Conveyors and Paint Systems
Choosing the right conveyor system, coating technology, and ancillary equipment.

Powder coatings are applied by electrostatically spraying charged powder so that it is attracted to the parts or by dipping heated parts into a fluidized powder bed so that powder melts onto the hot surface. Most coating systems use electrostatic spray.
The selection of a paint- or powder-finishing system depends on a number of factors, including the types of parts being coated, the required surface-treatment process, size and weight of the parts, sequence of process steps, and the flow of material through the entire fabrication process.
The finishing line layout should be planned based on the space requirement of the process equipment and the available space. Route the conveyor so as to carry parts from the loading point in the fabrication area through the process system to the unloading point in the assembly/shipping area. This concept will minimize material handling/damaged parts and personnel required.
Conveyor Systems
For liquid-paint process lines, mainly two types of conveyor systems are used.
Overhead monorail conveyors have the load-carrying and the drive functions combined in one element—the endless chain. This chain is guided by a rail system based on either an I-beam or an enclosed track. A take-up station overcomes chain slack caused by temperature variations or wear. A caterpillar drive or a sprocket in a turn drives the chain. Parts are suspended from the chain by special attachments or load bars. This conveyor can follow only one path—deviations are not possible. This system is simple and efficient, but not very flexible.
Overhead power and free conveyors are two-rail systems. The load-carrying element, (trolley) and the driving element (chain) are separated. The trolleys use the lower “free rail,” and the chains are in the upper “power rail.” Pusher dogs establish the connection between chain and trolley, and they can be engaged and disengaged as needed. The “free rail” can be equipped with switches, lifting stations or stops to allow the trolleys to follow several different paths, or be lifted or lowered, stopped, or moved at different speeds through the system. The entire conveyor system is PLC-controlled.
This system is more costly, but it is flexible enough to link fabricating processes, paint lines, assembly and shipping, and to accommodate process variations within these areas. It will also reduce the number of personnel and the cost of transporting parts through several fabrication steps. Because of this, the danger of damaged parts through various manual handling steps is greatly reduced.
Other Conveyor Systems
Besides the two systems previously described, there are several other systems used to lesser extents for finishing:
- Automatic hoist systems for dip processes (typically e-coat and dip pretreatment).
- Square-transfer systems (applications similar to those for hoist systems).
- Inverted monorail or power-and-free conveyors.
- Roller conveyors for transporting skids of parts or assemblies.
- Dual-chain and drag-chain conveyors for dolly systems.
Any of the above conveyor types can be combined to provide the optimum paint system for a specific application. Conveyor systems will reduce manual handling of the parts, minimizing labor costs and the potential for damage.
Process Equipment
In most cases, a paint or powder coating line consists of two portions: the pretreatment system and the coating section.
Pretreatment systems produce a substrate surface suitable to receive the coating. These systems are intended for cleaning, phosphating and similar treatments. Pretreatment chemicals are normally in aqueous solutions and may be used in steam-cleaning applications. Vapor degreasing/phosphating is also used. Mechanical cleaning, such as shot blasting, is another means for treating parts prior to cleaning.
Each pretreatment process starts with cleaning of the parts, followed by application of conversion coatings such as iron or zinc phosphates or chromates. Recently, a new generation of conversion coatings called nano ceramics have been developed. These new conversion coatings can operate at lower temperatures and generate significantly less sludge than iron or zinc phosphate processes. They are also more environmentally friendly. The process sequence also includes the required rinses. Spray or dip or combinations thereof could apply the process steps mentioned here, depending on part configurations and process steps required.
A dry-off oven typically follows the pretreatment process. The oven normally operates at approximately 300°F and is heated by natural gas. If gas is not available, fuel oil, electricity or steam can be used. Note: Dry-off ovens are not built to evaporate water puddles. All water collections must be drained prior to dry-off.
Ancillary equipment for pretreatment systems includes oil-water separators, sludge-removal systems such as filters or centrifuges, heating systems (hot water), chemical feed/metering systems, and demineralizers/deionizers. Different coating processes require specific pretreatment steps. Electrocoat, for example, requires a final rinse with deionized water before entering the e-coat tank.
