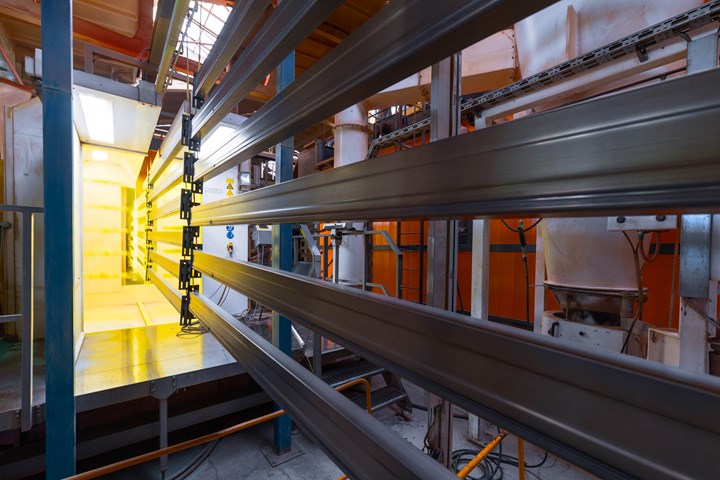
When wanting to increase productivity, the best, most efficient and practical way is to improve your line density.
Photo Credit: Vitracoat Inc.
When I was a kid, my big brother took me to my first (other than animated) movie called The Dirty Dozen. It was an army movie where the government needed a few men to complete a very dangerous mission where it was likely no one would make it out alive. So they selected a team of misfits from the Army prison system and gave them a choice to continue to do their time or join this team.
The list of powder coating tips that follow are my own Dirty Dozen — misfits that are typically ignored, misunderstood or not given enough attention. Before we get started, let there be no mistake, there are many others — I simply selected these 12 from a list I created through the years and advice I received from fellow experts in the industry.
The reality is running a powder line has some procedures that are considered “must do” or nothing can be processed — but these items, the Dirty Dozen, can be handled poorly or even ignored in some cases, and you can still get powder coated parts. I want to go deeper into the top 12 aspects of powder coating that can take your operation to a new, improved level.
Keep in mind that many of these Dirty Dozen work together and with poor management of one, one or more of the others can be negatively effected.
1 — Write a Specification
The architecture of a specification could be the subject of an article on its own. I want to make it clear that writing a specification is a very important way to elevate your coating operation as it will become the tool by which you determine a pass or failure of the coated part. The specification clearly defines all the areas that will be measured to provide a quality product, explains how to measure those areas, and most importantly, identifies how to determine if a coated part is rejected. The specification, if written properly, should remove the majority of the subjectivity in the evaluation process. Your specification defines all the tests your coated product must pass to meet your expectations and/or those of your market. However, in order to start this process, two things must be known:
- What atmospheric conditions will your coated part be subjected to?
- How long do you want it to last in that atmospheric condition?
Make sure when developing your specification that you are not reinventing the wheel. Use templates your powder vendor can supply you, as well as ASTM test methods, AAMA guidelines, and guidelines from PCI and/or APCA, just to name a few.
2 — Film Build Control
If you only have a few dollars to spend on a powder system to improve your process, buy a film gauge. This is an essential tool for all powder coatings operations. Next, put together a process to measure your film build on each part. Once you start measuring and documenting what you have, you can then start finding areas to improve your control. The idea is once you start measuring something you can then start to manage said something,
3 — FPTE
First pass transfer efficiency (FPTE) is the amount of powder sprayed from a device that sticks to the part. The remaining powder can be reclaimed or sprayed to waste. First pass transfer efficiency has many facets starting with the setup of the spray gun(s) minimizing the speed in which the powder is sprayed, giving the powder the best chance to adhere to the part. Ground, gun to part distance, set up angles using lead and lag, air flow, part geometry and last, but in many cases not least, the powder formulation — a formula that has been designed for your application.
4 — Particle Size Management
If the idea is to maintain a consistent, high-quality appearance with your powder coating operation, then the ability to have a particle size management program is very important. This starts with a partnership with your vendor on a particle size distribution specification — a process to manage your virgin powder to reclaim ratio, optimal line density and first pass transfer efficiency.
5 — Line Density
When wanting to increase productivity, the best, most efficient and practical way is to improve your line density or at least look at this first before you start increasing line speed. While increasing line speed will in fact push product through at a faster level, it also reduces the dwell time in all areas needed to produce an optimal powder coated part. On the flip side, increasing or improving line density allows your process to improve simply by increasing the amount of product in the given silhouette.
