Non-chromated Conversion Coating for Magnesium Alloys and Zinc-Nickel Plated Steel
A novel hexavalent chromate-free conversion coating was developed to improve anti-corrosion and adhesive-bonding characteristics of the magnesium alloys and zinc-nickel (Zn-Ni) plated steel substrates. The corrosion behavior of the coated and uncoated alloys was investigated by neutral salt fog (NSF) and electrochemical corrosion tests. Surface wettability of the pretreated substrates was investigated by static contact angle measurements. Wet-tape adhesion tests verified that there is strong adhesion between the primer and the chem film-treated substrates. The morphology and composition of the coated surfaces were investigated by optical microscopy (OM), scanning electron microscopy (SEM) and energy dispersive x-ray spectroscopy (EDX) methods. This trivalent chromium-based surface treatment is a potential hexavalent chromate conversion coating replacement for magnesium alloys and Zn-Ni plated steel.
Magnesium alloys and Zn-Ni plated steels have been used in a variety of aerospace and defense sectors. Both magnesium alloys and Zn-Ni platings require a chem film treatment for maximum corrosion protection and to improve the paint adhesion characteristics of the surface. Chromate conversion coatings have been used on magnesium alloys and Zn-Ni platings mainly for temporary corrosion protection and to improve the adhesive bonding characteristics of the surface.
In this work, an eco-friendly trivalent chromium (Cr+3)-based conversion coating technology is studied on magnesium alloys and Zn-Ni plated steel substrates. Neutral salt fog (NSF), potentiodynamic polarization, and open circuit potential (OCP) methods were used to evaluate the corrosion properties of the chem films. Wet-tape adhesion tests were performed on coated and uncoated magnesium and Zn-Ni plated 4130 steel substrates and rated in accordance with ASTM D3359A.5 Comparative performance analysis results for the uncoated, trivalent chromium- and hexavalent chromate-processed magnesium alloys and Zn-Ni plated steel is presented.
Experimental
Test methods
Corrosion resistance testing was done on test coupons for each pretreatment process using a neutral salt fog salt spray chamber maintained in accordance with ASTM B117.7 Potentiodynamic polarization and open circuit potential (OCP) measurements were performed by using a G300 Gamry Potentiostat. The experiments were carried out in an aerated 3.5% NaCl (pH 6.5-7.2) electrolyte.
Test samples were primed with non-chromated epoxy primer (MIL-PRF-23377J, Type I, Class N)8 and cured for seven days at room temperature prior to the wet-tape adhesion test. The wet-tape adhesion test was performed in accordance with Federal Test Method Standard 141 (FED-STD-141)9 and rated in accordance with ASTM D3359A.5 Sealed and plated Zn-Ni plated steel test coupons were exposed to salt spray for one week prior to the wet-tape adhesion test. The adhesion rating per ASTM D3359 - Method A is shown in Table 1.
Contact angle measurements were made by using a Rame-Hart model 250-F1 contact angle goniometer. The surface morphology of deposited films was observed using a Hitachi S-4700 scanning electron microscope (SEM/EDX). All coated panels were cured for 24 hr at ambient temperature prior to the measurement of anti-corrosion and paint adhesion properties.
Table 1 - Wet tape adhesion rating per ASTM D3359 - Method A.5
ASTM D3359 - Method A
Rating description of coating after tape removal
4 Trace peeling or removal along scribes.
3 Jagged removal along scribes up to 1/16 in. (1.6 mm) on either side.
2 Jagged removal along most of the scribes up to 1/8 in. (3.2 mm) on either side.
1 Removal from most of the area between the scribes under the tape.
0 Removal beyond the area of the scribes.
Scanning electron microscopy (SEM) images along with the energy dispersive x-ray spectroscopy (EDX) studies revealed that the surface of the magnesium alloys was homogeneously covered with the trivalent chromium-based deposits with relatively less mud-cracking. The details will be presented elsewhere.
