Understanding Infrared Line-of-Sight
Marty Sawyer of Trimac Industrial Systems offers insights into using infrared to accelerate your powder coating curing operations.
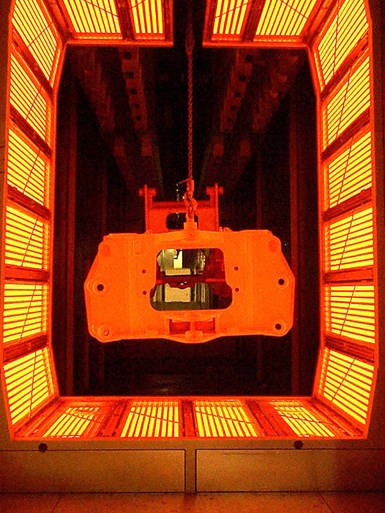
An infrared boost oven can accelerate the curing process so that less time in a cure oven is needed.
Photo Credit: Trimac Industrial Systems LLC
Q: I am considering using infrared for my process and I am concerned about line-of-sight issues. What exactly is this and is it an issue in a powder coating operation?
A: Great question! To understand line-of-sight, you first must understand infrared, which is basically light energy. It is part of the electromagnetic scale just below visible light. When you stand in the sun, you feel the line-of-sight energy of warmth. When you move to the shade, you feel the line-of-sight energy being blocked. In process heating, line-of-sight is the ability of the infrared energy to see the part. When a part has a complex shape, interior portions can be shielded from the light energy basically restricting the light from “seeing” all surfaces of the part, thereby creating a line-of-sight challenge.
If light energy cannot see all areas of the part, does that mean infrared will not work on anything other than a flat part? In theory that is correct because light cannot see around corners. However, in real-world applications, infrared can be used to heat and cure even complex weldments.
To get the benefits of infrared on a complex part, another part of heat transfer physics, conduction, plays a huge role. Conduction is transferring thermal energy through direct contact with matter. If you put a metal poker in a fireplace and leave it, the heat will “conduct” up the handle. Most commonly in powder coating, convection heat is used to cure complex shapes. The oven’s hot air does not bend around the corners of the part either, but the length of time allows conduction to help the part cure itself. The heat transfers via conduction into the hidden areas to cure anything the hot air cannot easily reach. With infrared, you can accomplish the same result on complex parts, only faster also through conduction. For instance, a gas catalytic oven is typically 3X faster than convection, but a complex weldment can still be cured through the assistance of conduction. With electric infrared, the process can be up to 10X faster than convection cures, however, the speed reduces the time for conduction to play a role as the part is not in the oven long enough.
Another consideration is how are you considering using infrared in your line? In a boost or gel application, it is typically not a major issue. The point of a boost is to accelerate the curing process so that less time in a cure oven is needed. The only way to speed conduction is through higher temperatures so a boost will drive more heat into a part much quicker than the convection oven can. Even if there are line-of-sight restrictions, the point is to accelerate conduction so those issues will typically be resolved in the cure oven. A boost or gel oven, though, still should be designed to ensure infrared energy coverage around the part to limit the line-of-sight issues. The better coverage you have, the less this will be an issue. If you are considering a cure application using infrared, line-of-sight can pose a bigger challenge. If the products are basically flat, you have no line-of-sight challenges, so cure is easily and quickly attained. If your parts have a complex shape, then your materials handling may be of assistance such as rotating the part in an overhead or chain-on-edge configuration. If the parts are not moveable, then you need conduction to also play a role. You still should be able to cure the product in about a third of the time vs. convection and possibly faster.
Another consideration affecting line-of-sight is infrared heater design. You would think the hotter the heater, the faster the process would work, right? Well, it’s a bit more complicated than that. Regardless of how much infrared energy you direct toward a part, what really matters is how much energy gets absorbed. Hotter is not always better because the energy is more likely to be reflected off the part vs being absorbed into it. The rate of infrared absorption of organic matter is in the medium to long wavelengths (300°F-1500°F). All infrared heaters emit infrared energy at their designed temperature/wavelength (temperature is inversely related to wavelength). For instance, gas catalytic emits in the 300°F-1,000°F range (long wavelength) and electric infrared is typically designed to emit at 800°F-4,000°F (medium to short wavelength). At the shorter wavelengths, the reflection of energy typically also goes up. If the energy only gets partially absorbed, then line-of-sight is even worse.
Bottom line, line-of-sight is an issue and must be part of the consideration in using infrared to accelerate your powder coating operation. To understand how it might affect your parts, you should work with an experienced infrared oven designer and have them perform tests in their lab. Using an oven temperature logger, the impact of the infrared energy on areas that might have line-of-sight issues can be probed for exact results. With data, you will know how infrared can be successfully incorporated into your line.
About the Author
Related Content
Curing Oven Basics
Simply heating up the substrate does not cure the coating. There are many variables to consider when choosing the best cure oven for your application...
Read MoreHow Not to Cure Powder on MDF
Mike Chapman, chief strategic officer at WolfRayet, an industrial oven provider for heat-sensitive substrates, discusses the correct procedures and common pitfalls when curing powder coating on MDF.
Read MoreThe Powder Coating Process
Powder coating is one of the most durable finishes that can be applied to industrial manufactured products, and offers excellent corrosion protection and is very safe because of its lack of volatile organic compounds. To understand the powder coating process you should start with the fundamentals.
Read MoreData Logger Helps Industrial Ovens Cut Energy Costs
Industrial Physics' encourages customers in the industrial coatings sphere to consider the energy saving properties of its oven logger kits.
Read MoreRead Next
Powder Coating 4.0: Smarter, Faster, More Efficient and Connected
New tools reduce cost and waste, lower manufacturing footprint of powder coating operations.
Read MoreThe 2024 Ford Mustang: All the Colors Available
Although Chevrolet has announced the end of the Camaro and Dodge is offering “Last Call” editions of the Charger and Challenger, the Ford Mustang is launching to its seventh generation.
Read MoreEpisode 42: An Interview with Robin Deal, Hubbard-Hall
Hubbard-Hall wastewater treatment specialist Robin Deal discusses the latest trends in wastewater management.
Read More