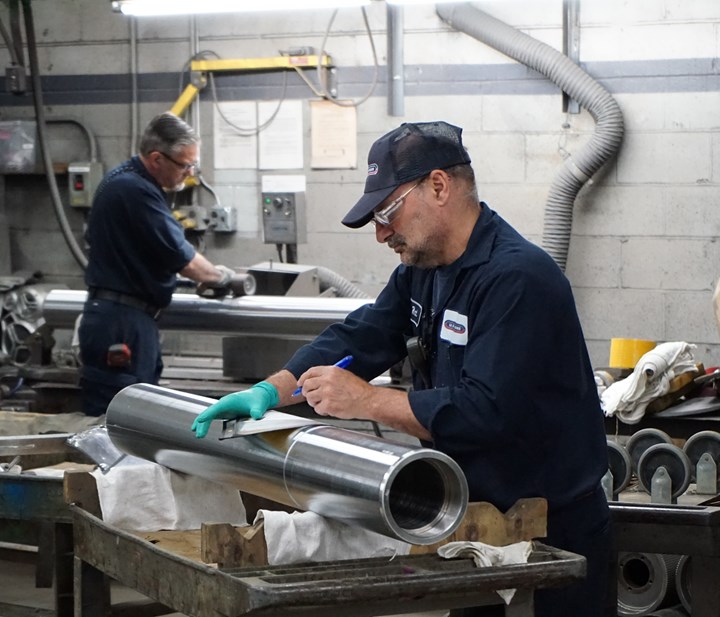
U.S. Chrome prides itself on developing customized solutions for its customers.
Photo Credit: All photos courtesy of U.S. Chrome
U.S. Chrome has served the plating industry since the 1940s. The company boasts a state-of-the-art research and development laboratory where it works to develop customized coating solutions for its customers and explores environmentally-friendly alternatives to traditional chromium plating technologies. The company’s Batavia, N.Y., facility has qualified as a Products Finishing Top Shop in our annual benchmarking survey for three years running. PF recently sat down with third generation owner Mike Reath, New York facility general manager Mike Klotzbach, application engineer Scott Broussard and marketing manager Chris Berlinski to hear more about what continues to make U.S. Chrome a leader in the industry.
PF: U.S. Chrome got its start in the 1940s. Can you give a brief bit of background on the company’s history and its current finishing capabilities?
CB: The company was founded by Roger Reath and another business partner in 1940. It was originally named Superior Plating and spawned additional satellite plants that went by the name Tibon Plating. Years later, the company was restructured with many of these plants being renamed U.S. Chrome Corporation.
U.S. Chrome Corporation’s five facilities combine to offer a variety of surface finishes, including hard chrome, thin dense chrome, electroless nickel, electrolytic nickel, NiCom (nickel silicon carbide), cerakote, spray decorative chrome, hydro dip, and other alternatives.
MR: We are able to deposit chrome on a number of different substrates that some other platers cannot — titanium for example.
PF: What industries do you serve?
CB: Some of the industries we currently serve are aerospace, agriculture, alternative energy, defense, firearms, heavy industry, hydraulics, medical, and oil and gas.
MK: Specific to the New York facility, agricultural and aerospace are very big up here and the reason why we got our Nadcap Chemical Processing and Aerospace Quality Systems certification. We also do a lot with the hydraulics industry — not only new but also the refurbishment of hydraulic rods including the strip, repair, plate and polish. It’s kind of been our bread and butter for a good long time.
PF: You have several locations – what advantages does that give you for serving various markets?
CB: Having several locations provides us with a number of advantages, but what is really impressive is how we’re able to use the diversity of each location as one of them. Our general managers and application engineers work closely together to share their varied experiences and expertise. From discussions on different industries and plating topics to the development of unique solutions, our teams thrive on helping each other provide the best quality to our customers and strengthening the knowledge base of each employee.
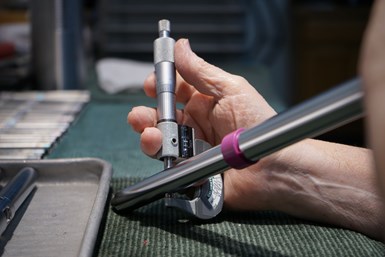
U.S. Chrome strives to provide creative solutions for challenging plating applications.
