Development of a Novel Hexavalent-Chromium-Free Aluminum Sacrificial Paint
Hexavalent chromium is a known carcinogen, repro-toxin, and mutagen. Its elimination is of high importance to the aerospace industry, which has struggled to find high performing alternatives. Legacy aluminum sacrificial paints have traditionally utilized hexavalent chromium to prevent corrosion and coatings which are equal to or better than have been difficult. This first paper discusses the novel process from the supplier point-of-view.
A Paper* based on a Presentation given at NASF SUR/FIN 2022 (Rosemont, Illinois)
by
Bruce McMordie**
Coatings For Industry, Inc. (CFI)
Souderton, PA, USA
Editor’s Note: The following is a paper based on a presentation given at NASF SUR/FIN 2022, in Rosemont, Illinois on June 7, 2022, in Session 1, Aerospace / Defense Response to REACh. This is the first of two papers on the development of hexavalent-chromium-free aluminum sacrificial paints, this one from the supplier point-of-view. A pdf of this article can be accessed and printed HERE; the complete Powerpoint presentation is available by clicking HERE. A concurrent second paper by Wiley, available at http://short.pfonline.com/NASF23Feb2, addresses the user point-of-view in terms of the process validation work by Rolls Royce Corporation.
ABSTRACT
Hexavalent chromium is a known carcinogen, repro-toxin, and mutagen. Its elimination is of high importance to the aerospace industry, which has struggled to find high performing alternatives. Legacy aluminum sacrificial paints have traditionally utilized hexavalent chromium to prevent corrosion and coatings which are equal to or better than have been difficult. Many attempts have resulted in failure. In this paper, a body of results will be shared substantiating efficacy of a leading replacement. Performance testing includes cyclic-synthetic-seawater (salt spray/humidity/ambient) corrosion testing, continuous neutral salt spray corrosion testing, cyclic salt spray / humidity corrosion testing, cyclic salt spray / heat / humidity corrosion testing, heat resistance testing, fluid resistances testing, adhesion testing, conductivity/resistivity, metallography, quality, stripping, and touch up. Normalized data will show the success of a hexavalent chromium-free aluminum sacrificial paint.
Introduction
Hexavalent chromium is a known carcinogen, repro-toxin, and mutagen. Its elimination is of high importance to the aerospace industry which has struggled to find high performing alternatives. Legacy aluminum sacrificial paints have traditionally utilized hexavalent chromium to prevent corrosion and oxidation of steels. Due to the high performance nature of these coatings, work to approve alternate coatings has been difficult. To date, most attempts have failed. The process of developing a novel hexavalent-chromium-free aluminum sacrificial paint will be summarized here, including the history, failures and key factors.
Chromate / phosphate coatings
In the 1950s, development of viable flight gas turbine engines was hindered by the lack of coatings to protect steels from salt corrosion and heat. Apart from aluminum-flake filled stoving enamels, there were few coatings that would remain well-bonded to steels at the temperatures being seen in these innovative designs.
In 1963, Teleflex Inc. (North Wales, PA) filed for a patent for a glassy, heat-curable, aqueous binder that combined phosphoric acid with 5-6 wt% chromic acid (50,000 to 60,000 ppm Cr+6).*** By 1965, Pratt, Allison (now Rolls-Royce), and GE were protecting steel shafts and compressor cases in their turbines with a coating of aluminum powder dispersed in this binder. The Al-filled slurry sprayed like a paint, yet when baked at 600°F, it limited oxidation and salt corrosion of steels up to 1000°F.
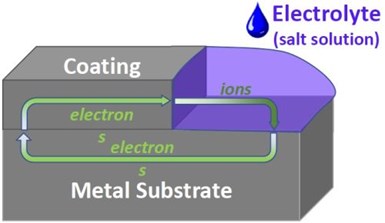
Figure 1 – Schematic of galvanically sacrificial coating.
Soon it was discovered that the aluminum-chromate/phosphate coating would become electrically conductive when it was baked for 90 minutes at 1050°F or lightly blasted with fine grit or beads. When conductive, the coating was galvanically sacrificial (Fig. 1).
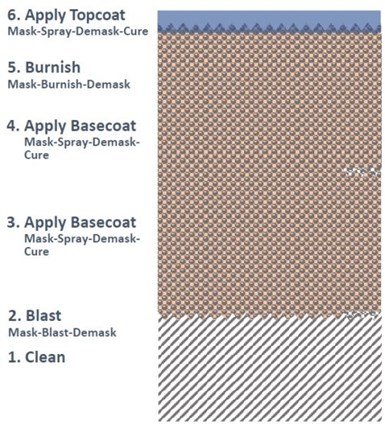
Figure 2 – Schematic of the chromate/phosphate system.
