Control of Powder Film Thickness
Powder coating consultant Rodger Talbert offers insights for film build control when powder coating.
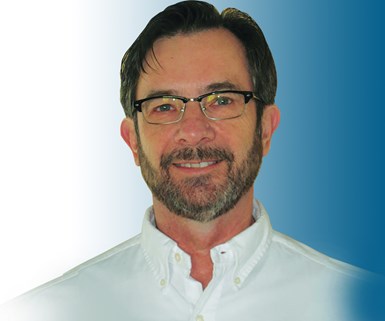
Rodger Talbert has more than 30 years experience in the powder coating industry.
Q: We are powder coating metal furniture and we have trouble getting uniform film thickness on all areas of the parts. We have a wider variety of shapes and sizes from very small fittings to 12' long benches. A lot of the products are fabricated with tubing but we also have some plate and flat stock construction. Our application is all manual with one sprayer on each side of the part. The line speed is between 4 and 6 FPM depending on the metal gauge and complexity of the part being coated. Our minimum film thickness is 3 mils to get the performance we need but we actually get anywhere from 1.5 to 5 mils on a regular basis. We need suggestions on how to adjust our spray guns to apply more uniform coverage.
A: Film build control starts with earth ground. If you have a lot of inconsistency in film thickness I would first make sure that your hooks are clean and you maintain good ground at all times. From a safety perspective, the industry recommends resistance lower than 1 megaohm from the part to the ground rail or other ground source. Personally, I would strive for zero resistance for efficiency. Measurement of ground is often done with a megger due to the high voltage output. I use a high-quality multi-meter because it is more sensitive to a minor powder build on the area being measured and if it says zero I know I have the best possible ground.
Rack design is also important to achieving good application uniformity. Parts should be profiled as much as possible to avoid having to throw powder around one surface to get to another or reach around some area to get to an inside space. Keep the profile of the parts as accessible as possible so that all areas can be reached with a limited amount of angles or stretching. Avoid inconsistent racking and keep the racks in good repair. Always fill the rack up if possible and fix bad contacts. Dense racking (more metal, less empty space) is good up to a point. It improves efficiency and consistency. Just be careful to control the amount of the metal so that your sprayers can access all surfaces easily and keep up with the volume.
As for gun set-up, there are a few guidelines that help:
- Make sure the powder is properly fluidized; too much or too little fluidizing air will cause spitting and break up the spray pattern. Keep the hopper as level as possible during the production day.
- Adjust the voltage and microamps to a comfortable number; I start with full voltage and current at around 40 microamps. On flatter surfaces, the current may go a little higher. On complex surfaces with inside corners, the current can be lower.
- Adjust the flow rate to a moderate output and make sure that the pattern is smooth and consistent. It is critical that the powder cloud have steady, lower velocity and the whole pattern is even, no spurts or heavy tails of powder in the pattern. I start a gun out at around 30 pounds per hour (4 grams per second). On a typical volume-based controller, that would be around a total air volume of 4.0 Nm3 (Normal Cubic Meters) with a powder percentage setting of 40%.
- The sprayers should research and develop a consistent pattern and do it the same way at all times. Steady, slow strokes starting in the Faraday cage areas and working out to the easier surfaces from the inside corners.
- Make sure the coaters are not rushed and have enough time to coat the parts. If they have to work too much they will turn up the flow rate and get more random in the spray pattern.
Practice and be consistent with moderate flow rates. Use slow and steady strokes. Start in the Faraday cage areas (recesses) and work to the flatter surfaces. If your sprayers follow these rules they should get the uniformity that you need.
Related Content
Trivalent Chrome Overview
As the finishing industry begins to move away from the use of hexavalent chromium to trivalent chromium, what factors should finishers consider as they make new investments? Mark Schario, chief technology officer for Columbia Chemical offers a helpful overview of this complicated topic.
Read MorePrevent Plating Problems with Critical Inspections
Tanks and their contents should be regularly inspected visually and analytically. When a quality issue arises, it is important to quickly pinpoint where the main problem is by checking which parameter is out of line.
Read MoreAdjusting Current and Voltage When Powder Coating
Which manual powder coating gun setting is better to adjust, voltage or current? Jeff Hale of Gema USA discusses when to use different settings on your powder gun to achieve optimal results.
Read MoreHow to Address Declining Powder Coating Coverage Over Time
Fine particles from reclaim could be to blame for powder coating problems that emerge over time. Avoid problems by keeping hooks clean, maintaining guns and using reclaim powder quickly to avoid accumulation of fines.
Read MoreRead Next
Understanding AAMA Specifications
Powder coating consultant Rodger Talbert explains AAMA specifications and considerations coaters should make before taking on work required to meet those standards.
Read MoreTGIC Powder Coatings vs. Non-TGIC Powder Coatings
As raw materials become increasingly scarce, powder coating consultant Rodger Talbert offers insights into using non-TGIC products.
Read More