6 — Training
Many training programs include being trained from the old guy who was trained by the older guy who was trained by the dead guy. While it may work, this approach does not develop any consistency, structure or true knowledge transfer. What you want to create is the ability to assure whomever is doing the job is doing it the same way every time. Develop training programs, use videos to make points and assure the new guy does it the same way as the next guy.
7 — Powder Selection
Once you understand the atmospheric conditions your part will be subjected to and have defined an idea of how long you want it to last in that atmosphere, you have a very good starting point. With only this information, you can narrow down to the field to if powder coating with UV resistance is required or not. From there, you take one performance requirement at a time, removing chemistries along the way.
8 — Use of a Primer
When selecting a powder coating, the use of layers should also be considered. Additional layers can provide increased protection for times when the atmospheric condition is more harsh than what you may consider a normal application — all without the need to change your standard powder coating. The use of layers allows you to offer two performance options and allow the consumer to select the ones that will best suit their needs.
9 — Part Design
One of the most missed or ignored parts of a powder coating process is looking at the way a component of a product is engineered and/or fabricated. Look at how and where welds are placed and consider whether the part has hidden areas where powder or pretreatment will not be able to reach or protect. By taking time to consider the part design itself, you can assist your powder coating in its goal to help the part or product last longer.
10 — Air Management
In any powder coating operation, there are many air sources and they all should be checked regularly, before it’s too late. First is compressed air where not only the PSI (pounds per square inch) needs to be adequate, but also CFM (cubic feet per minute) — the volume must be maintained. But what about LFPM (lineal feet per minute) — the velocity of air moving throughout the opening of a powder booth? Your regular maintenance program should check these areas before you see an issue.
11 — Trouble Shooting
When you have trouble (and you will have trouble) — what process do you use? The natural impulse is to start turning knobs until the problem goes away. If this works (and in some cases it may), it only shows that you have turned the correct knob. In the process, you have also most likely turned a knob or two that were not needed to address the problem and will impact something else. The best and most practical way to troubleshoot is to use the SIRE method.
- Step 1: S – Search
- Step 2: I — Identify
- Step 3: R — Recreate
- Step 4: E – Eliminate
The SIRE method allows you to take the time and find the root of the problem by using the process of elimination.
12 — Making Partners
I left this one for last, but it should be considered as something you do in the beginning: Pick good partners to join you in the journey. Your application equipment partner, your powder coating vendor and/or your chemical pretreatment supplier — all of these organizations want you to have an optimal, self-sustaining process and have expertise in-house to help you get there!
About the Author
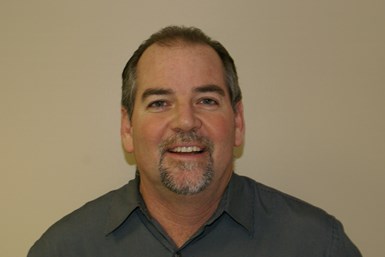
Steve Houston
Steve Houston is vice president of business operations at Vitracoat America. Visit vitracoat.com.
Related Content
Unique and Evolving Electroplating Training
Offering a standard online course as well as on-site custom courses, this training firm uses student feedback to continuously improve its courses to reach industry training needs.
Read MoreWorkforce Education is Never Finished
Educational initiatives in the industry offer training/learning opportunities for professionals who are entering the industry to seasoned employees as well as introductory programs for high school and college students.
Read MoreTake Advantage of Finishing Industry Educational Opportunities
Looking into training opportunities within the industry? Here’s some advice to help you seek out finishing industry education and make the most of it.
Read MoreAdjusting Current and Voltage When Powder Coating
Which manual powder coating gun setting is better to adjust, voltage or current? Jeff Hale of Gema USA discusses when to use different settings on your powder gun to achieve optimal results.
Read MoreRead Next
Calculating the Cost of Powder Coating
How can you calculate the cost of powder coating a component if you only know its surface area? Powder coating expert Rodger Talbert has the answer.
Read MoreThe Powder Coating Process
Powder coating is one of the most durable finishes that can be applied to industrial manufactured products, and offers excellent corrosion protection and is very safe because of its lack of volatile organic compounds. To understand the powder coating process you should start with the fundamentals.
Read MoreDevelopments and Trends in Powder Coating
New solutions for powder coating centers combine powder preparation, conveyance, dosing and color changes into a fully automated, closed system.
Read More