PPG, Satys Partner for Aerospace Ecoat System in France
PPG is partnering with Satys, a French industrial group active in aircraft sealing, painting and surface treatment.
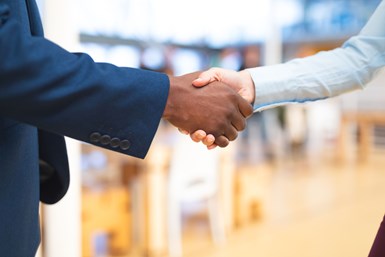
Photo Credit: Getty Images
PPG has partnered with Satys — a French industrial group active in aircraft sealing, painting and surface treatment — to provide electrocoating (ecoat) of OEM aircraft parts. As part of the agreement, Satys will install a PPG Aerocron ecoat primer system at its facility in Dugny, France.
“PPG is proud to partner with Satys to provide our innovative ecoat technology in close proximity to key aerospace OEMs,” says Sam Millikin, PPG global director, coatings and sealants, Aerospace. “Our customers in France will benefit from the PPG Aerocron system, which produces a more uniform finish on the aircraft parts, using less paint than traditional spray-applied methods.”
With the PPG Aerocron technology, metal aircraft parts are dipped into a bath of chrome-free ecoat primer and charged with electrical current to apply the coating, resulting in an even surface finish, a consistent coating thickness and no drips, runs or sags in the cured paint film. Ecoat is a sustainable, waterborne system that produces minimal waste, has low volatile organic compounds (VOCs) and helps reduce aircraft fuel consumption due to weight savings provided by the lower paint usage.
“We are always looking for innovative and efficient ways to improve our aircraft painting capabilities for our customers, as well as contributing to the decarbonization of the aerospace industry,” says Christophe Cador, Satys president and CEO.
The company says the 2,100-gallon (eight cubic meters) ecoat tank at Dugny will be the largest in Europe, enabling a single operator to coat several parts at once, further increasing the efficiency of the process. The coated parts are corrosion and chemical resistant, and compatible with industry standard pretreatments and topcoats.
Related Content
-
Anodizing for Bonding Applications in Aerospace
Anodizing for pre-prep bonding bridges the gap between metallic and composite worlds, as it provides a superior surface in many applications on aluminum components for bonding to these composites.
-
Advancing Aerospace Connectors
OEMs looking to optimize aircraft performance and range are turning to composites and plastics, which require specific finishing treatments.
-
Eliminating No-Value-Added Services Adds Value for Customers
Answering questions about how to best meet customer needs led this Products Finishing Top Shop to stop using trucks to provide value-added services and instead, start offering in-house solutions.