10 Ecoat Best Practices
Following this list of guidelines can help to increase the performance, cost effectiveness and quality for your ecoat operation.
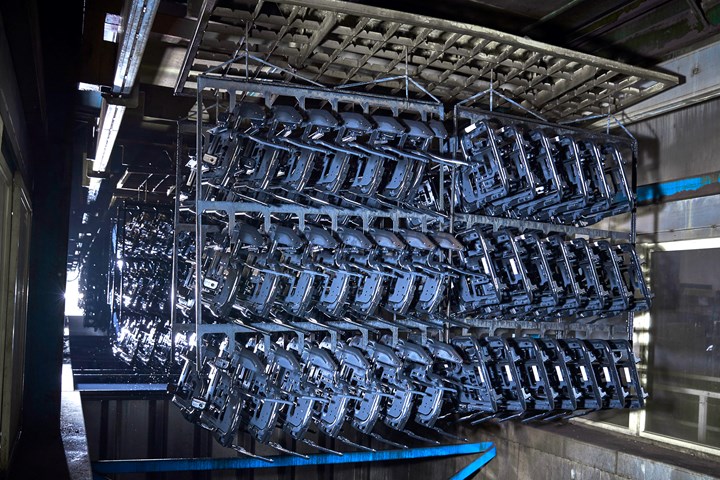
ECOAT24 is a great opportunity to educate new employees, learn about the latest ecoat technologies and brush up on your fundamental knowledge of electrocoating processes. Below, you’ll find a list of 10 electrocoating best practices to help ensure optimal performance and quality for your ecoat operation.
1: Preparation is Key: It is important to thoroughly clean and pretreat the substrate before electrocoating. Surface cleanliness is vital for successful adhesion and achieving a uniform coating.
2: Proper Racking and Fixturing: Efficient racking and fixturing of parts is an important factor in achieving consistent coating coverage. Properly designed racking aids in maintaining uniform electrical conductivity and can help minimize the risk of coating defects.
Learn more: Looking for ideas for optimizing and managing your racking procedures to improve productivity? short.pfonline.com/goodrackdesign
3: Quality Pretreatment: High-quality pretreatment processes, including cleaning and rinsing, help to ensure proper surface preparation. Effective pretreatment, including phosphate or zinc phosphate conversion coatings, is an important step for removing contaminants, as well as for improving adhesion and corrosion resistance.
Learn more: In addition to traditional phosphate-based pretreatments, phosphate-free alternatives reported to be more environmentally friendly are available. Check out this article on Optimizing Ecoat With Zirconium Pretreatment. short.pfonline.com/ecoatzirconiumpretreat
4: Optimized Bath Parameters: The regular monitoring of electrocoating bath parameters such as temperature, pH levels, conductivity and bath chemistry is a crucial component of your process. Maintaining these parameters within specified ranges aids in process stability and consistent coating quality.
Learn more: Addressing low pH levels in your ecoat bath: short.pfonline.com/lowpHecoat
5: Uniform Film Thickness: Performance and aesthetic requirements rely on consistency in coating thickness. It is important to control the voltage, current density and deposition time in order to achieve the desired film thickness uniformly across all parts. Ensuring proper grounding of parts is another essential factor for achieving an even and uniform coating.
Learn more: The regular monitoring, recording and charting of throwpower can be a very valuable tool for ensuring quality. short.pfonline.com/ecoatthrow
6: Proper Masking: Masking techniques can be used to protect specific areas of parts from being coated where necessary.
Learn more: Are you weighing the costs of a custom masking solution vs. an off-the-shelf solution? Explore the overall savings that can be realized with custom masking. short.pfonline.com/custommask
7: Filtration and Maintenance: Clean filtration aids in sustaining bath chemistry, preventing defects and ensuring coating quality. It is crucial to maintain and regularly replace filtration systems in the electrocoating bath to remove impurities and contaminants.
Learn more: Check out these best practices for ecoat paint ultrafiltration systems: short.pfonline.com/ecoatultrafiltration
8: Monitoring and Testing: Implement a robust system for monitoring and testing the coating thickness, adhesion, and other critical quality parameters. Regular inspections and testing procedures ensure compliance with standards and specifications.
Learn more: What are the best practices for testing an automotive electrocoat system? short.pfonline.com/ecoatqa
9: Efficient Curing Process: Use an efficient curing process post-coating to achieve the desired film properties. Make sure the curing temperature and time align with the coating’s specifications to enhance durability and performance.
Learn more: Recent innovations in ecoat technology allow for an expanded bake window to enable the curing of diverse substrates of varying thicknesses. short.pfonline.com/ecoatcure
10: Continuous Training and Improvement: Provide comprehensive training to operators and personnel involved in the electrocoating process. Encourage a culture of continuous improvement by soliciting feedback, analyzing defects and implementing corrective actions.
These best practices can help you optimize efficiency, consistency and quality in your electrocoating processes and can be used as a starting point or reminder. Embracing these guidelines can contribute to enhanced performance, prolonged equipment life, reduced rework, and the overall cost-effectiveness and success of your electrocoating operation.
Related Content
Masking Solutions Provider CFS Dramatically Expands Capabilities and Capacity
Custom Fabrication & Supplies (CFS) completed a new plant expansion packing 10 times the capacity into twice the space. It dramatically enhances the supplier’s custom capabilities to provide extremely precise and cost-effective masking solutions.
Read MoreInstalling an Ecoat Line
Thinking of investing in electrocoating capabilities? George Lovell, coatings plant manager for Lippert, discusses considerations you should keep in mind as you add your ecoat line.
Read MoreTTX’s Automated Conveyor Carrier System Offers Wireless, Flexible Operation
ACC system designed for reliable, consistent point-to-point movement of everything from small to heavy parts.
Read MoreCFS Unveils New Hook Locks Parts Racking Solution
New product from Custom Fabricating & Supplies (CFS) prevents part loss during coating processes.
Read MoreRead Next
Delivering Increased Benefits to Greenhouse Films
Baystar's Borstar technology is helping customers deliver better, more reliable production methods to greenhouse agriculture.
Read MoreA ‘Clean’ Agenda Offers Unique Presentations in Chicago
The 2024 Parts Cleaning Conference, co-located with the International Manufacturing Technology Show, includes presentations by several speakers who are new to the conference and topics that have not been covered in past editions of this event.
Read MoreEpisode 45: An Interview with Chandler Mancuso, MacDermid Envio Solutions
Chandler Mancuso, technical director with MacDermid Envio discusses updating your wastewater treatment system and implementing materials recycling solutions to increase efficiencies, control costs and reduce environmental impact.
Read More