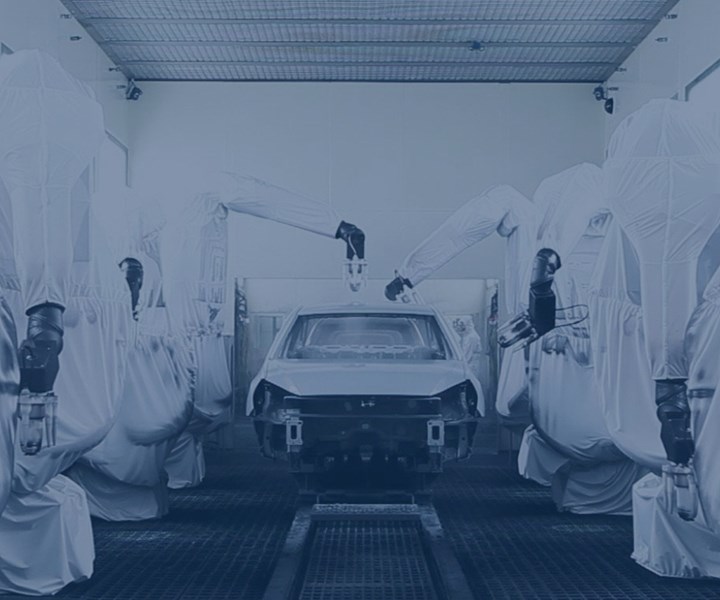
The platform is a cloud-based system that Viu Insight says will help plant managers better understand those correlations to help reduce losses in quality, productivity and cost.
An automotive manufacturing plant will make well over 250,000 vehicles per year, on average, or roughly one per minute. And no matter the make, style or color, the paint finish on each vehicle has to be flawless when it rolls out of the factory.
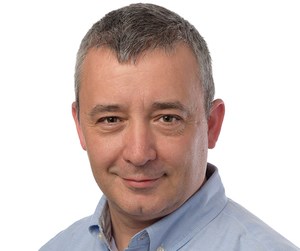
Ivan Maldonado
That’s where Viu Insight is hoping to help automakers get as close to perfection as possible in their paint processes with a data platform that takes the interactions between millions of fragmented data points collected from application equipment, automation systems and the people running them, and looking for ways to improve quality, increase productivity and improve efficiency.
“Most all automakers are good at measuring their performance,” says Ivan Maldonado, Viu Insight co-founder. “But when you consider that these paint shops all have state-of-the-art technology and thousands of sensors, there is very little going on with using the data gathered from all of those sensors to correlate the operating conditions with product quality.”
The platform is a cloud-based system that Viu Insight says will help plant managers better understand those correlations to help reduce losses in quality, productivity and cost. The magic is not just in the collection of data, but seeing how data points relate to one another.
“It’s about seeing if we can identify those correlations to particular working conditions in a process that makes that process less efficient,” Maldonado says. “The payoff is finding ways to improve those efficiencies.”
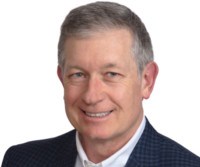
Jeff Stephens
Viu Insight is a startup that launched in 2018, and also includes managing partners Kasey Stark, who leads the operations and technical teams; David Kumaran, who directs product development and growth; and Jeff Stephens, who oversees strategic partnerships and business development efforts. This is a unique and dynamic team as they blend the experience and process knowledge of automotive manufacturing with the emerging technology expertise from Silicon Valley.
AUTOMOTIVE INDUSTRY VETERANS
Both Maldonado and Stephens have a long relationship in the automotive coating industry, with both having worked in it for many decades.
An engineer by profession, Maldonado has over 20 years of experience in highly sophisticated industrial environments in multiple countries, and has led the performance optimization of complex manufacturing operations. He increased efficiency and reduced losses at a Peugeot operation from 7% to less than 0.5% by improving processes and analyzing data. He improved and stabilized a Toyota OEM supplier operation by using data to increase availability by 13% and improved quality to 99%.
