The holidays are upon us, and so too is the closing of another year. I find myself reflecting on Products Finishing’s role in the industry, our friends in the community, and the opportunities that we’ve had throughout the year. My colleague Scott Walker, regional vice president for PF, always talks about the “privilege of representing this industry.” I find myself filled with a sense of gratitude and excitement as I look ahead to a new year of reporting on what’s in store for the finishing community. Here’s a look back at some of PF’s best stories of 2022 and some themes that set the table for 2023.
Getting perspective
2022 was a big year for Products Finishing. The return of travel afforded us the chance to reengage with the finishing community in person by attending conferences and tradeshows (including FABTECH, an incredibly well-received Electroless Nickel Conference and my very first IMTS), as well as by touring numerous facilities. Some of my favorite stories that we published in the magazine came from our time spent on the road. Here are a few highlights:
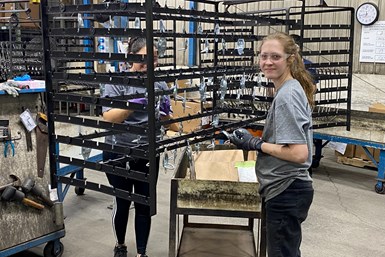
Professional Plating (Brillion, Wisc.)
Photo Credit: Products Finishing
Boasting zinc plating, an acrylic ecoating line, powder coating lines, wastewater treatment systems, and a lab with precision testing equipment, Professional Plating’s (Brillion, Wisc.) leadership sees its team as the company’s greatest asset, which is evidenced by the communal culture on the shop floor. The May 2022 installment of Products Finishing’s Top Shops Insider column offered a peek inside this winning finishing shop’s approach. short.pfonline.com/profpla1222
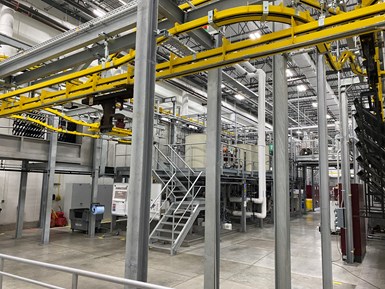
Brose (New Boston, Mich.)
Photo Credit: Products Finishing
When it comes to automotive components, quality, turnaround time and consistency are of utmost importance. These are the necessary hallmarks of companies that supply automotive OEMs. An excellent example of this is the electrocoating line at the Brose Group's New Boston, Mich. plant. The captive line is dedicated to coating the automotive seat components produced at the facility, but paint technologist Yolanda Watts MS, MBA, takes pride in running the line like a job shop — “a business inside a business.” In this feature article from the September 2022 issue of PF, we hear from Watts along with regional surface technology specialist Benjamin Hill, CEF, about the company's approach to ecoat. short.pfonline.com/ecoat1222
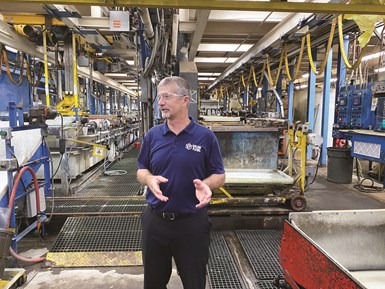
Varland Plating (Cincinnati, Ohio)
Photo Credit: Products Finishing
Varland Plating is a one-stop shop for barrel-plated parts, which the company has been churning out from its facility just north of downtown Cincinnati, Ohio, since 1946. Learn about the company’s offerings and recipe for success in the October 2022 installment of PF’s Top Shops Insider Column. short.pfonline.com/varl1222
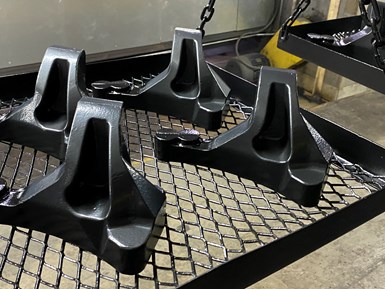
Winona Powder Coating (Etna Green, Ind.)
Photo Credit: Products Finishing
Winona Powder Coating (Etna Green, Ind.) has become one of the leading industrial powder coating providers for the Midwest and continues to emphasize new growth as it looks to the future. In November 2022, PF checked in with Winona for a look at the company’s successful approach to expanding its capabilities and finding new business. short.pfonline.com/winona1222
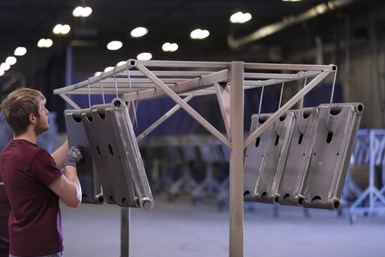
D&K Powder Coating
Photo Credit: Monte Consulting
Rooted in humble beginnings and an entrepreneurial spirit, D&K Powder Coating (Mankato, Minn.) got its start in 2013 and has grown its business from the ground up. The company recently found a new level of productivity by implementing ERP software from Steelhead Technologies. This story from November 2022 outlines how the new system allowed the company to instantly see improvements in profitability. short.pfonline.com/dk1222
Automotive
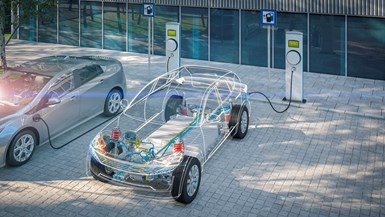
What new opportunities will emerge for finishers as EVs and hybrids claim a larger share of the automotive market?
