Justifying Investments in Automation and Smart Solutions
Corey Sorrento of Carlisle Fluid Technologies discusses the long-term benefits and payoffs for investing in AI-driven technologies for your paint line.
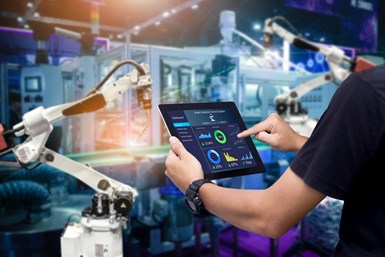
Q: We’re exploring upgrading our plural component systems to incorporate modules with “smart” features but are initially hesitant due to the up-front costs. What are some of the short- and long-term benefits of transitioning to next-gen components, and how can we quantify the ROI to justify the investment?
A: Introducing AI-driven technologies to your paint line yields many immediate and obvious advantages over traditional, user-controlled systems. Many of today’s systems can track inputs, from materials and solvents to compressed air, and optimize their usage to ensure the application meets specifications and any waste in the process is minimized. Higher-end systems can sense environmental conditions such as humidity and temperature and adjust viscosity near the point of atomization to provide the highest degree of precision and transfer efficiency. Time savings from automated purge and load sequences during color changes save labor hours, which equates to reduced downtime and increased production. Machine learning enables systems to anticipate potential issues and suggest preventative action, prolonging the life of components and limiting operation failures. Real-time, closed-loop feedback facilitates the delivery of repeatable and error-free results, bringing consistency to the quality of your finish and reducing the need for rework. Some systems can now monitor energy consumption and VOC emissions, which may suggest adjustments that contribute to corporate sustainability initiatives.
Assigning a dollar value to each of these can help you quickly calculate the overall impact, payback period, and long-term ROI of any proposed capital expenditure. In turn, these savings could directly translate to increased profitability for your business or be passed along to the end customer to give your brand a price-competitive edge in the market.
Q: Are the days of the human in-booth applicator numbered?
A: In recent years, it has been increasingly challenging to recruit, train and retain qualified finishing operators. Experienced professionals may be scarce in some areas or come at a premium. Often paint lines are challenged to maintain production levels with fewer resources, which may translate to higher workloads and more stringent productivity demands. Add the fact that human operators can introduce error into the process — as by nature, we may become distracted, fatigued, or overlook important detail — and the result could prove costly to a finishing operation.
From overuse of resins and solvents to imprecise ratios, wasted time mixing materials, the need for rework or scrap, and the risk of operator injury, the potential for inefficiency is great. Fortunately, the integration of automation in a system adds a level of control by removing the human variable in the equation, providing time, material, and labor savings, added safety in operation, and better consistency in results. Some automated systems feature cloud-based connectivity, allowing users to log in and instantly evaluate performance, manage operations, diagnose and troubleshoot issues, all from a remote location outside the booth. The data can then be exported in real-time or by batch for logging and analysis.
By freeing up these manual tasks, operators can turn their attention to more value-added efforts and focus on monitoring, analyzing and steering the overall process. While automation in in-plant finishing systems will continue to grow, there will always be a place for the operator in an ever-developing and ultimately more collaborative role alongside the supporting technology.
About the Author
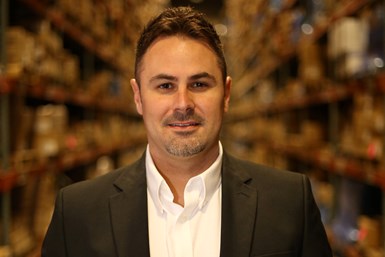
Corey Sorrento
Corey Sorrento is the global product manager for the mix, meter and flow as well as cure and convey product lines for Carlisle Fluid Technologies. Visit carlisleft.com.
Related Content
Zinc Phosphate: Questions and Answers
Our experts share specific questions about zinc phosphate and pretreatment
Read MoreFinishing Systems Provider Celebrates 150 Years, Looks to Future
From humble beginnings as an Indiana-based tin shop, Koch Finishing Systems has evolved into one of the most trusted finishing equipment providers in the industry.
Read MoreCoatings Plant Evolves with Market Trends
Expanding its focus from exclusively serving the RV industry, one of this company’s stand-alone coatings plant has successfully extended its services to additional markets.
Read MoreTTX’s Automated Conveyor Carrier System Offers Wireless, Flexible Operation
ACC system designed for reliable, consistent point-to-point movement of everything from small to heavy parts.
Read MoreRead Next
Digitizing Your Job Shop for Increased Production and Profitability
Dean Halonen of ERP software provider Steelhead Technologies discusses how digitizing your metal finishing job shops can help you achieve more production throughput and improve profitability.
Read MoreEpisode 32: An Interview with Bobby Haggard, TrinSoft LLC
A wide variety of ERP systems are on the market ranging from off-the-shelf solutions to custom programs. What should finishing operations keep in mind when exploring a new ERP solution?
Read MoreWhen to Introduce Automation Into Your Finishing System
Looking to increase productivity for your liquid coating operation? John Owed of Carlisle Fluid Technologies provides examples of how automation can help improve quality and efficiency for paint spray equipment.
Read More