Indonesian Plater Finds Fast Success in Auto Market
This father/son team, inspired by inventor Michael Faraday, focuses on anti-corrosion methods and automated processes to help their Indonesian plating business flourish.
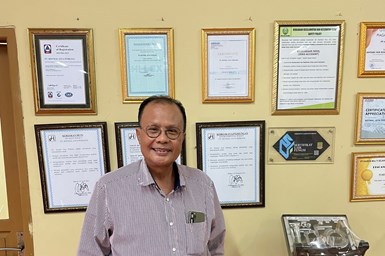
Hotman Malau, a first-generation plater, became an industry legend in Indonesia because of his specialized knowledge of the plating of metals and ability to grow his business so quickly.
Photo Credit: MacDermid Enthone
In 1831, British scientist Michael Faraday discovered electromagnetic induction, arguably the greatest scientific achievement in the modern history of surface treatment. Faraday is known to have inspired many people throughout the world, not only in chemistry but in other fields as well.
One hundred and fifty years later, an admirer of Faraday’s accomplishments, a young Indonesian man named Hotman Malau, began his career in the plating industry. After working for another plating company, Malau decided to start his own plating shop in his garage. He could not have dreamed then that in a short time, he would be leading a booming business with 700 employees. Although his company, PT Hotmal Jaya Perkasa (West Java, Indonesia), has faced trials, it has pulled through and is successful today. Malau, along with his son as his business partner, have built an entity that focuses on sustainability as a long-term strategy.
Surrendering his diploma
Malau had always been infatuated with everything related to electroplating. Therefore, he knew that engineering was a promising path to accomplishment in the plating industry. After completing high school, it took Malau eight years to graduate with a bachelor’s degree in engineering, finishing near the top of his class. He entered the workforce at the relatively mature age of 26 and joined a job shop that specialized in anti-corrosion plating.
In 1990, Malau’s first son was born while his career was only beginning. Malau named his son Faraday, after Michael Faraday, the great inventor. With no capital whatsoever and a 4-year-old son to support, Malau started PT Hotmal Jaya Perkasa in 1994 from the confines of his garage. Hotmal is derived from a combination of the first three letters of Malau’s first name and last name.
Because physical proof of a certified college diploma is required to find almost any job in Indonesia, he surrendered his graduation certificate to an investor to prove that he was 100% committed to his new venture and would not walk away to find a job elsewhere. After a few years, the investor began to see profits and returned Malau’s diploma to him.
Revving up to prosperity
Just as William Harley and Arthur Davidson started their motorcycle business from a garage, Malau first used his garage to offer plating services. Customers were introduced via word of mouth, and volume increased quickly. Malau outgrew the garage after only two years and moved to a location more befitting of a factory.
Through the 1990s and 2000s, PT Hotmal expanded and at one point, had 700 employees because of the thriving Indonesian auto industry’s need for anti-corrosion plating. Over time, the company automated processes, tripling
PT Hotmal plans to recycle all the polyethylene plastic used in the jerricans supplied by the chemical suppliers. While still in the experimental phase, the company currently grinds the plastic into flakes. The intention is to mold the plastic using on-site injection molding equipment in the near future.
production capacity. Now, however, the company requires only 350 employees at its two factories in Cibitung and Tangerang, Indonesia.
Malau, a first-generation plater, became an industry legend in his country because of his specialized knowledge of the plating of metals and ability to grow his business so quickly.
Hard times
The most challenging time for PT Hotmal was in 2011. An earthquake in Japan triggered a series of events that almost led to the collapse of the business.
Malau laments, “The tsunami, which occurred immediately after the earthquake, wreaked chaos on the automotive fastener industry because steel from Japan was no longer available in Indonesia.”
Faced with the prospect of shutting down, some of PT Hotmal’s customers scrambled to use locally available steel. The change in the material quality led to a recall at a fastener manufacturer, which almost bankrupted PT Hotmal.
Contributing to a circular economy
Last year (2023) was a turning point for the company as the young Faraday, now 32, helps his 66-year-old father navigate an unknown future with new challenges. As a company that focuses 90% of its business on zinc and zinc-nickel plating used in automotive applications, metals are near and dear to its heart.
Therefore, plastics have not been core to the family business. Nonetheless, the father/son duo is intentional about managing every segment of the organization. Therefore, they plan to recycle all the polyethylene plastic used in the jerricans supplied by the chemical suppliers. While still in the experimental phase, PT Hotmal currently grinds the plastic into flakes. The intention is to mold the plastic using on-site injection molding equipment in the near future. The company is currently in talks with partners regarding the end-use applications of such recycled plastic.
About the Author
Julian Bashore
Julian Bashore, based in Tokyo, Japan, is general manager of the MacDermid Enthone Industrial Solutions businesses in Indonesia, Japan and Thailand. He also manages Circuitry Solutions in Japan and has served on the board of the Japan Electronics Packaging and Circuits Association since 2015. Before joining the plating industry in 2013, his career was focused on coatings and other surface treatment technologies.
Related Content
Advantages to Pumped Eductor Agitation
Not all agitation methods are created equally. Pumped agitation with eductor nozzles can improve process tanks and quickly show a reduction in operating costs while keeping staff safe, following environmental legislation and preventing pollution.
Read MoreAn Overview of Electroless Nickel Plating
By definition, electroless plating is metal deposition by a controlled chemical reaction.
Read MoreSuccessful South African Plater Beating the Odds
Remaining focused on quality and reliability, Team Plating Works stays profitable in a volatile and challenging economy.
Read MoreHow to Maximize Nickel Plating Performance
The advantages of boric acid-free nickel plating include allowing manufacturers who utilize nickel plating to keep up the ever-changing regulatory policies and support sustainability efforts.
Read MoreRead Next
Faraday's Children (and Nickel): The 40th William Blum Lecture
This article is a republication of the 40th William Blum Lecture, presented at the 86th AESF Annual Convention in Detroit, Michigan on June 21, 1999. In this lecture, Dr. George DiBari describes the search for the ideal nickel anode material and the outlook for survival of nickel plating at the end of the 20th century.
Read MorePlating with Zinc-Nickel: Benefits and Challenges
Chad Murphy of Columbia Chemical speaks about the benefits of various types of zinc-nickel alloy, and provides tips for manufacturers about the zinc-nickel plating process.
Read MoreEducation Bringing Cleaning to Machining
Debuting new speakers and cleaning technology content during this half-day workshop co-located with IMTS 2024.
Read More