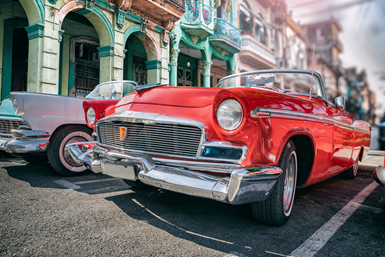
Some chrome looks different on cars than you once imagined. Decorative chromium plating comes in two different stripes – hexavalent and trivalent. Photo Credit: Getty Images
Picture this: Your car is totaled, and you are fighting back the urge to scream. You summon the humility to arrange to have your wife drive you to the local car dealership to look around for a replacement car. Feelings of anger, apprehension and excitement simultaneously permeate through your mind and body. You walk gingerly up each row of new cars, taking time to admire the sleek and aerodynamic engineering, the elegant and stylish craftsmanship of the leather upholstery, and the exquisite sparkle of the azure sapphire chrome trim.
Some chrome looks different on cars than you once imagined. This is a glimpse of the future of the automotive industry. Chrome has been on cars and in other commercial applications before movies could talk, but times, they are a changin’.
Decorative chromium plating, as you see on your car, faucets and tools, comes in two different stripes — hexavalent and trivalent. Each of these formulations contain chromium metal ions, but they exist in different valences or charged states because of the number of electrons each atom has lost due to a chemical reaction. Therefore, they perform differently when engaging with the plating reaction. Ultimately, they produce a similar but different deposit.
Trivalent chromium’s benefits
Trivalent baths have been around for many decades but are picking up more steam and incremental popularity in applications where they were once used less, such as in the automotive industry. Users are realizing that there are many benefits to switching from hex to tri. These benefits include better covering and throwing power, lower sensitivity to current interruptions, less stringent and rigorous wastewater constraints and prohibitions, more color options because of alloying capabilities, and better worker safety and health.
The coverage or covering power of a trivalent bath is often significantly better than its hex cousin. Looking at a Hull cell panel to evaluate the health of the electrolyte, standard hex-chrome solutions achieve 60% to 75% coverage of the panel from left to right or from high current density (HCD) to low current density (LCD), while a standard trivalent bath will achieve 80% to 90% of coverage on the panel. That’s a 20% improvement on average, which means that more complex geometries can be employed without the need for special conforming anodes or other ancillary current-assisting apparatuses.
The trivalent bath is also less sensitive to current interruption and excessive ripple (residual alternating current or AC that was not fully rectified by the rectifier). So, if you are not putting out the highest quality direct current (DC) or your rectifier is a bit worn and inefficient because of blown diodes and other potential interferences, the trivalent bath will be much more forgiving. If the parts are plating and then stop plating because of electrical anomalies,
Users are realizing that there are many benefits to switching from hex to tri. These benefits include better covering and throwing power, lower sensitivity to current interruptions, less stringent and rigorous wastewater constraints and prohibitions, more color options because of alloying capabilities, and better worker safety and health. Photo Credit: MacDermid Enthone
poor contact, polarization or other factors, the freshly plated deposit in the hex-chrome bath will passivate as hex-chrome deposits are naturally inclined to do. This is why they are often used as passivating agents.
But during a reaction in which we want to maintain the activity and receptivity of a plating surface, passivity is a counterproductive attribute. If chrome is plated on top of the passivated chrome, it produces a white, splotchy defect known as whitewash. Whitewash is more common with hex than tri and can be due to several factors not related to energy irregularities.
With trivalent chromium, wastewater treatment is often less costly and labor intensive because there is no need to reduce the hexavalent chromium ion to the more innocuous and benign trivalent chromium ion with a reducing agent such as sodium hydrosulfite or bisulfite, hydrazine, sulfur dioxide, ferrous sulfate or any of the other five possible reducers being used. Once the hexavalent chemistry has been reduced, a pH adjustment is needed to de-solubilize or crystallize and precipitate out the metal in the solution. This is a standard way to remove most metal cations from rinses and other processing solutions.
The trivalent chrome chemistry does not pose the same toxicological and carcinogenic concerns associated with hex-chrome, therefore, the potential litigation (a la Erin Brockovich) can be mitigated because in general, it means worker safety can be improved. It is still prudent to remain aware of the dangers of all chemicals, which is why the proper protocols must be enforced. However, the more extreme Occupational Safety and Health Administration (OSHA) personal protection equipment (PPE) standards can often be adjusted because of trivalent chrome’s more benign characteristics. Companies that prioritize sustainability and responsible practices can improve their reputation among customers, investors and monitoring authorities.
In a trivalent chrome bath, the metal concentration itself is generally only one-fifth of the amount in a standard hex bath, which means there is far less dragout of material and therefore far less wasted metal, which means less sludge, less chemical cost, less labor, and therefore a monetary savings to be reaped.
Drawbacks
As with any new system, there are associated pitfalls and disadvantages to trivalent chromium. These include, but are not limited to, strict control and maintenance requirements, more expensive equipment and extremely low tolerance for inorganic and organic contaminants.
The biggest drawback to trivalent chromium is how it handles metallic contaminants. A hexavalent chromium solution is highly resistant to copper, nickel, zinc, iron, aluminum and many other associated tramp metals, as well as some organic material. On the inorganic side of the scale, these baths are so robust as to be capable of withstanding thousands of parts
Although the chemistries are slightly different, trivalent chemistry is improving. Photo Credit: Products Finishing
per million (ppm) of many of these metals often without exhibiting any major signs of deposit deterioration both functionally and cosmetically. There is a point at which the hex bath will become slightly less efficient, will lose even more of its already poor covering and throwing power and will present and manifest other subtle issues oftentimes imperceptible to all but a trained eye.
