Mitigating Heat in the Building
Powder coating systems radiate heat and without good air turn over the heat can become unbearable. Powder coating expert Rodger Talbert offers ideas for cooling your facility.
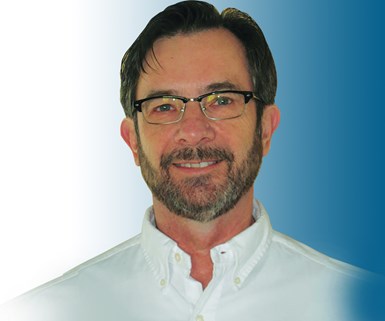
Rodger Talbert has more than 30 years of experience in the powder coating industry.
Q: We are located in Florida and we do not currently cool our shop. It has always been hot in the summer months and we tolerate it by using fans and working an early shift to avoid the worst heat of the day.
We installed a powder operation this winter and it generates a lot of heat from the washer and ovens. It is not too bad yet but on hotter days is already becoming a problem and the hot months are coming. We have talked to the company that supplied the powder system and they suggest that we consider air conditioning the entire plant. We are not anxious to take on the cost of cooling that much space and we were wondering if there is another way to help reduce the heat buildup by insulating the equipment or something. Any suggestions would be appreciated.
A: It is true that powder systems do radiate heat and without good air turn over the heat can become unbearable, even in cooler areas like where I live in Michigan. Air conditioning could work but that is a substantial investment and a big operating expense. You may want to look into evaporative cooling. It will cost more than cooling with outdoor air but it can drop the indoor temperature to a lower point.
I think a better alternative would be good ventilation using outdoor air to change the heated air inside the building. You need to turn over the building air to avoid the continuous gain of temperature during hot days. The building should be slightly pressurized to ensure that the heated air from the equipment is constantly pushed out.
Good ventilation has to have exhaust air from the building and supply air from Air Make-Up (AMU). Sizing of the ventilation fans depends on the size of the building, the size of the thermal equipment, and how well designed and insulated the ovens and washer were built. Generally, the air inside the building should be “turned over” somewhere between 0.20 air changes to 0.50 air changes per 1,000 cubic feet depending on the building size, shape and construction. Air changes should usually be at least 1.5 per hour to make sure the heat is evacuated fast enough and air changes of 5 per hour may be necessary if the outdoor temperature is very high and the equipment is generating substantial heat.
The ventilation fans should be strategically placed to capture as much radiant heat from the equipment as possible. The exhaust volume should be added to the exhaust volume of the system equipment to get the total AMU needed. The total cubic feet per minute (CFM) of AMU needed will be based on the equipment exhaust, the ventilation volume, and the slight addition to maintain pressure inside the building when the system is running. The AMU can be designed with or without heaters so you can cool the air and have the ability to heat also if needed.
Using good ventilation will drop the indoor temperature to around the same as the outdoor temperature. Evaporative or mechanical cooling can drop the temperature below outdoor levels but it will cost more to purchase and operate.
Related Content
How to Address Declining Powder Coating Coverage Over Time
Fine particles from reclaim could be to blame for powder coating problems that emerge over time. Avoid problems by keeping hooks clean, maintaining guns and using reclaim powder quickly to avoid accumulation of fines.
Read MoreTroubleshooting Alkaline Zinc
One of the most common problems that can arise when plating with alkaline zinc is an imbalance of brightener in the solution. In this helpful Ask the Expert article, Chad Murphy of Columbia Chemical discusses how different zinc metal concentrations and brightener concentrations can impact efficiency.
Read More10 Anodizing Best Practices
Following this list of guidelines can help to increase the performance, cost effectiveness and quality for your anodizing operation.
Read MoreMasking Solutions for Medical Applications
According to Custom Fabricating and Supplies, a cleanroom is ideal for converting, die cutting, laminating, slitting, packaging and assembly of medical-grade products.
Read MoreRead Next
A ‘Clean’ Agenda Offers Unique Presentations in Chicago
The 2024 Parts Cleaning Conference, co-located with the International Manufacturing Technology Show, includes presentations by several speakers who are new to the conference and topics that have not been covered in past editions of this event.
Read MoreEducation Bringing Cleaning to Machining
Debuting new speakers and cleaning technology content during this half-day workshop co-located with IMTS 2024.
Read MoreDelivering Increased Benefits to Greenhouse Films
Baystar's Borstar technology is helping customers deliver better, more reliable production methods to greenhouse agriculture.
Read More