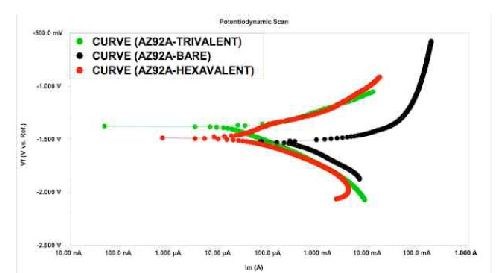
Figure 2 - Optical microscopy images for uncoated (L) and trivalent chromium conversion coated (R) AZ31B-H24 magnesium alloy surface after 26 hr of exposure to 5% NaCl solution (pH 6.5-7.2) at room temperature.
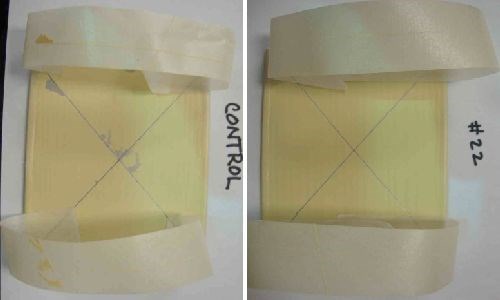
Figure 3 - Wet tape test results for non-chromated epoxy primed and scribed AZ31B-H24 magnesium alloys; bare (L), trivalent chromium-coated (R) magnesium samples. Scale from the surface was removed chemically. Trivalent chromium-based chem film on the magnesium alloy surface provided excellent tape adhesion characteristics with a rating of 5A in accordance with ASTM D3359 - Method A.
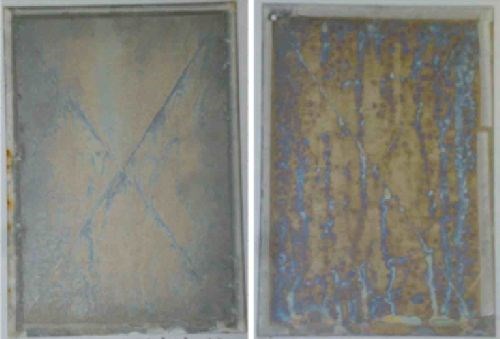
Figure 4 - Zn-Ni plated 4130 steel test panels sealed with the novel trivalent chromium (L) and hexavalent chromate (R) after 528 hr neutral salt fog test per ASTM B117.
Open circuit potential (OCP) measurements in a naturally-aerated 3.5% NaCl (pH 6.5-7.2) corrosive medium revealed that sealing the Zn-Ni plated steel with the novel trivalent chromium-based coating solution resulted in a positive potential shift from -875 mV (for bare unsealed Zn-Ni-plated steel) to -840 mV (for trivalent chromium-sealed Zn-Ni plated steel) as shown in Fig. 5.
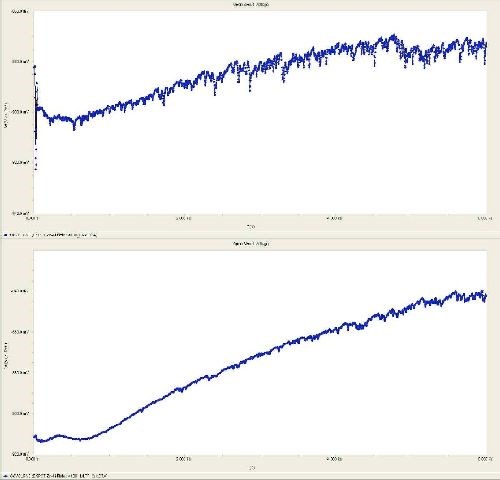
Figure 5 - Open circuit potential (OCP) diagrams for bare Zn-Ni plated 4130 steel (top) and trivalent chromium-sealed Zn-Ni plated 4130 steel (bottom). Sealing with the novel environmentally green trivalent chromium coating solution caused a positive potential shift from -875 mV to -840 mV.