In 1970, Teleflex introduced a chromate / phosphate sealer for burnished (sacrificial) SermeTel™ W creating a sealed coating system, SermeTel™ 725, with longer life in high salt environments. In 1975, Teleflex’s Sermatech Division introduced Process 5375, mechanically polished smooth SermeTel™ W that increased flight turbine efficiency and reduced fuel consumption by as much as 2%. SermeTel™ 5380DP, a smoother, sealed and more corrosion resistant coating that did not need polishing, supplanted Process 5375 in 1980. Also that year, Coatings for Industry patented Alseal™ 500, which cured at temperatures low enough to allow its use on aluminum and HSLA steel.
By the 1980s, chromate/phosphates had become a firmly established standard and were specified by every major turbine engine OEM and many airframe OEMs (Fig. 2). A chromate/phosphate binder was utilized in sealers and other functional coatings, under several trade names.
Aluminum chromate/phosphate coatings (2 mil / 50 μm on steel) met the required specifications. Corrosion resistance per ASTM B117 was met with no rust over 1000 hr of 5% salt fog. Heat / salt corrosion resistance testing produced no rust after 10 cycles. Maximum continuous and peak heat resistance were 1050°F (566°C) and 1150°F (621°C), respectively. Subjecting the coating to either hot lubricating oil or hot deionized water had no effect, and a 90° bend test around a ¼” mandrel produced no flaking.
There was a hidden hazard, however. The heat-curable ceramic binder that Allen had patented combined chromium trioxide (chromic acid) and phosphoric acid. While trivalent chromium (Cr+3) was known to be a nutrient essential for human health, chromic acid (hexavalent chromium - Cr+6) was known to pose health risks. That is why OSHA limited Permissible Exposure Limits (PEL) for workers to no more than 0.1 mg Cr+6/m3, requiring protection and monitoring when there was >0.052 mg Cr+6/m3.
Elimination of hexavalent chromium
The simple goal was to remove hexavalent chromium from the coating system. Recognizing the risks posed by Cr+6, around 1990, companies began developing Cr-free alternatives to the Allen binder. In 1993, Solar Turbines was granted the first patent for a Cr-free aluminum-phosphate coating composition. It was stabilized with vanadium pentoxide (V2O5), a toxin. By 2011, sixteen U.S. patents had been granted for acid-phosphate binder chemistries containing no Cr+6 that could be used to make a heat-curable aluminum-ceramic. Unfortunately, every Cr-free acid-phosphate had/have limited shelf-life (no more than a few hours) and reacted with bare, blasted steel.
By 2000, Cr+6 in the water supply was indicted as the cause of increasing cancer rates in Hinckley, California. The fight to bring the company responsible for the contamination to justice was dramatized in the film “Erin Brockavitch” and the hazards of Cr+6 were no longer a secret. At the same time, airborne Cr+6 was linked to increased rates of lung cancer. A study published in 2004 estimated that exposure at 0.1 mg Cr+6/m3 led to an excess risk of lung cancer death that exceeded 1 in 10. In 2005, about one million U.S. workers were exposed to Cr+6. Thus, it was back to square one.
Blocked by patents on Cr-free acid-phosphate binders, Coatings for Industry (CFI), in 2001, developed a heat-curable aluminum-filled inorganic silicate (water-glass) slurry that could be baked to form an aluminum-ceramic coating. The single component slurry had a one-year shelf-life. It did not react with steels and, when cured, could be made electrically conductive and galvanically sacrificial by the same means now used for Al-chromate/phosphates. In 2003, CFI filed for a patent on its innovative slurry and in 2010, Praxair was granted a patent on its own aluminum-silicate. The patent for the CFI Al-silicate was finally issued in 2014.
At the same time, regulations became stricter. Acknowledging the risks of Cr+6, in 2006, OSHA lowered the PEL for Cr+6 to 5 μg/m3, a 20-fold reduction in the 8-hr limit per employee. Employers had to protect and monitor workers when exposure was a mere 2.5 μg of Cr+6 per cubic meter of air. The European Chemicals Agency (ECHA), classified chromium trioxide as a “substance of very high concern” and proposed to restrict its use in the EU. ECHA’s REACh regulations became law in 2017. Users the were required to be authorized (for a substantial fee) to import materials containing >1000 ppm of Cr+6, registered to use it and report how much they use (Al-chromate/phosphates contain 30K - 55K ppm Cr+6.).
DoD Efforts - Propulsion Environmental Working Group
Anticipating OSHA’s lowering of the PEL for Cr+6, in 2005, the US Department of Defense (DoD) established the Propulsion Environmental Working Group (PEWG), with the credo, “Industry and government leaders striving to insert clean, safe, and cost-effective sustainment technology improvements in the propulsion community.” PEWG’s goal was to produce "The Ultimate Green Engine" made with parts that lasted its designed lifetime, contained no toxic materials, and built, maintained and reworked without using or releasing any hazardous materials, with valuable components and/or materials recoverable at life’s end.
