CO2-Based Spray Cleaning of Automotive Parts
Spray technology offers unique particle and organic residue removal benefits.
Carbon-dioxide-based spray technologies have been effectively used to meet a wide range of demanding precision cleaning and surface preparation applications because of their unique and adaptable particle and organic residue removal capabilities in a non-condensing spray.
This article will summarize the technology, explore how it has been applied to the cleaning of automotive plastic parts, summarize O&M cost factors and present its advantages over traditional cleaning technologies.
The non-condensing solid CO2 particles generated by the integrated spray are used to remove particulate matter and organic material from critical surfaces. Liquid CO2 is injected into a capillary condenser where it is transformed into solid particles of variable size and density. The particles are then mixed with a heated and pressure-regulated inert propellant gas to form a homogenous, non-condensing mixture with both controllable spray composition and energy.
The resulting spray can be adapted to deliver particle impact pressures as high as 10,000 psi without damaging plastic part surfaces. Because the primary cleaning agent is solid CO2, which sublimes upon contact with the surface, there are no cleaning agent residues to manage. When combined with an integrated solvent injection, the spray can be used with atmospheric plasma and ionized air de-stat systems for additional surface treatment capability.
Because the spray cleans without condensation, no special component heating or cleaning zone segregation are necessary. This makes the technology easily adaptable to the sort of open-celled cleaning applications used in the automotive painting industry.
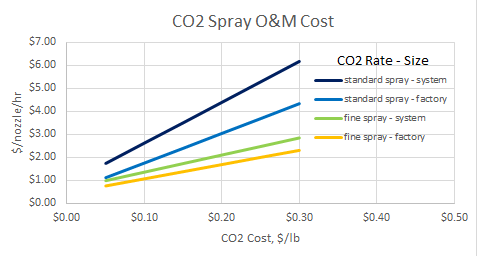
Figure 1: O&M cost estimates for CO2 spray cleaning as a function of spray type and CO2 cost.
Surface Preparation
So far, CO2 spray cleaning systems have been used to clean automotive acrylonitrile-butadiene-styrene (ABS) and polycarbonate (PC) parts prior to painting as a replacement for aqueous washing/drying and air jet cleaning. Some of the contaminants removed include manufacturing residues, dust, finger prints, mold release agents, water marks and other light oils, all of which can affect painting quality.
An integrated CO2 spray cleaning system was recently introduced to the paint line of a North American automotive component manufacturing plant. The plant uses a dual robot system in the cleaning room just upstream of the entrance to the paint booth. The system consists of a CO2 spray generator and a series of custom-designed nozzles and nozzle assembly. The application requires various three-dimensional ABS parts to be cleaned on both sides, accommodating existing fixtures on 40 × 60-inch racks and taking no longer that 45 seconds per rack.
Other cleaning requirements include:
--Clean and dry part surface
--No release agent or other remains after cleaning
--No negative impact to the part’s visual appearance or functionality after painting

A close-up of the one of the nozzle assemblies.
Among the contaminants of concern are hand sweat, dirt and dust, mold release agents, and tool oils.
To meet these requirements, the cleaning system includes two 4-nozzle CO2 spray modules with four nozzles each and two 6-axis robots designed to actuate the nozzle assembly for cleaning both sides of the parts using the identical part mounting racks and fixtures used in previous operations. Custom cleaning programs were developed to accommodate the CO-2 cleaning technology. A low-pressure CO2 supply and a pneumatic gas booster supply fluid to the spray modules.
Based on test results (customer confidential), the cleaning system has thus far been effective in removing the target contaminants and has eliminated the need to hand wipe plastic parts prior to painting.
Operation and Maintenance Costs
To determine the operational costs necessary to operate a CO2 spray generator system, it is necessary to consider the cost of CO2, the pressure of CO2 delivered to the unit, the energy necessary for spray system operation and the energy necessary to boost CO2 pressure.
The cost of CO2 is an obvious cost variable and depends on its quality and the pressure supplied. High-pressure (greater than 700 psig) bottles of liquid CO2 are suitable for small applications. For larger systems, gas-phase CO2 can be a cost-effective alternative. For many applications, the most cost-effective option is low-pressure (200 to 350-psig) CO2. Typical costs for low-pressure CO2 can range from 5 to 30 cents per pound, depending on supply. Prices for high-pressure CO2 supplies can range between $5 - $60 per pound.
Production-level cleaning applications typically utilize a low-pressure CO2 supply source. As such, a CO2 gas booster must be supplied as part of the cleaning system package and accounted for in the operational costs. These booster systems are typically either pneumatically or electrically driven. For pneumatically driven boosters, the cost of drive air becomes an important variable, while for electric boosters the cost of electricity is the dominant O&M cost. Since these systems are mechanical, periodic service costs should also be considered.
The cleaning module O&M costs include CO2 utilized, CDA (Clean, Dry Air), electric power and unit maintenance.
Figure 1 illustrates a cost model developed to estimate the O&M costs for a production-level CO2 cleaning system. These cost estimates are based on typical values of many parameters, including electricity costs, CO2 utilization, CO2 booster characteristics, maintenance costs and labor rates. These costs were developed using a range of CO2 supply costs, and were further subdivided based on the type of nozzle used and the nominal CO2 usage rates (fine spray and standard spray). In addition, two different types of CO2 supply systems are presented: “system” describes a single installation, and “factory” describes a larger CO2 infrastructure. The cost results are presented based on the cost of operation on a per-operational hour–per-nozzle basis, assuming 4,000 operational hours per year and electricity use of 20 cents per kW per hour. These estimates do not include the cost of equipment capital or installation.
