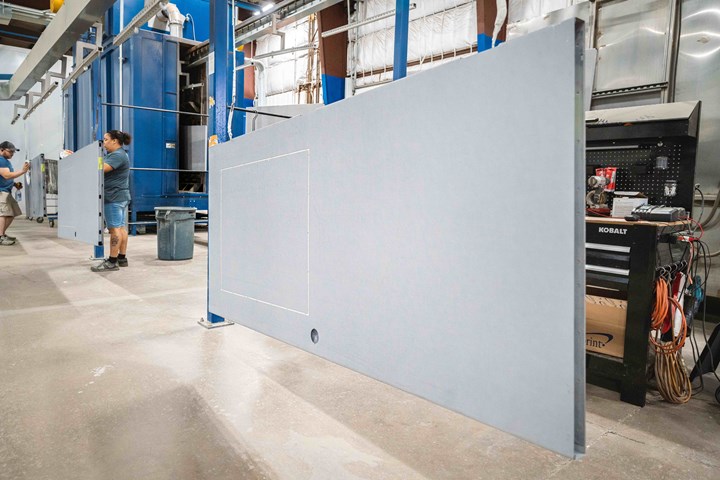
A door system waiting to receive treatment in the finishing line. Employees inspect other systems farther down. Photo Credit, all: Global Building Products
They say when one door shuts, another opens in its place. When Global Building Products (Global) was experiencing quality issues with the pre-finishing on its standard door and frame components, the company began its search for a key solution to provide the results it needed. However, the sensitive insulated material inside the company’s door system needed to be heavily considered when on the lookout for the next solution. Research turned up a few options, but one appeared to be the answer to Global’s predicament. To learn more, Global reached out to DVUV about UV powder coating.
Problems With Pre-Finished Parts
Established in 2002, Global produces, assembles and distributes commercial steel walk doors and windows, primarily for the commercial construction and pre-engineered metal buildings industries. Its door systems contain polystyrene and polyurethane — material that requires a temperature-sensitive application for finishing. Since its founding, Global has always provided its system components with a painted finish, but this practice was in jeopardy when paint issues, such as adhesion and peeling, increased over the course of a few years.
Prior to finding a new process, Global mostly used pre-finished/pre-painted components provided by a supplier using an electrostatic system to apply a water-based paint before being dried in an oven. In addition, Global also had the capability for customization on components and colors through a personal paint booth system. While this process also involved a water-based paint, the products from Global’s paint booth were air-dried after receiving treatment.
Search for a Solution
Before Global found UV powder, it tested other solutions, but overall, it was not satisfied with the results. The company investigated another electrostatic system utilizing water-based paints, but it feared the process would not solve the problem at hand. There was also an attempt at a higher heat powder coating process that didn’t end well — the core of the door slabs melted, highlighting a secondary problem. In addition to finding a solution to the quality problems, the company needed to find a solution that was temperature conscious.
UV powder coatings and application systems first came to be in the late 1990s. UV powder coatings are well-suited to replace solvent coatings, environmentally friendly, good for heat-sensitive materials where a traditional thermoset process is not and more efficient than other finishing processes.
Like traditional thermoset processes, the powder is deposited on the product before proceeding to the melt and flow treatment. However, the UV powder only sees this step in the process for around a minute. Following this step, the powder is cured using UV light in a matter of seconds. The swiftness of this application and processing becomes important when considering process efficiency and turn-around time on orders.
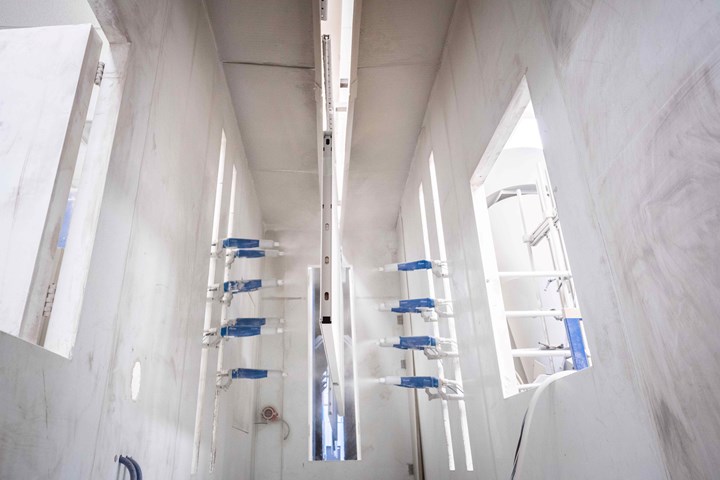
A door system being powder coated in a booth.
More important to Global’s case, however, was the fact that lack of time spent in the melt and flow step meant the heat-sensitive materials in its products were less vulnerable to developing quality issues internally.
A Door Opens, Opportunity Arrives
When Global discovered the UV powder coating manufacturer that would later provide the system, it was uncertain with how the process would work for the company.
“We specifically focused our search on low-temperature applied finishes,” says Andrew Carpenter, Global’s founder and president. “Our research led us to DVUV, and we made contact with them to inquire about the coating process.”