With the trivalent chrome baths, a few ppm of any of these metals (1,000x less) will show palpable and definitive signs of degeneration and dilapidation related to plating speed, cracking, thickness, color, clarity, coverage, throw, and so on. The need for constant side-tank dummy plating and/or ion exchange resins is a necessary piece of the total equation when conducting trivalent plating. Those require time, energy, labor, equipment cost and material.
The hexavalent baths are one of the simplest baths. If a second catalyst isn’t being used, often fluoride or some sort of proprietary organic agent, then these baths only employ a single catalyst, the sulfate ion and the chromium metal.
The trivalent baths are often much more complex and have a multifaceted list of sometimes over a dozen proprietary products and dozens of ingredients captured within those products. These ingredients ensure the metal stays in the solution at an optimal pH range. pH is a major metric for optimally running a trivalent chrome bath, while the hex-chrome baths do not concern themselves with monitoring pH.
The many ingredients in tri baths also ensure proper brightness, color and hue along the current density spectrum, depositing the right hardness and wear/abrasion resistance and distributing thickness properly by maintaining a certain degree of throwing and covering power. Producing the right alloy, as all trivalents are alloy baths, is a critical duty of these ingredients.
Because trivalent chrome deposits are not pure chromium like their hexavalent chromium cousins, this is a double-edged sword because it can both add to the variegated color diversity of these baths and therefore to their ability to produce coatings with similar functional properties (hardness, lubricity, corrosion resistance). This is because a small amount of nickel, iron or vanadium may change the color from a bright blue to a full black; however, this means that the color can change quickly if the bath is not monitored frequently to ensure the presence of these good metallic ions at proper concentration, proper valence, proper solubility and proper orientation.
Hardness, and therefore abrasion and wear resistance of the trivalents, tend to be a little lower on the order of 750-850 HV (Vickers scale), whereas hexavalent chromium tends to be closer to between 850-1100 HV. Stress can
Continual monitoring and optimizing of the plating process is key to maximizing and continuing the highest quality, performance and efficiency of these solutions.
be either compressive or tensile with trivalent baths, but with hex baths, the deposits are always tensile and often more stressed than the trivalents; therefore, macrocracking is more of a possibility. Macrocracking is possible in the trivalents but more prevalent with hex baths, which is not only unsightly, but presents an adverse effect on the corrosion resistance since the cracks are large enough to be perceived without magnification. Therefore, they are deep, wide, prevalent and continuous, which is a recipe for problems related to oxidation and corrosion.
To change or not to change
When evaluating the advantages and disadvantages of moving from the hexavalent to the trivalent chromium plating solutions, it is important to take a comprehensive assessment and recognize the importance of training and education, as the learning curve can be steep. Pilot projects will help to concretize and make more tangible the realities of the plating process and its performance.
It is critical to work closely and collaboratively with chemical suppliers, equipment manufacturers, adjunct vendors and regulatory authorities to ensure a seamless transition. Engaging with customers to communicate the benefits of the switch and to address any concerns they may have is paramount. Continual monitoring and optimizing of the plating process is key to maximizing and continuing the highest quality, performance and efficiency of these solutions. This goes for any bath, but will certainly be a prominent factor in the way a trivalent bath is run.
Trivalent chrome baths allow for plating more highly complex geometry and will not be as impacted by electrical inadequacies and aberrations. Because hex-chrome has garnered a lamentable position within the surface finishing industry lately, the emphasis on greener technology is a prominent metric. The opportunity to offer a range of color options makes trivalent chrome more marketable and commercially lucrative, but with all these benefits comes the necessity to cultivate an assiduousness most likely not required with other baths, especially when compared with hex-chrome.
Upfront capital investment in equipment, labor and maintenance is unavoidable because the trivalent chrome bath is simply less forgiving and far more sensitive to anything foreign.
If you see the long-term benefits of making the move and are willing to tolerate and leverage some of trivalent chrome’s unique attributes, then you will also acquire its advantages.
About the Author
Adam Blakeley
Adam Blakeley is director of technical services for MacDermid Enthone. For more information, visit macdermidenthone.com.
Related Content
Products Finishing Reveals 2023 Qualifying Top Shops
Each year PF conducts its Top Shops Benchmarking Survey, offering shops a tool to better understand their overall performance in the industry. The program also recognizes shops that meet a set of criteria to qualify as Top Shops.
Read MoreTroubleshooting Alkaline Zinc
One of the most common problems that can arise when plating with alkaline zinc is an imbalance of brightener in the solution. In this helpful Ask the Expert article, Chad Murphy of Columbia Chemical discusses how different zinc metal concentrations and brightener concentrations can impact efficiency.
Read MoreLiquid Chrome Vs. Chromic Acid Flake
Contemplating how to continue offering chromic acid services in an increasingly stringent regulatory world? Liquid chrome products may be the solution you’re looking for.
Read MoreA Chromium Plating Overview
An overview of decorative and hard chromium electroplating processes.
Read MoreRead Next
Trivalent Hard-Chrome Process Eliminates Hex-Chrome Risks
Atotech’s BluCr is a trivalent hard-chrome plating process, offering the wear resistance and corrosion protection of hard-chrome without the hazards and risks of hexavalent chromium.
Read MoreHow to Choose Between Sulfate and Chloride-Based Trivalent Chromium
There are several factors to consider when choosing between sulfate and chloride-based baths for trivalent chromium plating. Mark Schario of Columbia Chemical discusses the differences and what platers should keep in mind when evaluating options.
Read MoreSwitching from Decorative Hexavalent Chromium to Trivalent
Pavco decorative team manager, Shane Moore, discusses the considerations you should keep in mind when contemplating switching from decorative hexavalent chromium to trivalent.
Read More