Powder Coating Clinic: Making Powder Lines More Profitable
Q. We run a job shop powder coating operation with a conveyor system that runs at around 4 to 6 fpm, depending on what product is hung. We are putting through a lot of work, but our profits are not great. Can you suggest how to improve the efficiency, or cut our cost for a better profit margin? We cannot speed up the line because we do not have enough time in the cure oven to go faster. Our powder material cost seems to be higher than what we expect based on our quotes. What are we missing?
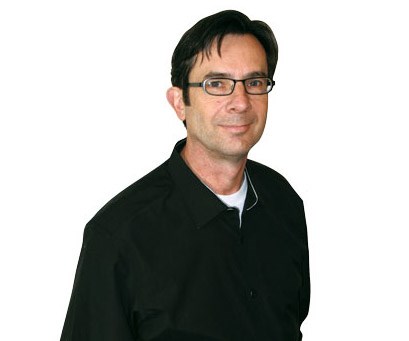
Q. We run a job shop powder coating operation with a conveyor system that runs at around 4 to 6 fpm, depending on what product is hung. We are putting through a lot of work, but our profits are not great. Can you suggest how to improve the efficiency, or cut our cost for a better profit margin? We cannot speed up the line because we do not have enough time in the cure oven to go faster. Our powder material cost seems to be higher than what we expect based on our quotes. What are we missing?
A. Start by reviewing your quoting practices. You need to break down your racking scheme and make sure you understand the actual production rate. Gather all your costs (labor, material, fixed business cost, line burden, scrap and rework, etc.) and divide it out by the production rate to get an accurate per-piece price based on the production rate. Then you will know your real cost per part and be in a good position to add the profit margin you need.
Another issue that I always point out is racking. The conveyor speed is one aspect of throughput but the more important issue is “how full is the line?” Pay attention to spacing in the vertical and horizontal. Be aware of improved positions or density. As long as the coaters can keep up with the amount of surface going through the booth, it is a good idea to rack parts densely. You may want to invest in special racking for some parts so that they are hung at the optimum density. Simple hooks are useful but sometimes they do not take proper advantage of the available space on the line.
Operator technique and film build control are also key issues. Be sure your operators have the proper training and understanding of what to coat, how to use the gun and how much powder is needed to achieve the desired performance. If they are not efficient or you have too many rejects, the cost of coating is artificially high. Check film build regularly.
Color change is also a factor in some lines. Limit color change frequency and work on short color-change time by training your people and using the best equipment available. Plan production to minimize downtime and lost powder. Maintain your system by scheduling cleaning and repair and keeping things in good working condition. Damaged or worn system components reduce efficiency and raise cost. Keep spare parts inventory and make sure the guns are always in good working order.
Check your earth ground to make sure that your parts are always grounded during coating. Poor grounding will increase rejects (hook scars, light coating, orange peel) and decrease application efficiency. Use good powder products. Some coaters shop for lower cost powder by the pound. Focus on applied cost, and that may mean using a material that costs more per pound but covers more surface because of better ingredients. Not all powders are created equal.
Make sure the people that run the line are trained and motivated, keep the system in good condition and maximize output. Use the line for optimum throughput, and you should be making money.
Originally published in the December 2016 issue.
Related Content
Film Thickness Control
Have a powder coating job that requires precise film thickness control? Products Finishing columnist Rodger Talbert offers advice controlling the variables that can impact your success.
Read MoreCFS Unveils New Hook Locks Parts Racking Solution
New product from Custom Fabricating & Supplies (CFS) prevents part loss during coating processes.
Read MoreMaximize Your Racking Efficiency and Quality
Best practices for racking parts in surface finishing operations.
Read MoreFABTECH 2024 Heads to Orlando
CCAI’s FINISHING Pavilion and Conference continues to grow at FABTECH, offering insights and innovations covering all aspects of industrial surface finishing.
Read MoreRead Next
Episode 45: An Interview with Chandler Mancuso, MacDermid Envio Solutions
Chandler Mancuso, technical director with MacDermid Envio discusses updating your wastewater treatment system and implementing materials recycling solutions to increase efficiencies, control costs and reduce environmental impact.
Read MoreA ‘Clean’ Agenda Offers Unique Presentations in Chicago
The 2024 Parts Cleaning Conference, co-located with the International Manufacturing Technology Show, includes presentations by several speakers who are new to the conference and topics that have not been covered in past editions of this event.
Read MoreDelivering Increased Benefits to Greenhouse Films
Baystar's Borstar technology is helping customers deliver better, more reliable production methods to greenhouse agriculture.
Read More