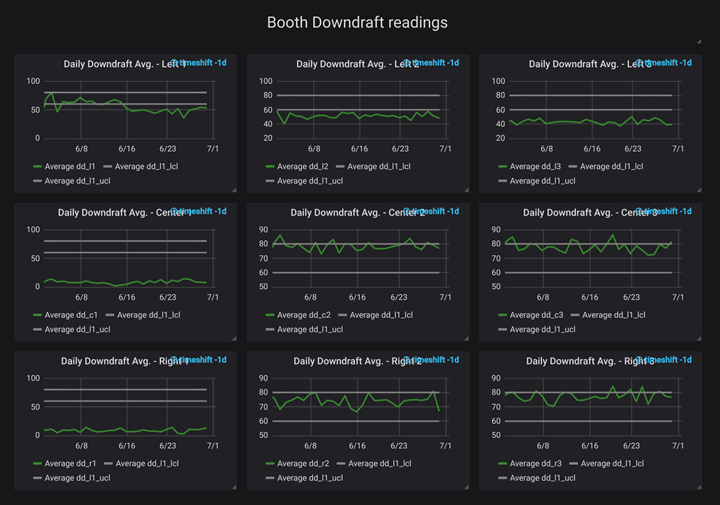
Viu Insight correlates all data points into an integrated network that allows for holistic analytics to optimize operational performance. It integrates the data within the manufacturing production apparatus, and the data foundation is used to analyze aggregated complex data sets and extract actionable information.
Stephens has been a service provider to the automotive industry for almost 30 years. Holding various leadership roles with service supplier companies, he has worked with most automotive OEMs throughout his career. Driving the design and implementation of innovative service concepts, he is well positioned to introduce emerging technology to automotive manufacturing.
“Both Ivan and I have a great relationship with a lot of OEMs, and we are getting a very common response when we talk with automotive leaders about bringing artificial intelligence and machine learning to the automotive manufacturing space,” Stephens says. “We hear, ‘we collect huge amounts of manufacturing data, but we are not utilizing it the way we should.’ That’s when they say, ‘please help.’”
What Viu Insight essentially does is correlate all data points into an integrated network that allows for holistic analytics to optimize operational performance. It integrates the data within the manufacturing production apparatus, and the data foundation is used to analyze aggregated complex data sets and extract actionable information.
NEURAL NETWORK OF NODES (N3)
Stephens says plants have multiple sources of data from spreadsheets, checklists, automation systems, business process databases and the people who operate or oversee the equipment. In addition to structured data, he says there is data that may not be currently digitized, and that the capture and connection of all structured and unstructured data is the foundation of what Viu Insight calls the ‘Neural Network of Nodes’ or N3.
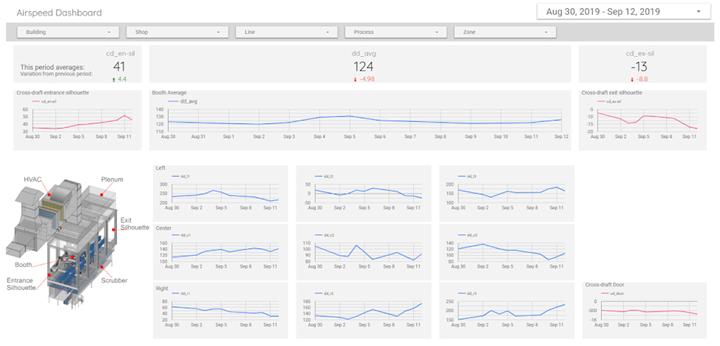
Viu’s platform measures data such as airspeed, and provides charts and graphs to demonstrate correlations.
Each data collection point is a node, Maldonado says, such as with paint guns and other coating equipment, as well as the sensors measuring downdraft in the paint booths. It can also be plant staff inspecting a product or staff performing equipment maintenance.
“By connecting the nodes, all plant data is now available to be analyzed in a holistic manner, breaking up the information silos,” he says. The Viu Insight platform then transforms the data into actionable insights, using the data to improve business logic and processes.
