Episode 19: Brandon Acker, Titan Abrasive Systems
Brandon Acker of Titan Abrasive Systems offers insights for blasting best practices.
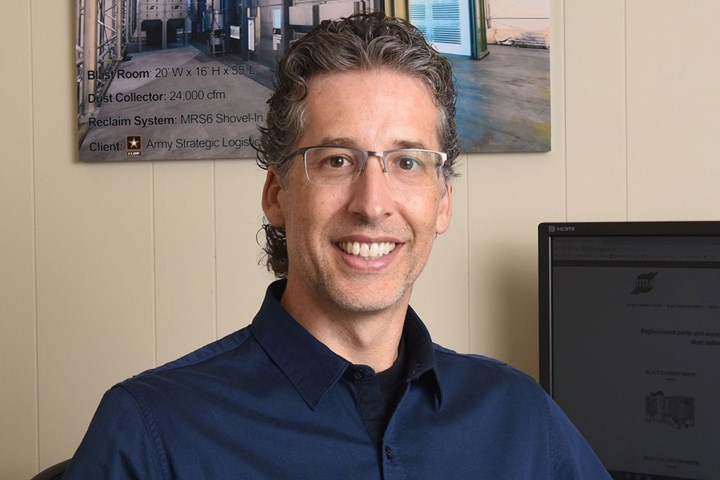
Brandon Acker, president, Titan Abrasives
Photo Credit: Titan Abrasives
In this episode of On the Line, the official podcast of Products Finishing we delve into blasting methods for preparation of surfaces prior to finishing.
Brandon Acker is president of Titan Abrasive Systems, a manufacturer of media blasting equipment and custom-engineered blast rooms that has been a provider of American-made blasting solutions since 1953. In this interview, Acker offers an overview of Titan’s offerings, insights for blasting best practices, common pitfalls and more.
An excerpt from Episode 19
So as we look at the basic process of blasting, I'm wondering if you could point out any common mistakes or misconceptions that you've seen people make as they do go through their blasting processes.
A big misconception of blasting that we find we're mainly we’re more industrial. So we deal with most things inside rather than outdoor. So inside with our blast rooms people are constantly looking for the problem of my blast room is going to be a mess, you know, I don’t want it in my shop because it’s going to be dirty, it’s going to make a huge mess.
In my shop that that is a misconception blast rooms are they are messy inside of them. It’s all about housekeeping. If you have a dust collection system, you put the room under negative pressure, it’s going to maintain that keep that dust and debris inside. As long as you’re not opening the doors while you’re blasting or too early, not allowing that collector to clear the room. Or you’re tracking debris in and out of the room is where your mess comes from. But it’s not going to fill your shop with dust. So that’s a pretty big misconception.
Another thing to pay attention to is maintenance. Maintenance on blasting equipment is pretty intense. It is what it is, it’s the nature of the beast, when you’re blasting have abrasive flowing in, you’re thinking what it does to a product, you know what it does to steel, how to remove that coating, it also does the same thing to the equipment, unfortunately. So there are parts on the equipment that do where it’s just kind of the nature of the beast. And you need to make sure you pay attention to those areas. And the maintenance all the manuals focus on certain valves, things that we designed the equipment to be maintained like that to have, you know areas that consumables that can be replaced easily. But you want to make sure you pay attention to those and keep that maintenance up where you’re going to have issues and keep your and keep the air dry. Now the big thing is, moisture is not your friend, when you blast is going to clump, it’s going to clog the media, you want to make sure you have really clean dry air. That’s gonna give you the best results.
Could you maybe speak to some quality issues that can arise if blasting is done incorrectly, maybe some of the kinds of defects you might see if it's incorrectly done.
Yeah, one of the big issues would be that profile, whether you're using the wrong media, too much pressure is creating too much profile, too little profile, you have too much profile is going to be really deep, and it’s going to take a lot of coating, you know to cover that profile is sealed and you’re not going to be happy or those jagged peaks are going to poke through the profile. So which is not what you want through the coating, or you’re going to have the opposite too little profile, so your coating is not going to adhere properly. So that’s a big thing. The other thing is that like I said that media using the wrong media steel grip on aluminum oxide, that that’s going to be one stainless, you don’t want the wrong media in there and bedding in stainless and failure coding failure, want to make sure you create those proper profiles. Nobody wants a coding failure. And that's probably the biggest, the biggest issue with blasting is not having that proper profile and having coating failure.
Related Content
Calculating Applied Media Force During Vibratory Finishing
What appear to be identically set-up vibratory bowls will finish identical loads of parts in varying time cycles. This paper offers a new technique to better predict what the operator will produce, by measuring the force applied to the parts. It is the efficiency of that force which controls the efficiency and speed of the refinement cycle.
Read MoreGlass Bead Blasting as Plating Pretreatment
What are the best practices for using blasting in preparation for plating? Angelo Magrone of Bales Metal Surface Solutions discusses the ins and outs of glass bead blasting.
Read MoreMiles Chemical Anaheim Doubles Capacity with Second Building
Miles Chemical Anaheim is doubling its capacity with the purchase of a second facility adjacent to its existing one.
Read MoreModernizing Wastewater Treatment and Recovery
Source: Kontek Kontek’s “spigot to drain” Source Water and Wastewater Solutions offer integrated technologies to modernize your water & wastewater treatment and recovery.
Read MoreRead Next
Episode 18: Richard Lynch, MacDermid Enthone
Richard Lynch, vice president of MacDermid Enthone Industrial Solutions discusses the company’s 100 year anniversary and its plans for the future.
Read MoreEpisode 16: Passion for the Industry (An Interview with Jim Jones, DIFCO)
Jim Jones, consultant and former vice president of DIFCO, discusses his experience in the surface finishing industry.
Read MoreEpisode 17: 2022 Finishing Hall of Fame Inductee Tony Revier
Tony Revier of Uyemura International discusses his experiences in the industry, as well as his insights into what the future might hold for surface finishing.
Read More