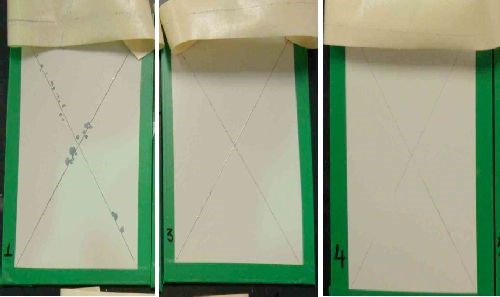
Figure 6 - Wet-tape tests on non-chromated epoxy primed Zn-Ni plated steel after 168 hr of salt spray exposure: Bare Zn-Ni plated steel (left), hexavalent chromated (center) and trivalent chromium-sealed (right).
2. F.W. Eppensteiner & M.R. Jenkins, Metal Finishing Guidebook, 109, 417 (2011).
3. H. Bhatt, A. Manavbasi & D. Rosenquist, Metal Finishing, 107 (6), 39 (2009).
4. EPA Federal Register, National Emission Standards for Hazardous Air Pollutants for Source Categories: Aerospace Manufacturing and Rework Facilities, 60 (170), 45947 (1995); epa.gov/ttn/atw/aerosp/fr9195.pdf.
5. ASTM Standard D3359, 2002, “Standard Test Methods for Measuring Adhesion by Tape Test,” ASTM International, West Conshohocken, PA, DOI: 10.1520/D3359-02.
6. AMS-M-3171-C, “Magnesium Alloy, Processes for Pretreatment and Prevention of Corrosion on,” Society of Automotive Engineers, Warrendale, PA: Standardized Document Order Desk).
7. ASTM B117, 2002, “Standard Practice for Operating Salt Spray (Fog) Apparatus,” ASTM International, West Conshohocken, PA, DOI: 10.1520/B0117-02.
8. MIL-PRF-23377J, “Performance Specification - Primer Coatings: Epoxy, High Solids,” (2006).
9. FED-STD-141, “Federal Test Method Standard Paint, Varnish, Lacquer, and Related Materials: Methods of Inspection, Sampling and Testing,” Philadelphia, PA: Standardization Document Order Desk.
Related Content
Solar-Powered Photonic Cooling Enables Energy-Saving Coating
Passive cooling technology can reduce interior temperatures 5-13°C, offering weight, cost and CO2 benefits for cars, construction, aircraft and more.
Read MorePortfolio of Energy-Curable Coatings Launched
PPG's DuraNEXT portfolio includes EB and UV curable coatings, offering rapid, energy-efficient solutions for metal coil coaters.
Read MoreRevolutionizing Battery Production for Electromobility
Fully automated process combines ultrafine cleaning and protective UV coating for battery cells, replacing the need for traditional film wrapping.
Read MoreEnergy Efficient SprayWand Pretreatment System
P-450 Energy Efficient SprayWand Pretreatment System Source: PEM PEM Inc., a leader in providing innovative batch and automated finishing equipment to OEMs, fabricators and job shops, will display its SprayWand, FinFlow and SprayLean brands.
Read MoreRead Next
Education Bringing Cleaning to Machining
Debuting new speakers and cleaning technology content during this half-day workshop co-located with IMTS 2024.
Read MoreEpisode 45: An Interview with Chandler Mancuso, MacDermid Envio Solutions
Chandler Mancuso, technical director with MacDermid Envio discusses updating your wastewater treatment system and implementing materials recycling solutions to increase efficiencies, control costs and reduce environmental impact.
Read MoreA ‘Clean’ Agenda Offers Unique Presentations in Chicago
The 2024 Parts Cleaning Conference, co-located with the International Manufacturing Technology Show, includes presentations by several speakers who are new to the conference and topics that have not been covered in past editions of this event.
Read More