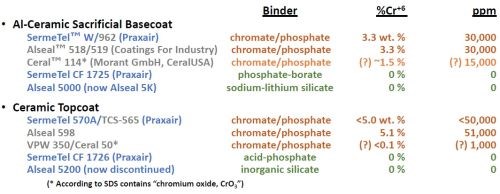
Table 1 – Aluminum-ceramic coatings circa 2005.
In 2005, there were a number of commercial aluminum-ceramic coating processes available with varying amounts of Cr+6 in their formulations, as shown in Table 1. Shelf life remained a problem with the alternatives.
Using specifications for Cr+6 slurries as a guide, PEWG sought a Cr‐free candidate(s) that matched SermeTe™l W’s perform-ance as a benchmark. Finding no Cr‐Free match in all tests, including Cr-free aluminum-phosphate and silicate systems (Table 2), PEWG sup-ported development of a “low Cr+6” Al‐chromate / phosphate.
Our efforts at CFI continued to focus on a system that was completely Cr+6-free. A proprietary system consisting of an aluminum-ceramic sacrificial basecoat using a sodium-lithium silicate binder (Alseal™ 5000, later referred to as 5K). Two topcoat sealers were considered: (1) Alseal™ 5200, a sodium-lithium silicate and (2) Alseal™ 5KTC, using Al+3-acid-phosphate chemistry.
The PEWG data in Table 2 shows instability of silicate-based topcoats in fluids. This is further shown in Fig. 3, at left, where the vapor from an open beaker of moderately warm water dissolved the sealer. On the other hand, Fig. 3, at right, shows that an acid-phosphate topcoat stabilized the same Al-silicate under identical test conditions.
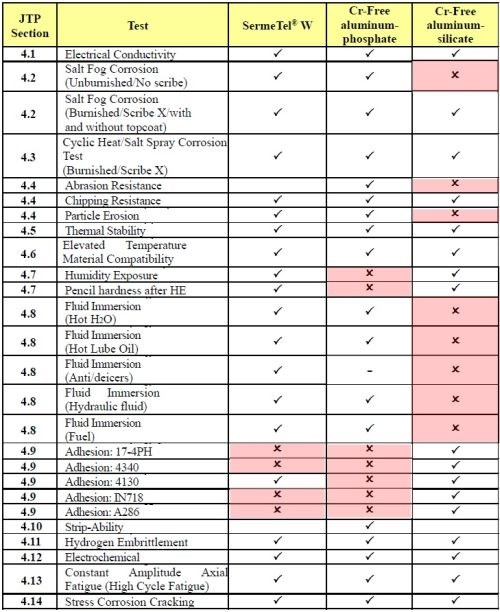
Table 2 – Pass/fail characteristics of PEWG analysis of aluminum-ceramic coating systems.
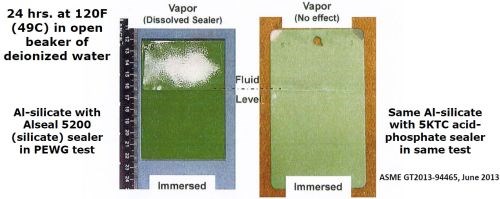
Figure 3 – Performance of Cr-free sealers in deionized water at 120°F (49°C).
Unfortunately, a Cr-free coating that had passed lab tests failed in a power generation turbine operating with wet compression. The failure led the OEM to develop a new laboratory test to screen the Cr-free systems.
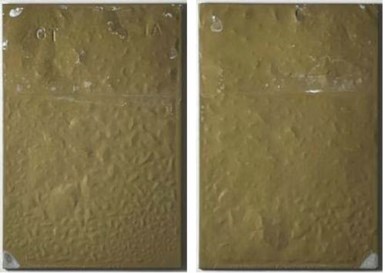
Figure 4 – Exfoliation failure of Cr-free Al-silicate basecoat, sealed with a Cr-free acid-phosphate topcoat in hot water immersion test.
It involved a 100-hr partial immersion in deionized water at 176°F (80°C) in sealed container. The result for the system in question, a Cr-free Al-silicate basecoat, burnished and sealed with a Cr-free acid-phosphate topcoat, is shown in Fig. 4.
Our laboratory looked at alternate approaches of using these new Al-acid phosphate sealers, keeping in mind the PEWG support of low Cr+6 chemistries with Cr+6 levels well below the REACh limits of less than 1000 ppm.
