Keyland Polymer, PolySpectra Powder Coat 3D-Printed Parts
Keyland’s color-matching capabilities, combined with PolySpectra's COR family of materials, now enable consumer and industrial brands to adopt a new approach to digital manufacturing.
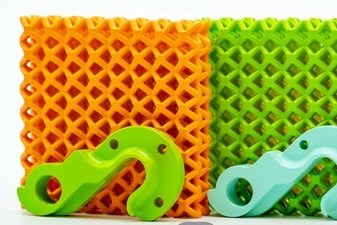
Keyland Polymer (Cleveland, Ohio) and PolySpectra (Berkeley, California) have announced a strategic partnership to provide UVMax powder coatings to Cyclic Olefin Resin (COR) Alpha 3D-printed parts. This collaboration is said to unlock a new modular approach to additive manufacturing (AM), enabling the direct digital fabrication of end-use polymer components for a wide variety of applications.
The surface color and texture of the UVMax coating can reportedly be tailored to make COR Alpha 3D-printed parts indistinguishable from traditionally-manufactured polymer products. The color-matching capabilities of Keyland, combined with PolySpectra's COR family of materials, now enables consumer and industrial brands to adopt a new approach to digital manufacturing.
PolySpectra's family of engineering-grade photopolymers are said to unlock a diverse array of previously impossible AM applications. For over five years, the PolySpectra team has been collaborating with end-users of 3D printing to refine COR Alpha for applications that require thermomechanical performance and durability.
Keyland's UVMax is said to provide an excellent finish for plastic applications in transportation, light-weighting, building materials, consumer and industrial products. Keyland can develop a wide range of powders to match supplied color standards. In addition, UV powder is an environmentally friendly coating, containing no solvents, volatile organic compounds (VOCs) or hazardous air pollutants (HAPs); it is safe to use and can be reclaimed and recycled.
Both COR Alpha and UVMax were designed for durability. The high working temperature, toughness and extreme chemical resistance of COR Alpha is enhanced by the hardness, abrasion resistance and excellent adhesion of the UVMax coating.
Related Content
-
NASF/AESF Foundation Research Project #123: Electrochemical Manufacturing for Energy Applications - 9th Quarterly Report
This NASF-AESF Foundation research project report covers the ninth quarter of project work (January-March 2024) at the University of Texas at Dallas. In this period, we followed our work on 3D printing anode support for solid oxide fuel cells, SOFC (or cathode for solid oxide electrolyzers, SOEC). We focused on the mechanical properties of 3D printed yttria-stabilized zirconia (YSZ) using a four-point bending test. We then conducted a statistical analysis to characterize the flexural strength of porous 3D printed YSZ. The full paper on the ninth quarter work can be accessed and printed at short.pfonline.com/NASF24June2.
-
Plating Additively Manufactured Plastic Parts
Using electroplating to enhance the structural properties of 3D printed parts.
-
NASF Foundation Research Project #123: Electrochemical Manufacturing for Energy Applications - 10th Quarterly Report
The NASF-AESF Foundation Research Board selected a project on electrodeposition toward developing low-cost and scalable manufacturing processes for hydrogen fuel cells and electrolysis cells for clean transportation and distributed power applications. In this period, we followed our work on 3D printing anode support for solid oxide fuel cells, focusing on the thermal shock properties of 3D printed yttria-stabilized zirconia (YSZ).