PF: One of the things U.S. Chrome seems to highlight is “tailored plating solutions” – can you talk a bit about how you work with your partners to offer solutions specific to their application?
MR: Our tooling is really one of the things that sets us apart. We provide custom fixturing and creative solutions for getting to the areas where others can’t.
CB: We’ve found that when we receive challenging applications, forming a good working relationship with that partner, where communication flows freely, is paramount to both our success. It allows us to receive thorough details on the complexities and requirements of the job in a timely manner.
This information helps us build a solution around their application that is purposefully designed to achieve the exact job requirements that are needed. Not only does that allow us to provide a quality surface finish that most other companies cannot, but also improve customer satisfaction through reduced lead times and better communication.
There will always be new, inventive ways to solve difficult-to-plate applications, our commitment is to advance our abilities and provide the best, most efficient solution for that specific application.
Recently, U.S. Chrome successfully engineered a plating process for a component that NASA/JPL had previously been struggling with. During a visit, we allowed them to evaluate our fixturing to demonstrate how we go about plating these challenging applications. Their feedback to us was that we were at a level above the other platers they had worked with and that we were the type of plater they need to be working with going forward.
MK: We specialize in the difficult applications. It’s become normal to receive RFQs from other platers if they’re not able to accomplish what their customer is looking for.
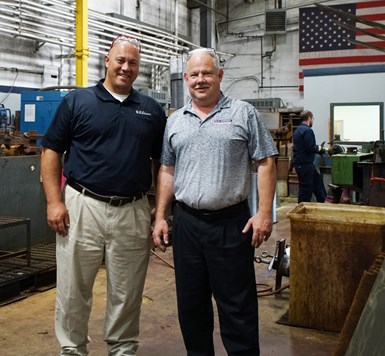
Scott Broussard (left), Application Engineer, with Mike Klotzbach (Right), General Manager, of U.S. Chrome Corporation of New York.
PF: What makes U.S. Chrome a Top Shop?
MK: We’re very anxious every year to get the [survey] results. We view it as our report card, as we like to see how we stack up against peers in the industry. We appreciate the format because it tells us where we’re strong, where there are opportunities to improve. It gives us a benchmark.
CB: U.S. Chrome simply cares about our partners’ problems, and we do everything that we can to make their business better. As a customer-oriented company, we strive for complete customer satisfaction and our goal is to make our partners feel as though we are an extension of their company.
Perhaps the aspect that makes us a top shop is our ability to reflect on feedback and surveys, such as the Products Finishing Top Shops survey, discuss our findings, and enact positive changes that will better our customers and our own success. We grow in these ways, and we are always improving by taking on the hardest applications that come as part of the many essential business supply chains we serve.
Related Content
Defining a Top Shop: Quality, Quickness, Communication, Community
Luke Engineering & Anodizing Co. takes an active role in its community and the industry while also focusing heavily on the quality of its work and employee treatment.
Read MoreAttentive Employees Support Large Customer Base
As a Products Finishing Top Shop, this company’s success with offering a variety of finishing services would not be possible without its employee dedication and the pride that’s been instilled in them to produce quality products for its long list of customers.
Read MoreHow to Build a Powder Coating Brand
Maui Powder Works, a 2022 Products Finishing Top Shop, shares the story behind how it grew from an island job shop to a recognized voice in the finishing community.
Read MoreHighlights from SUR/FIN 2023
Products Finishing offers a recap of some of the topics that were top of mind at the SUR/FIN 2023 finishing industry trade show.
Read MoreRead Next
A ‘Clean’ Agenda Offers Unique Presentations in Chicago
The 2024 Parts Cleaning Conference, co-located with the International Manufacturing Technology Show, includes presentations by several speakers who are new to the conference and topics that have not been covered in past editions of this event.
Read MoreEducation Bringing Cleaning to Machining
Debuting new speakers and cleaning technology content during this half-day workshop co-located with IMTS 2024.
Read MoreDelivering Increased Benefits to Greenhouse Films
Baystar's Borstar technology is helping customers deliver better, more reliable production methods to greenhouse agriculture.
Read More