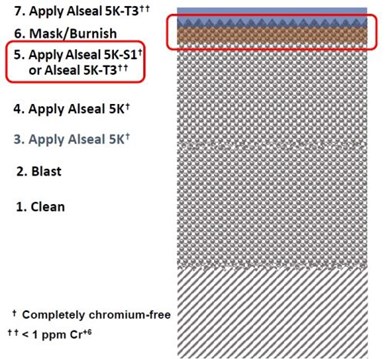
Figure 5 – Schematic of the REACh compliant systems.
The system schematically shown in Fig. 5 was the result. The Alseal™ 5K Cr+6-free aluminum-silicate basecoat was followed by immersion in a heat-cured acid-phosphate solution, which stabilized the basecoat in hot water or water vapor testing. Two chemistries were tested: (1) a completely Cr-free solution, Alseal™ 5K-S1 or (2) a very low Cr+6 (< 1 ppm) trivalent chromium acid-phosphate solution, Alseal™ 5K-T3. This step was followed by an abrasive burnish, which activated the cathodic response of the aluminum-silicate. Finally, a second application of the smooth acid-phosphate topcoat, the very low Cr+6 Alseal™ 5K-T3 containing trivalent chromium completed the process.
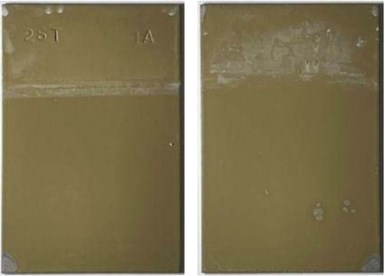
Figure 6 – Results of 1000 hr of hot water immersion test for Alseal™ REACh-compliant system.
Figure 6 shows the results after 1000 hr of hot immersion testing of this system in 176°F (80°C) deionized hot water, a ten-fold increase in test duration. No coating failure was observed.
Summary
Virtually Cr-free slurries have been developed, consisting of a completely Cr-free aluminum-ceramic sacrificial basecoat, based on sodium-lithium silicate chemistry (Alseal™ 5K) plus ceramic sealers, consisting of (a) a completely Cr-free aluminum-acid phosphate chemistry (Alseal™ 5K-S1) or (b) an aluminum-trivalent chromium acid phosphate chemistry (Alseal™ 5K-T3) containing less than 1 ppm Cr+6 well below the REACh compliance-limit of 1000 ppm. It appears that these nearly Cr-Free materials can be combined into multi-layer coating systems that are a safe alternative to aluminum sacrificial paints (ASPs) that contain hazardous chromium trioxide (hexavalent chromium) which are currently widely used in aerospace.
About the author

Bruce McMordie is Director of Alseal Operations at Coatings for Industry, Inc. (cficoatings.com) in Souderton, Pennsylvania. He has over 40 years’ experience developing and implementing coating systems to protect components in turbine and industrial equipment. He spent more than 30 years with Sermatech International (now Praxair Surface Technologies) and 10 years now with Coatings For Industry. Bruce holds 18 coating related patents.
*Compiled by Dr. James H. Lindsay, Technical Editor - NASF
** Corresponding author:
Bruce McMordie
Director, Alseal Operations
Coatings For Industry, Inc.
319 E Township Line Road
Souderton, PA 18964
Web: www.cficoatings.com
Phone: (315) 723-0219
E-mail: bmcmordie2@cficoatings.com
*** Charlotte Allen, “Inorganic Coating and Bonding Composition,” US Patent 3,248,251, April 16, 1966.
Related Content
A Smooth Transition from One Anodizing Process to Another
Knowing when to switch from chromic acid anodizing to thin film sulfuric acid anodizing is important. Learn about why the change should be considered and the challenges in doing so.
Read MoreTop Shop Emphasizes Dedication, Work Ethic
With a primary focus on aerospace and defense work, American Metaseal Corp. of Arbutus, Maryland, has qualified as a Top Shop on multiple occasions.
Read MoreNADCAP Shop Digitizes to Eliminate Paper Trail
Customizable ERP software has transformed a 27-year-old manual metal finishing job shop into a state-of-the-art paperless company with full digital traceability in about 10 months.
Read MoreAnodizing for Bonding Applications in Aerospace
Anodizing for pre-prep bonding bridges the gap between metallic and composite worlds, as it provides a superior surface in many applications on aluminum components for bonding to these composites.
Read MoreRead Next
Making Chrome Safe
A non-aqueous hard chrome alternative offers safe and environmentally sustainable functional and decorative chrome coatings.
Read MoreThe Continuing Battle Over Hex Chrome
The latest in the California regulatory battle over the phase-out of hexavalent chromium use in finishing operations.
Read MoreCalifornia Public Hearing to Decide Fate of Hex Chrome Plating and Anodizing
Metal Finishing Association of California urges all members of the metal finishing community to submit comments prior to the hearing.
Read More