L) New makeup versus (R) Slide conversion after two weeks of operation.
Once the new make-up was operating satisfactorily, the customer discontinued additions of the PFAS-containing wetting agents to the two tanks slated for slide conversion. As with the Bolta conversion, the slide conversions involved allowing the tank surface tension to increase to 40 dynes/cm before the chemical conversion began to reduce interaction of the old and new wetting agents. Again, addition of the new chemistry to the tanks was begun after reaching the 40-dynes/cm surface tension. Feed rates were closely monitored and adjusted as required, and the system was monitored for surface tension, foam formation and foam height. Figure 3 shows the chromium tank in the new bath make-up (L) and one from the slide conversion after operating for the first two weeks (R).
3. North Star Plating††
North Star Plating is an after-market decorative automotive plater, with a plating line capable of ~120,000 m2/year from one 5,700 L (~1,500 gal) chromium tank. They produce bright nickel-chromium automotive parts. Here, the single tank underwent a slide conversion. The system operated without an exhaust scrubber, and compliance was demonstrated by monitoring surface tension. North Star worked closely with the Minnesota Pollution Control Agency (MPCA) and EPA Region 5.
The slide conversion procedure was undertaken as with the other plants, with surface tension allowed to increase to 40 dynes/cm, after which the new system adds were begun. Feed rates were adjusted as required during the first few weeks, and the process was continuously monitored for surface tension, foam formation and foam height. Figure 4 compares the operational characteristics during the first 90 seconds of operation.
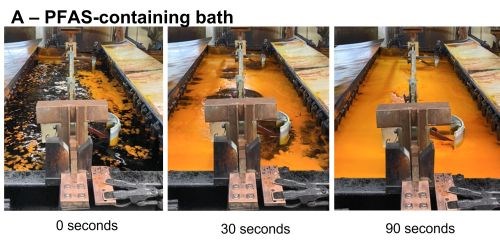
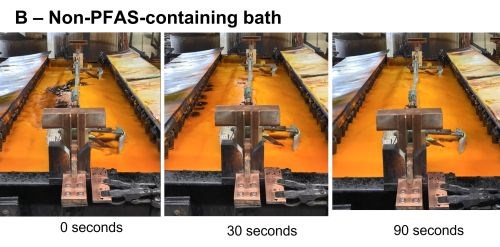
Figure 4 – Comparison of start-up for (A) PFAS- and (B) Non-PFAS chromium baths.
Conversion and testing
Prior to any conversion to eliminate PFAS, there are regulatory procedures to be followed. The customer’s air permits would be reviewed to determine if permit modification was required. If required, a dialogue with the local EPA region would ensue, with a permit modification proposal sent to that local regional office. The dosing equipment and chemistry would be coordinated and a stack test for permit modification scheduled.
At the start of the conversion, site-specific surface tension and/or foam height and/or scrubber exhaust would be monitored and, after reaching steady state, a stack test and a Personal Exposure Limit (PEL) test would be performed. The results and the site-specific control method would be reported to the local EPA region, at which point, a new permit would be issued.
Emissions testing
Due to transition of the decorative chromium bath to an elevated surface tension of 40-47 dynes/cm, a new air permit was required in all three case studies. To re-permit, a Method 306 Stack test was required to demonstrate compliance. All three lines passed the chromium exhaust emissions requirement for their region. Additionally, an OSHA Personal Exposure Limit (PEL) test for chromium was also undertaken to ensure safe conditions for line operators. All three lines passed the exposure limits required as well. The test results are shown in Table 1.
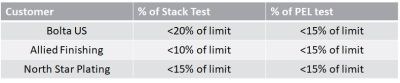
Table 1 – Stack (Method 306) and PEL test results for the three lines converted to non-PFAS operation.
Summary
In summary, the three customers have been pleased with the transition away from PFAS-based wetting agents, and PFAS is no longer purchased and in their facilities. All shops have or working towards new permits from regulators allowing for production by site-specific surface tension, site-specific foam height, by exhaust scrubber or some combination. They are no longer a part of the continued-use PFAS debate. Indeed, conversion has begun in EPA regions 2, 3, 4, 5, 6, 7 and 9. The pathway from PFAS-based wetting agents is available, allowing chromium platers to stop introducing this chemical of concern into their facility.
About the author

Paul Madden is Product Marketing Manager for Decorative and POP Applications at Atotech USA LLC, and is based in Minneapolis, Minnesota.
*Compiled by Dr. James H. Lindsay, Technical Editor - NASF
* Corresponding author: Mr. Paul Madden, CEF
Product Marketing Manager for Decorative and POP Applications
Atotech USA LLC
Minneapolis, Minnesota
E-mail: paul.madden@atotech.com
Related Content
NASF's SUR/FIN 2023: Bringing the Surface Finishing Industry Together
SUR/FIN 2023 is an opportunity for those in the surface finishing industry to expand their knowledge, expertise and network.
Read MoreDevelopment of a Novel Hexavalent-Chromium-Free Aluminum Sacrificial Paint
Hexavalent chromium is a known carcinogen, repro-toxin, and mutagen. Its elimination is of high importance to the aerospace industry, which has struggled to find high performing alternatives. Legacy aluminum sacrificial paints have traditionally utilized hexavalent chromium to prevent corrosion and coatings which are equal to or better than have been difficult. This first paper discusses the novel process from the supplier point-of-view.
Read MoreTin-Zinc Alloy Electroplating and Its Corrosion Behavior
An NASF/AESF Foundation Research Program Retrospective
Read MoreRead Next
Episode 45: An Interview with Chandler Mancuso, MacDermid Envio Solutions
Chandler Mancuso, technical director with MacDermid Envio discusses updating your wastewater treatment system and implementing materials recycling solutions to increase efficiencies, control costs and reduce environmental impact.
Read MoreA ‘Clean’ Agenda Offers Unique Presentations in Chicago
The 2024 Parts Cleaning Conference, co-located with the International Manufacturing Technology Show, includes presentations by several speakers who are new to the conference and topics that have not been covered in past editions of this event.
Read MoreMasking Solutions for Medical Applications
According to Custom Fabricating and Supplies, a cleanroom is ideal for converting, die cutting, laminating, slitting, packaging and assembly of medical-grade products.
Read More