The cost of CO2 supply dominates O&M costs for such systems, accounting for 35-58 percent for a single installation and 54-83 percent for a factory installation. Examination of Figure 1 shows that O&M costs can range from $1 to $2.85 per hour per nozzle for a single system and from 75 cents to $2.30 for a factory-level system.

A CO2 spray cleaning setup integrated into a North American plant’s painting operation.
For the standard spray system (the unit expected for most automotive painting operations), the factory-level costs range from $1.10 to $4.34, while single-system costs range from $1.74 to $6.20 per hour per nozzle. If we then assume a standard CO2 price of 10 cents per pound, which is typical in many North American manufacturing areas, we can expect the O&M costs to be about $2.50 per hour per nozzle for a single installation and about $1 per hour per nozzle for a factory system. Assuming that a typical paint line uses two cleaning modules of four nozzles each, the O&M costs for operation of this system for the cleaning modules are expected to be $20 per hour for a single installation and $8 per hour for a factory installation. These values include the costs of electricity, compressed air, CO2, spare parts and annual maintenance. Missing from this analysis is the cost of electricity for robots and fans used in the cleaning cell.
Advantages over Traditional Systems
Beside the technical capabilities of the CO2 spray in preparing automotive surfaces for painting, there are substantial cost and operational benefits. Typical paint line cleaning systems consist of multi-stage conveyors of spray washers—typically three and five stages followed by a water rinse. This is followed by a conveyor tunnel drying system laid out in a serpentine manner. In many instances, these cleaning lines demand hand wiping of parts with a solvent-soaked rag as a final cleaning prior to painting. Some wash lines are 400 to 500 feet long, and drying time can take over 30 minutes.
Operational costs to run these lines include:
--Electricity to run blowers for drying and power washers
--Heat for drying ovens (in some cases requiring up to 2 million BTU per hour)
--Inlet and outlet water treatment costs
--Consumables (detergents, filters, etc.)
Operational costs for these wash/dry lines can range from $50-$75 per hour. In addition, these systems consume large amounts of factory floor space.
A typical CO2 spray system, similar to the unit described above consists of two cleaning modules, a pneumatic booster, custom nozzles and two paint gun robots. The CO2 spray cleaning programming is a modification of that used for spray paint application. This system can be installed with a conveyor in a paint prep room. Furthermore, because the spray system’s cleaning function occurs at a single location in less than one minute, it is more responsive to process variations that may occur in the production than a cleaning system that has cleaning time of 30 to 45 minutes.
Based on comparisons with traditional aqueous-based cleaning systems, the CO2 spray cleaning system meets cleaning specifications with substantial cost savings. Capital costs of a complete CO2-based cleaning system will be substantially less than those of a traditional cleaning system. In addition, it is estimated that CO2 spray O&M costs are only 10 to 20 percent of those for a conventional spray wash system and take a fraction of the factory floor space—as little as five percent of the typical system.
Carbon-dioxide-based atmospheric spray systems have been shown to be effective for a wide number of applications in a variety of industries. This technology has been utilized to cost-effectively clean automotive plastic parts prior to paint application at the factory level with no cleaning waste byproduct. This cleaning technology option should be considered for applications where low costs, efficient use of factory floor space and environmental quality are valued.
Dr. Sorbo is vice president of R&D for Cool Clean Technologies and has been involved in the application and design of CO2 spray systems internationally. The author gratefully acknowledges the support of Thierica Equipment Corp. for assistance with this article. For information on Cool Clean Technologies, please visit coolclean.com.
Related Content
Tin and Tin Zinc Overview and Growth
Brett Larick of Columbia Chemical discusses the increasing demand for conductive finishes driven by the increasing electrification of vehicles.
Read MoreIndonesian Plater Finds Fast Success in Auto Market
This father/son team, inspired by inventor Michael Faraday, focuses on anti-corrosion methods and automated processes to help their Indonesian plating business flourish.
Read MoreEpoxy Rebar Company Reinforcing Roads of the Future
Providing epoxy-coated rebar with the ultimate corrosion resistance is Simcote’s focus for the infrastructure industry it serves.
Read MorePrecise Paint Flow Reduces Material and Labor Costs
Finding a more accurate paint proportioner for its application enabled this auto parts manufacturer to save significant costs and labor while increasing capacity.
Read MoreRead Next
Masking Solutions for Medical Applications
According to Custom Fabricating and Supplies, a cleanroom is ideal for converting, die cutting, laminating, slitting, packaging and assembly of medical-grade products.
Read MoreA ‘Clean’ Agenda Offers Unique Presentations in Chicago
The 2024 Parts Cleaning Conference, co-located with the International Manufacturing Technology Show, includes presentations by several speakers who are new to the conference and topics that have not been covered in past editions of this event.
Read MoreEducation Bringing Cleaning to Machining
Debuting new speakers and cleaning technology content during this half-day workshop co-located with IMTS 2024.
Read More