Changing From Liquid to Powder Coating
Will the powder coating perform better than your liquid system? Products Finishing columnist Rodger Talbert discusses considerations you should consider when making the switch.
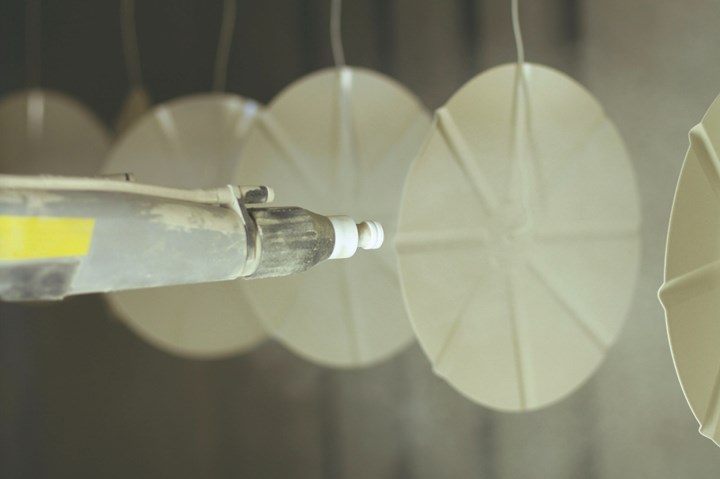
Q: We make components used by agricultural and construction equipment manufacturers. Some of our parts are coated before assembly by outside suppliers, but most of our products are painted after assembly with all of the parts including fasteners, belts, hydraulics, and other parts already in place as part of the assembled product. We have been asked by some of our customers to consider powder coating instead of the liquid paint we use now to reduce our environmental impact, but we do not see how we can use powder coating on our assembled product with all of the temperature sensitive components. We are not sure if our oven is capable of curing powder. Are there any low temperature cure powder coatings that we could use? Do we need to start coating all of our parts before assembly? If we need to coat the parts before assembly, will the powder coating be damaged when we fit the parts together during assembly? We are also wondering if the powder will provide better field performance than our current liquid paint and if it will work in our system.
A: Will the powder perform better than your liquid? That depends on the specific liquid paint you are using. A powder can perform as well as or better than many liquid paints and it does not usually require a primer coat. If you are having some issues now you may have a lower performance liquid coating and the powder will be better. For the toughness and durability that a single coat of powder can provide, you would usually need a primer and a superior liquid topcoat. Chances are your performance will be better with the powder. Performance should not be an issue.
Can it work in your system? That will depend on your pretreatment system and your cure oven.
Powder is not tolerant of dirt, grease or surface imperfections. Liquid paint can sometimes work over slight contamination, though it is not a good idea to do it for outdoor product with higher performance expectations. You need a very clean part and a good conversion coating. If you can get a clean part and you have enough oven time and temperature, you should be able to run powder
Typical powder cure temperatures for powder are between 375°F and 400°F for 10 to 15 minutes of peak metal temperature. There are some polyester formulas that have the needed UV resistance and will cure at lower temperatures, but they will still be above 320°F, a temperature that will most likely cause damage to rubber, plastic or other materials that you use in your assemblies. The good news is that you can coat before assembly and the powder is durable enough to take some abuse during assembly. It sounds like a big undertaking to change your manufacturing operation, but it can be done and there are substantial rewards in efficiency and quality when parts are coated on a high-production line instead of being painted as fully assembled units. The coating covers areas that may not be reached in the assembly too.
Get in touch with a powder supplier and run some tests to confirm that you can coat and cure powder and it will perform as well as or better than your current liquid. You may have to go through some extensive changes, but in the end, you should be able to save money and get better results.
About the Author
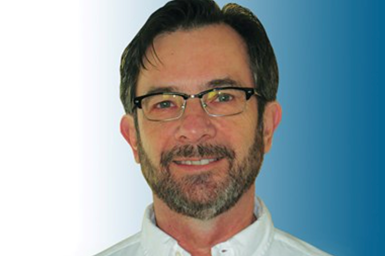
Rodger Talbert
Rodger Talbert has more than 30 years experience in the powder coating industry.
Related Content
Surface Prep Solution for Rusted Rebar in Concrete
Julie Holmquist of Cortec Corporation discusses passivating corrosion on rebar and other reinforcing metals.
Read MoreHow to Address Declining Powder Coating Coverage Over Time
Fine particles from reclaim could be to blame for powder coating problems that emerge over time. Avoid problems by keeping hooks clean, maintaining guns and using reclaim powder quickly to avoid accumulation of fines.
Read MoreMasking Solutions for Medical Applications
According to Custom Fabricating and Supplies, a cleanroom is ideal for converting, die cutting, laminating, slitting, packaging and assembly of medical-grade products.
Read MoreCorrosion Resistance Testing for Powder Coating
Salt spray can be useful to help compare different pretreatment methods and coatings but it does not tell us much about the corrosion resistance of a part over time in the field. Powder coating expert Rodger Talbert offers insights into how to get a better idea of how to improve a part’s corrosion resistance in the real world.
Read MoreRead Next
Proper Sieve Size for Powder Coating's Smooth Results
Kevin Biller at ChemQuest Powder Coating Research gives recommendations for sieve size to ensure surface smoothness.
Read MoreRecoating Best Practices
Powder coating consultant Rodger Talbert offers advice for recoating successfully without excess orange peel or inconsistent gloss.
Read MoreCauses for Cross Contamination
Cross contamination of powder coatings is often the result of poor habits in the powder room. Powder coating consultant Rodger Talbert offers an example of how to mitigate cross contamination.
Read More