Paint Application
Paint is provided in two different forms: liquid and powder.
Liquid paint is provided as solvent-thinned or water-borne material. Spraying or dipping can apply both types of paint.
Powder coatings are applied by electrostatically spraying charged powder so that it is attracted to the parts or by dipping heated parts into a fluidized powder bed so that powder melts onto the hot surface. Most coating systems use electrostatic spray.
All liquid paint application systems (except for e-coat) require these process steps:
- Paint application (spray or dip).
- Solvent/water flash-off (evaporation).
- Paint curing.
Electrostatic powder coating application requires two process steps:
- Powder application.
- Powder melt/curing.
Spray painting
Liquid paint can be applied using manual or automatic spray guns. In either case, the spraying is done in a ventilated enclosure equipped to remove and filter out overspray paint. The amount of paint particles that may be discharged into the atmosphere is regulated by the EPA.
The enclosure either has a work opening through which the air moves into the spraying area or is completely enclosed and equipped with an air-supply plenum. The purpose of the enclosure is to contain paint overspray and solvents.
Dry filters (paint arrestors) or water-wash systems (scrubbers) remove overspray particles from exhaust air. A dry-filter system is normally used for low-volume painting. This system can be installed relatively economically, but requires purchase of filter materials and the proper disposal of these materials after they are loaded with paint overspray.
The water-wash system (scrubber) costs more but does not need the constant exchange of filter materials. By using a co-agulating agent in the water flowing through the water-wash curtain that traps overspray, you can detackify the overspray paint trapped in the curtain. Then you can remove it from the system as paint sludge. The scrubber system provides a constant airflow, does not require interruptions of production for filter changes, and will take a heavier load of overspray. Solvent-based and waterborne paints can be applied in the same type of spray booth.
Dip application
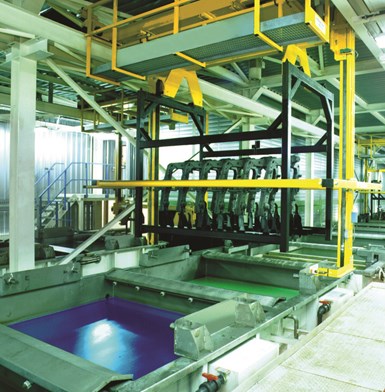
Both types of dip paint—solvent and waterborne—use the same type of dip tank. This tank has a paint-recirculation system to prevent settling of the paint material, and (if required) a paint-cooling system. The dip tank should be in a ventilated enclosure that prevents solvents from entering the surrounding area.
Both types of dip paint—solvent and waterborne—use the same type of dip tank. This tank has a paint-recirculation system to prevent settling of the paint material and (if required) a paint-cooling system. The dip tank should be in a ventilated enclosure that prevents solvents from entering the surrounding area.
Flash-Off and Curing
After paint application and prior to curing, the solvents need to “flash-off” to prevent bubbling of solvent evaporating from the paint as higher temperatures are applied in the curing oven. Flash-off normally happens at ambient temperatures in an enclosed, ventilated area. The exhaust of this enclosure is discharged into the atmosphere (or to an air-pollution-control system).
After flash-off, the paint cures at oven at temperatures of 175–400°F, depending on the type of paint used. The most common oven heats air using natural gas and convection. Infrared (IR) ovens are also used. Other curing systems such as UV are highly specialized and will not be discussed here.
Generally, it’s advisable to use the paint supplier’s recommendation for design of the curing oven. Each oven needs to fulfill safety requirements for the heating system (gas trains), purging cycles, exhaust-air volumes and pressure-relief areas. The air exhausted from the oven discharges to the atmosphere (or an air-pollution-control system).
Powder Application
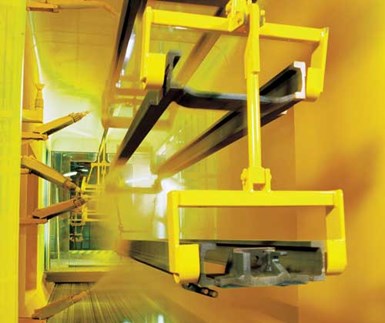
Powder coating is a very efficient way of applying a durable coating as long as large quantities of the same colors are being applied.
