Conscious Cleaning Considerations
Reassessing your cleaning process? Connor Callais of Hubbard-Hall offers an in-depth discussion of what you should keep in mind.
Q: We’ve been having trouble getting good coverage in our immersion iron phosphate process prior to powder, resulting in several reworks and off-spec parts. This issue arose about the same time our supplier switched to a stearate-based lube, so I believe we need to reassess our cleaning process, but not sure where to start?
A. Iron phosphate chemistries and other pretreatment methods are designed to provide enhanced physical and performance properties to the finished part or surface. These applications are employed in various industries — from automotive and aerospace to construction, firearms and others — to improve the durability and reliability of the product in the field. While a few factors influence the efficacy of the phosphate coating, adequate cleaning and surface preparation are paramount to ensuring that the coating is uniformly applied and effectively adhered.
The primary objective of any surface preparation is to ensure that the substrate is entirely free of organic and inorganic contaminates and otherwise address any characteristics hindering the development or quality of the impending phosphate application. Organic contaminants are characterized as carbon-based molecules; this includes natural and synthetic oils, pre-existing rust inhibitors, machining and metalworking fluids, waxes, lubricants and more. Inorganic contaminants are another form of surface imperfection and a common inhibitor to effective coatings; these include mill and heat-treat scale, base metal surface oxidation (corrosion/rust), and smut. The targeted removal of all present contaminants is a key aspect of a successful surface preparation and phosphate coating.
Cleaning and surface prep can be achieved mechanically, chemically, or through a combination of both. Mechanical methods can include blasting and wire brushing, and while these are effective techniques, they are often not practical or cost-effective at scale for many applications. Chemical applications use solvent or aqueous products to process and prepare parts at scale through batch or continuous cycles.
Aqueous cleaners are vast and varied in formulations and functions, often designed with a focus on specific applications or purposes. Typically, the first level of classification or segregation would be based on the cleaner’s primary builder(s); consequently, this translates to its relative acidity/alkalinity as well:
- Acid-based cleaners are formulated using mineral and organic acids, resulting in pH levels <6. These cleaners are commonly, but not exclusively, used in non-ferrous substrate applications and are highly effective in de-rusting, deoxidizing, and descaling various inorganic contaminants.
- Neutral to mildly alkaline cleaners can be made with a host of builder chemistries, including phosphates, amines and silicates. These cleaners can range in pH from roughly 6.5–10.5 and are generally multi-metal safe.
- Caustic cleaners utilize sodium and/or potassium hydroxide and have pH levels >11; these are often very effective in cleaning ferrous substrates and are commonly used prior to phosphate coatings. Under the right operating conditions, these products can also effectively de-rust surface oxidation.
In addition to these builders, aqueous cleaners possess a range of specialty components to address various contaminants. Organic soils generally have low-to-no solubility in water, so aqueous cleaning applications employ surfactants packages to increase their solubility and remove them from the substrate. Caustic cleaners can also facilitate the chemical reaction of saponification, whereby larger organic molecules (soils) are cleaved into fatty acid salts or soaps. Additionally, cleaners can use several other agents to offer properties such as chelation, sequestration, mild corrosion protection, brightening, and more.
Beyond the chemical makeup of the cleaner, three vital operating parameters play a critical role in the cleaner’s performance: time, temperature, and concentration. These parameters are direct variables to balance the application’s needs and limitations. Phosphate baths typically use caustic-based cleaners as the substrates are customarily ferrous and caustic cleaners tend to be the most robust. Immersion time is typically in the range of 5-10 minutes but can extend as necessary. Temperature is also quite variable, with operating ranges from 150°F up to 200°F; temperatures at the top of that range can be required for more tenacious materials such as stearate lubes and polymeric compounds. Lastly, concentration also influences the efficiency and activity — immersion cleaners typically run at 5-10% v/v but can be run at up to 20% v/v for applications where corrosion or extensive contamination is present. Modifying any of these parameters can improve the cleaning performance and, in turn, improve the phosphate’s crystal formation, coverage, and adhesion properties.
Other aspects worth assessment include the set-up and maintenance of the cleaning operation. Immersion cleaners can be either emulsifying or oil-splitting. Emulsifying cleaners are ideal for barrel-processed parts and are functional until the surfactant capacity is saturated. Conversely, oil-splitting cleaners are preferred for racked parts and in applications where considerable organic contaminants are being removed. The fixturing with respect to the part’s geometry can also impact the cleaner’s performance as recessed areas and concavities need adequate solution contact and flushing action. Active filtration of the cleaning solution ensures that the bath is not becoming oversaturated with soils. Lastly, bath maintenance is undoubtedly something that should not be overlooked. Daily checks for temperature, concentration titrations, and visual inspection of the cleaning solution ensure that work is processed consistently according to your application’s specifications. Judicious care for the daily operations of the cleaner baths translates to mitigated periodic maintenance as bath quality is kept in spec, leading to few bath dumps and tank cleanouts. These, among others, are all influencing factors to be aware of in evaluating and troubleshooting a cleaner issue.
Considering the totality of the cleaning application and understanding the variables in effect is crucial to evaluating and troubleshooting any cleaning issue. Each application is unique, from the equipment being used, to the part’s substrate and geometry, to the contaminants needing to be addressed. Often, a minor adjustment in the operating parameters or fixturing can address the issue; other times, with more substantial changes, you may need to consider alternative chemistries better suited to your application. Consult your chemical supplier for troubleshooting guidance and product input whenever in doubt.
About the Author
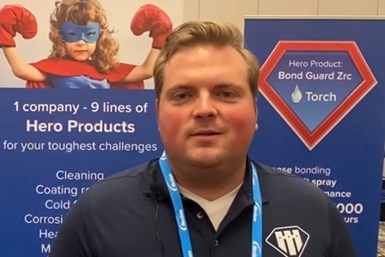
Connor Callais
Connor Callais is an applications specialist for Hubbard-Hall. Visit hubbardhall.com.
Related Content
How to Address Declining Powder Coating Coverage Over Time
Fine particles from reclaim could be to blame for powder coating problems that emerge over time. Avoid problems by keeping hooks clean, maintaining guns and using reclaim powder quickly to avoid accumulation of fines.
Read MoreHow to Choose Between Sulfate and Chloride-Based Trivalent Chromium
There are several factors to consider when choosing between sulfate and chloride-based baths for trivalent chromium plating. Mark Schario of Columbia Chemical discusses the differences and what platers should keep in mind when evaluating options.
Read MoreSurface Prep Solution for Rusted Rebar in Concrete
Julie Holmquist of Cortec Corporation discusses passivating corrosion on rebar and other reinforcing metals.
Read More3 Tests to Ensure Parts are Clean Prior to Plating
Making sure that all of the pre-processing fluids are removed prior to plating is not as simple as it seems. Rich Held of Haviland Products outlines three tests that can help verify that your parts are clean.
Read MoreRead Next
The Case for Parts Cleaning
Understanding the consequences and costs of not cleaning well.
Read MorePretreatment for Painting
Better adhesion, enhanced corrosion and blister resistance, and reduced coating-part interactions make pretreatment a must.
Read MoreAqueous or solvent-based cleaning?
Considerations for choosing the right cleaning solution.
Read More