Photo Credit: Getty Images
A lot has happened regarding trends in the manufacturing world in general and the finishing industry in particular. Growing consciousness of environmental responsibility and attempts to minimize reliance on fossil fuels is opening up new opportunities for electric vehicles (EVs) and new energy vehicles (NEVs). Such changes bring new finishing opportunities in the automotive and transportation industries. This story from the February 2022 issue of PF explores some of the ways coatings might enable emobility applications. short.pfonline.com/emobile1222
As automakers continue to make more investments in EVs and hybrid vehicles, what can finishers expect in terms of demand for finishes? In this Ask the Expert article from August 2022, Mark Schario of Columbia Chemical Corp. shares insights into the kinds of opportunities NEVs present for finishers. short.pfonline.com/ev1222
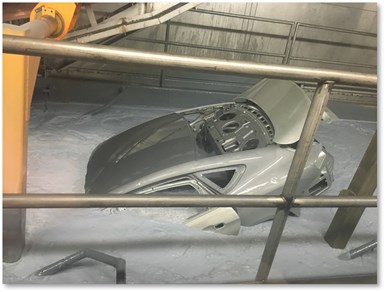
Low cure ecoat
Photo Credit: PPG
The growth of electrified vehicles in automotive naturally means increased use of different materials. Recent innovations in ecoat technology allow for an expanded bake window to enable the curing of diverse substrates of varying thicknesses. In this article from October 2022, Vivek Badarinarayana of PPG discusses expanded cure temperature ecoat solutions. short.pfonline.com/locure1222
Regulatory hurdles
While the coming year promises areas of opportunity for finishers, there remain plenty of challenges. The regulatory landscape for such substances as hexavalent chromium and PFAS chemicals has been front of mind for many finishers in 2022.
As hexavalent chromium phase-out deadlines in California loom large, hex chrome alternatives continue to gain attention. Trion Coatings (South Bend, Ind.) touts a new, non-aqueous, trivalent chromium chemistry called SAFE Chrome as an alternative for not only decorative, but some functional chrome applications. This feature from January 2022 offers a look at the solution. short.pfonline.com/chrome1222
Regulation of PFAS chemicals continues to increase.In this Ask the Expert article from the October 2022 issue of PF, Ethan Ware of environmental law firm Williams Mullen discusses some steps finishing operations can take to prepare. short.pfonline.com/pfas1222
Automation
To automate or not to automate... that is the question for many finishing processes. While automating the movement of material on a mechanical finishing line can be highly effective, automatically loading and unloading individual parts onto racks often requires numerous steps and a level of accuracy that is difficult to automate, particularly when handling parts of various shapes and sizes. So, what aspects of your operation make sense when targeting areas where you can find efficiency through implementing some sort of automation solution? In this feature article from the July 2022 issue of PF, industrial finishing line consultant Daniel E. Davitz examines some examples of when automation can help, and instances where a traditional approach remains the best one. short.pfonline.com/rack1222
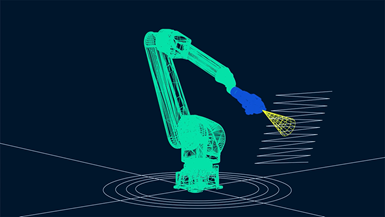
Omnirobotic’s technology enables robots to program themselves based on their environment and task, which has transformative potential for many finishing operations.
Photo Credit: Omnirobotic
Automation is touted as a potential solution for many challenges facing finishing operations — from seeking gains in efficiency and repeatability to addressing workforce shortages. But as with any change, many considerations have to be taken into account before going all-in on a robotics system. In the following story from July 2022, you'll get a look at a self-programming automation solution from robotics software startup Omnirobotic (Laval, Quebec, Canada) that could transform the way finishing shops consider robotics. short.pfonline.com/robo1222
To the future
As the finishing industry looks ahead to next year, there are plenty of challenges to meet head-on. But as the saying goes, in the midst of challenge lies opportunity. With the rising need for finishing of new EV parts and an infrastructure that can support them, advances in electronics, material innovations and an increase in production levels for additively manufactured parts, the opportunities for creative solutions to finishing different and complex parts will only continue to emerge. Are you ready?
Related Content
Powder Coating Overcomes Post Forming
Six Sigma methodology, open communication, and collaboration produce results for leading boat manufacturer.
Read MorePowder Coating 4.0: Smarter, Faster, More Efficient and Connected
New tools reduce cost and waste, lower manufacturing footprint of powder coating operations.
Read MoreLow-Temperature-Cure Powder Coatings Offer Unique Opportunities
An in-depth look at the advantages of low-temperature-cure powder coatings and the considerations for incorporating them into your process.
Read MoreTrends in Industrial Coatings
The benefits of new technologies in the industrial coatings market.
Read MoreRead Next
Masking Solutions for Medical Applications
According to Custom Fabricating and Supplies, a cleanroom is ideal for converting, die cutting, laminating, slitting, packaging and assembly of medical-grade products.
Read MoreDelivering Increased Benefits to Greenhouse Films
Baystar's Borstar technology is helping customers deliver better, more reliable production methods to greenhouse agriculture.
Read MoreA ‘Clean’ Agenda Offers Unique Presentations in Chicago
The 2024 Parts Cleaning Conference, co-located with the International Manufacturing Technology Show, includes presentations by several speakers who are new to the conference and topics that have not been covered in past editions of this event.
Read More