Some automotive OEMs in the past have been hesitant to utilize outsourced analytics of their data because of security concerns of having third-party companies access their systems and open them up to possible disruption of their flow processes.
But Maldonado says the Viu Insight platform does not need to gain access to the systems inside the plant, but rather just needs the data sent to them on a regular basis, whether it be by the minute, hour or day.
“Customers save the data in a common file in a repository outside of their systems, and then we have the capabilities to read it and analyze it,” he says. “It’s a decoupled connection and there are no issues of interfering with their controls or the management of the plant.”
LEVERAGING MACHINE LEARNING TECHNIQUES
When the company started, Stephens says the initial concept of Viu was developed as a consequence of looking for ways to optimize manufacturing processes through the use of data. Most manufacturing environments already incorporate significant levels of automation from PLCs to robots which contain numerous sensors that generate important operating data. Initially, Viu developed complementary tools to capture the data from these sensors and created dashboards to visualize the important process indicators.
“We were just scratching the surface and we realized the bigger play was getting connected to all of the available data sources,” he says. “The challenge that we took on was to develop a way to leverage machine learning techniques to make the manufacturing process smarter.”
Viu Insight is currently working with what Maldonado says is a “major player” in automotive manufacturing, and is gradually working with other OEMs on testing and integrating the platform. It even hopes down the road to work with coating applicators outside of the automotive industry.
“We have a customer now who we are looking closely at their data at it relates to downdraft and paint booth conditions,” he says. “It can be challenging to accurately measure downdraft in a paint booth, but we designed and developed an ultrasonic air speed sensor, and we were able to capture very precise measurements both in downdraft and cross draft, and we are starting to produce meaningful correlations between downdraft air speed and the quality of paint system performance from our analysis.”
Maldonado and Stephens say that OEMs are constantly looking at paint shops with a strong focus on continuous improvement. There are so many process variables in paint shop operations that achieving consistent performance from day to day is a major challenge. While all OEMs work hard to achieve a high quality rate first time through (FTT) percentage, incremental improvements may be harder to achieve. They are confident that data analytics, machine learning and AI will make the difference.
They say it can be done based on three key factors: manufacturing process consistency and relentless pursuit of improvements; new technologies in the form of new production materials as well as production processes; and the use of data and advanced analytics to drive performance.
“All three factors will need to progress in coordination in order to be competitive,” Maldonado says. “Fail in one and your plant will be left behind, risking the ability to compete.”
Visit viuinsight.com
Related Content
Masking Solutions Provider CFS Dramatically Expands Capabilities and Capacity
Custom Fabrication & Supplies (CFS) completed a new plant expansion packing 10 times the capacity into twice the space. It dramatically enhances the supplier’s custom capabilities to provide extremely precise and cost-effective masking solutions.
Read MoreHenry Ford Is Still Right When It Comes to Color
Who would have imagined that more than 100 years after his famous statement about any color as long as it’s black would still have relevance of a sort?
Read MoreCoatings Plant Evolves with Market Trends
Expanding its focus from exclusively serving the RV industry, one of this company’s stand-alone coatings plant has successfully extended its services to additional markets.
Read MoreCuring Oven Basics
Simply heating up the substrate does not cure the coating. There are many variables to consider when choosing the best cure oven for your application...
Read MoreRead Next
Education Bringing Cleaning to Machining
Debuting new speakers and cleaning technology content during this half-day workshop co-located with IMTS 2024.
Read MoreEpisode 45: An Interview with Chandler Mancuso, MacDermid Envio Solutions
Chandler Mancuso, technical director with MacDermid Envio discusses updating your wastewater treatment system and implementing materials recycling solutions to increase efficiencies, control costs and reduce environmental impact.
Read MoreA ‘Clean’ Agenda Offers Unique Presentations in Chicago
The 2024 Parts Cleaning Conference, co-located with the International Manufacturing Technology Show, includes presentations by several speakers who are new to the conference and topics that have not been covered in past editions of this event.
Read More