Powder coatings can be applied manually or with an automatic system, using electrostatic spray guns. The electrostatic charge to the powder is applied with either high voltage “corona” charging or “ tribo” friction charging. The most common equipment is “corona” charged.
The powder booth has filters that collect the overspray powder. The process is:
- Powder is stored in a fluidized hopper.
- It is drawn to the guns, charged and electrostatically attracted to the parts.
- Filters trap overspray powder.
- Filters are periodically blown down and the powder moved via a sieving unit back to the powder hopper. Powder in the hopper is then replenished.
Powder coating is a very efficient way of applying a durable coating as long as large quantities of the same colors are being applied. If many colors and frequent color changes are required, this is time-consuming and therefore expensive. The decision to introduce powder coating to a facility involves many details concerning investment, labor costs and the variety of colors and parts.
Electrocoating
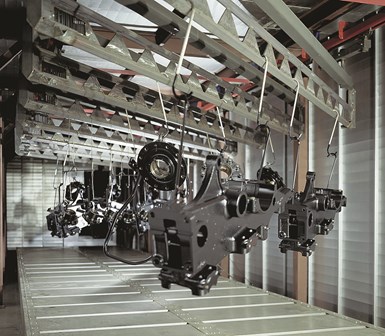
Applied in a dip tank, the water-borne e-coat paint is electrically attracted to the surface of the part. As the paint is attracted to the part surface and adheres to it, the paint deposited becomes water insoluble.
E-coat paint provides excellent corrosion resistance. Applied in a dip tank, the water-borne paint is electrically attracted to the surface of the part. As the paint is attracted to the part surface and adheres to it, the paint deposited becomes water insoluble.
There are two types of coating material, distinguished by the polarity at which they are applied in the e-coat tank. Cathodic e-coat is attracted to a cathodically connected part; anodic paint adheres to a part connected to the anode. The formulation of the paint is for one or the other type. The most common material is cathodic.
After going through the e-coat tank, parts travel through a series of rinses (spray or dip) that remove drag-out paint from the parts’ surfaces. These rinse stages are fed with permeate that is produced from the e-coat paint in the dip tank by ultrafiltration. This permeate is used to cascade the rinse containing paint particles back into the e-coat tank. Theoretically, the process is a closed loop and works without paint losses.
Proper operation of this very efficient process requires a lot of ancillary equipment: a rectifier, and systems for ultrafiltration, filtering, cooling, etc. For this reason, the investment is only feasible when high volumes of only one color must be applied.
Normally, cathodic paint is used in applying primers. The variety of colors is limited. Anodic paint has more colors available, but the corrosion resistance of the applied coating is not as good as that of cathodically applied paint.
Related Content
Installing an Ecoat Line
Thinking of investing in electrocoating capabilities? George Lovell, coatings plant manager for Lippert, discusses considerations you should keep in mind as you add your ecoat line.
Read MoreECOAT24 Issues Call for Speakers
Don't miss your chance to apply to speak at ECOAT24. Submit your abstract by June 26, 2023.
Read MoreSustainability, Electrification and Mobility
Industry events like ECOAT are good indicators of the trends that are top of mind for those in manufacturing.
Read MoreProfessional Plating Expands Zinc, Ecoat Offerings
Ever expanding, Professional Plating of Brillion, Wisc., has announced two capital investments: a second zinc line and an upgrade of its ecoat capabilities.
Read MoreRead Next
A ‘Clean’ Agenda Offers Unique Presentations in Chicago
The 2024 Parts Cleaning Conference, co-located with the International Manufacturing Technology Show, includes presentations by several speakers who are new to the conference and topics that have not been covered in past editions of this event.
Read MoreEducation Bringing Cleaning to Machining
Debuting new speakers and cleaning technology content during this half-day workshop co-located with IMTS 2024.
Read MoreDelivering Increased Benefits to Greenhouse Films
Baystar's Borstar technology is helping customers deliver better, more reliable production methods to greenhouse agriculture.
Read More