After learning about the potential benefits UV powder coating could provide, Global decided it was the way to go. The reasons for the switch lined up with what the company was seeking in its solution. UV powder offered a lower temperature process that would not affect the materials within Global’s products and a durable finish with less likelihood of quality issues. As added benefits, the speed and flexibility of the process also attracted Global, as well as the number of materials that could be powder coated through the system. And moreover, Global felt that adopting this finishing process would distinguish it in the industry.
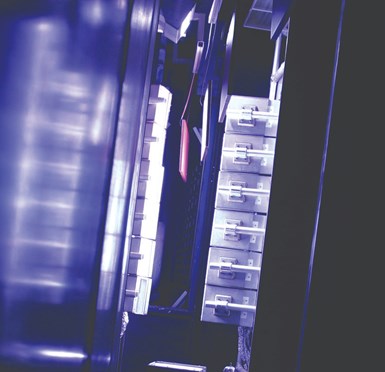
UV light is the final step in the finishing process, able to be completed in a matter of seconds.
Initially, the system install came with some challenges, especially during the Covid pandemic, but the UV powder manufacturer was able to support Global’s efforts for integration. Once the UV powder coating system was in place, things changed in Global’s day-to-day operations. The most significant change was the way Global ordered its components; it went from ordering pre-finished pieces to just ordering a “raw steel” format. The UV powder coating system enables the finishing of products in-house. While this sounds like it may have driven labor costs up, Global notes that the UV powder coating system requires less labor than the previous process.
Moving Onward and Upward
Part of the company’s goal when switching coating processes, in addition to resolving quality and service issues, was to extend its reach into different industries and markets and improve its products overall.
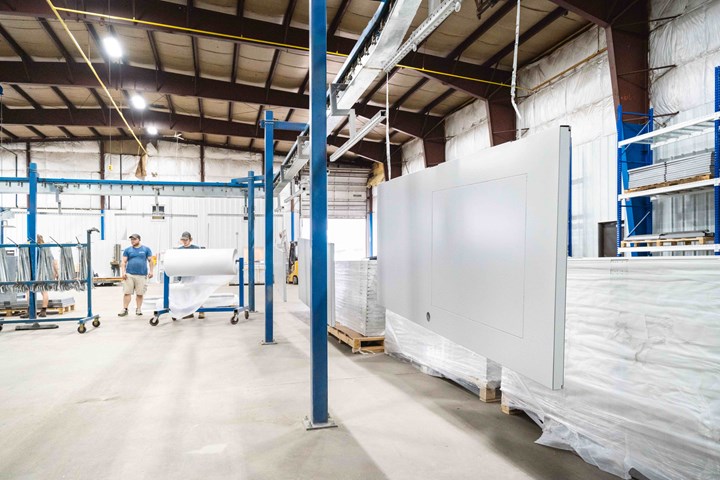
A door system finished with UV powder coating treatment.
“We originally purchased the UV powder coating system to provide a superior finish to our insulated steel door and frame components. The system provides us the ability to coat other heat-sensitive materials, such as MDF wood,” Carpenter says. “There is a very significant number of products in our area made with MDF wood, and this process has allowed us to service other industries.”
Other than the improvements to the finishes themselves, Global has also noted an advantage when it comes to the speed of the finishing process. The cost per piece has been reduced because of the speed. Along with the reduced cost, Global also points to the shorter turnaround on its custom color components, making for happier customers overall.
With volatile steel prices and supply chain shortages, it is important now more than ever for Global to stay competitive. The UV powder coating system has given rise for more opportunities in the company’s market.
When asked what product lines and industries he expects to see growth over the next year, Carpenter responds that the company has continued to see growth in its sales of steel doors and frames. “But we also are now powder coating MDF wood products, and we see that as the area where significant growth will occur.”
In January 2021, Global started Infinity UV, expanding business into finishing MDF. Now, in addition to its steel and aluminum products, Global utilizes UV powder coating for MDF products as well. All of the company’s door and frame systems are UV powder coated.
“We have only been using the UV powder coating process for a little more than a year and have experienced great results in our current product lines,” Carpenter says. “We are excited to look at other products, industries and materials that can also utilize this process as we continue to learn more about the UV powder coating process and its capabilities.”
Related Content
Concrete Reinforced Bars Built to Last
Not all corrosion-resistant materials for infrastructure are created equally. Epoxy-coated steel rebar has advantages that other materials used to prevent corrosion do not.
Read MoreArchitectural Powder Coating Mimics Natural Stone
AkzoNobel offers new stone effect powder coating for North American market.
Read MoreSurface Prep Solution for Rusted Rebar in Concrete
Julie Holmquist of Cortec Corporation discusses passivating corrosion on rebar and other reinforcing metals.
Read MoreLonglasting Nanotechnology Coatings Provide Barrier to Chemicals, Corrosion
The company moved its global headquarters from Houston in 2022.
Read MoreRead Next
12 Ways to Improve Your Powder Coating Quality
Often overlooked powder coating procedures that can help you elevate your quality, streamline your operations and improve your profitability.
Read MoreHow Not to Cure Powder on MDF
Mike Chapman, chief strategic officer at WolfRayet, an industrial oven provider for heat-sensitive substrates, discusses the correct procedures and common pitfalls when curing powder coating on MDF.
Read More