Be Prepared: Managing Environmental Inspections
Is your shop ready for an environmental inspection? Preparation and documentation can help minimize your facility’s risk of noncompliance.
Q: My facility takes environmental regulations very seriously. What advice do you have for working with inspectors?
Violations identified during an inspection can result in significant penalties and costs. Fines for a single violation of hazardous waste container requirements may be as high as $54,000 per day per container, and often, EPA requires “mitigation” costs to be paid to minority neighborhoods for any environmental impacts. While inspections cannot be prevented, it is important for surface finishers to manage the inspection within legal guidelines.
Scope of inspections
Surface finishers diligently guard against environmental impacts. Air emissions are monitored and minimized; wastewater is treated in multi-million-dollar treatment systems to meet categorical and water quality-based effluent limits; and solid wastes are subject to stringent container management requirements including labeling, inspection and recordkeeping provisions.
In 2015, EPA promulgated guidance on how regulators should inspect facilities for compliance with environmental regulations. The guidance allows for “Full Compliance” or “Partial Compliance” inspections: the former involves a complete review of monitoring systems, recordkeeping and compliance for a specific regulatory program, while the latter focuses on regulatory requirements for a specific piece of equipment or process.
Inspections may be triggered by schedule or due to complaints. For example, most surface finishers are large quantity generators (LQG) of hazardous waste and the guidance directs EPA to inspect at least six LQGs in each state annually and the state to inspect 20% of the LQGs during the same calendar year. Complaints (anonymous or named) require inspection unless it is duplicative. Facilities located near areas designated “environmental justice concerns” will be targeted by EPA during the next 4 years; these are areas where EPA believes pollution from a facility has a “disparate impact” on populations or subpopulations of race, national origin, religion or “socioeconomic” levels.
Managing the inspection
The keys to managing any inspection are preparation and documentation. Each may minimize a facility’s risk of significant noncompliance and reduce penalties if noncompliance is discovered.
Every electroplating business should develop a pre-inspection plan. A pre-inspection packet should include a guest log-in sheet/identification procedures, copying services, camera or video device, sampling equipment for solid waste and wastewater, and PPE requirements list. The facility should require inspectors to show identification and any HAZWOPER (Hazardous Waste Operations and Emergency Response) certifications. The proper person should be onsite during the inspection; if they cannot be there, explain the inspection will not be complete without them and request it be delayed until they can arrive. Prior to initiating the inspection, ask what the inspector is there to see: this is important in order to lock down the exact scope of the inspection. Key EHS personnel should be trained on the pre-inspection process.
Managing the inspection itself is equally important. Take the inspector or inspection team to see the areas requested during the pre-inspection meeting — and only those areas. Do not leave the inspector during the inspection and make sure to duplicate any photographs taken by the inspector, and split samples. This information may be useful for contested citations.
Finally, wrap up the inspection with a post-inspection meeting. This is the most important part of the process. It gives the facility an opportunity to minimize the scope of violations. Ask the inspectors what, if any, violations they observed. The answers will be helpful later if new or different claims are made by the inspectors during an enforcement process.
Conclusion
EPA and States have broad authority to perform inspections. EPA guidance sets boundaries for the inspections, but industries should understand the purpose of all inspections is to accumulate evidence of non-compliance. Companies can prepare in advance to minimize the scope of inspections by developing Pre-Inspection Plans (including collecting necessary tools for the inspection), managing the actual site visit, and asking the inspectors what, if any, violations they observed. All companies, including surface finishers, can reduce the chances of a “runaway” inspection by careful planning.
About the Author
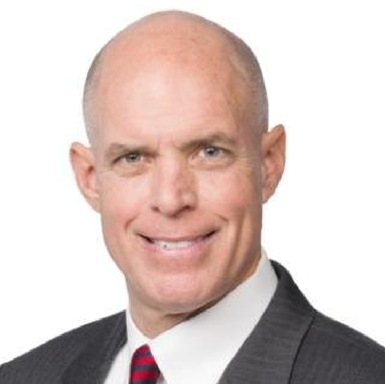
Ethan Ware
Ethan is a partner at law firm Williams Mullen. He represents businesses and industries in environmental and health and safety legal matters. Visit williamsmullen.com.
Related Content
California Public Hearing to Decide Fate of Hex Chrome Plating and Anodizing
Metal Finishing Association of California urges all members of the metal finishing community to submit comments prior to the hearing.
Read MoreHexavalent to trivalent chromium — the environmental benefits
Regulatory pressures to switch from hexavalent chromium to trivalent alternatives are a growing concern for many finishing operations. In this Products Finishing Ask the Expert clinic, Brittany McKinney of Pavco discusses the environmental considerations driving these regulations.
Read MoreHow to Maximize Nickel Plating Performance
The advantages of boric acid-free nickel plating include allowing manufacturers who utilize nickel plating to keep up the ever-changing regulatory policies and support sustainability efforts.
Read MoreCalifornia Looks to Finalize Rule Phasing Out Hexavalent Chromium Plating Processes
California will hold a public hearing January 27, 2023 on its new state rule to phase out hexavalent chromium plating and anodizing.
Read MoreRead Next
Education Bringing Cleaning to Machining
Debuting new speakers and cleaning technology content during this half-day workshop co-located with IMTS 2024.
Read MoreEpisode 45: An Interview with Chandler Mancuso, MacDermid Envio Solutions
Chandler Mancuso, technical director with MacDermid Envio discusses updating your wastewater treatment system and implementing materials recycling solutions to increase efficiencies, control costs and reduce environmental impact.
Read MoreDelivering Increased Benefits to Greenhouse Films
Baystar's Borstar technology is helping customers deliver better, more reliable production methods to greenhouse agriculture.
Read More