Electrodeposition of Ni-Fe-Mo-W Alloys - Part 8
Eighth Quarterly Report - AESF Research Project #R-117. This NASF-AESF Foundation research project report covers the eighth quarter of project work (October-December 2014).
by
A. Kola and Prof. E.J. Podlaha-Murphy,*
Northeastern University
Boston, Massachusetts, USA
Editor’s Note: This NASF-AESF Foundation research project report covers the eighth quarter of project work (October - December 2014). Progress on the previous quarters has been published in summary in the NASF Report in Products Finishing and in full at www.pfonline.com.** A printable PDF version is available by clicking HERE.
Introduction
The project, initiated in January 2013, addresses the induced codeposition of molybdenum and tungsten alloys with nickel and iron having a focus on developing a toolbox of plating conditions to deposit different combinations of Ni, Fe, Mo and W. This paper covers progress made during the eighth quarter. Work was focused on the effect of the additive 2 butyne-1,4-diol (BD) in an acidic Ni-W electrolyte.
Through NASF-AESF Foundation funding, several students, both graduate and undergraduate, have gained experience in surface finishing research. In this period, Graduate student Avinash Kola has continued work on the influence of deposition conditions on the properties of the Ni-W alloys.
Effect of 2 butyne-1,4-diol (BD) on Ni-W deposition
Nickel-tungsten is a promising alloy that may be of interest to replace the environmentally unfavorable hard chromium coatings, due to the satisfactory appearance of the coating, and the mechanical and anti-corrosion properties.1,2 The corrosion behavior of Ni-W alloys is well documented. For example, Yao, et al.3 found that Ni-W is more corrosion resistant than stainless steel 304 in acidic media. Stepanova and Purovskaya4 investigated the dissolution of different compositions of Ni-W alloys and found that an alloy having a composition of 28 wt% tungsten had the most favorable results. It is also well-known that tungsten cannot be deposited from an aqueous solution and codeposition of tungsten with other elements, such as those of the iron group (i.e., Fe, Ni, Co) permits deposition of tungsten in the alloy.5
Corrosion protection by organic inhibitors is mostly based on the modification of the surface properties of the metal alloy through adsorption of inhibitor molecules and the subsequent formation of a blocking layer.6,7 Acetylenic compounds are known to be strong corrosion inhibitors in acidic solutions, and one such widely examined compound for corrosion inhibition is 2-butyne-1,4-diol (BD).8 The inhibitive effects of BD on mild steel in sulfuric acid were investigated by Hosseini and Arshadi.9 The introduction of BD can lead to the formation of a thin inhibitor film on the steel surface, which effectively protects it from further corrosion. The addition of BD can also reduce the deposit stress,10,11 depending on its concentration, and act as a brightener for nickel alloys.12,13 In addition, it has been shown to improve the corrosion resistance of Ni-W deposits.13,14 However, little understanding is present on the effects of BD on the deposition rates of nickel, tungsten and the side reaction during reduction. In this study, we examine the effect of different concentrations of BD during the electrodeposition of Ni-W alloys, and its influence on the nickel and tungsten deposition behavior using a conventional Hull cell.
The electrolyte used in this study contained 0.1M nickel sulfate, 0.15M sodium tungstate and 0.285M trisodium citrate at a pH of 2 and at room temperature. The BD concentration was varied from 0 to 5 mM. The applied current density was -50 mA/cm2 on a copper plate in a Hull cell configuration for 30 min at an agitation rate of 3 L/min (air). Polarization data was obtained by placing the electrodes parallel to each other, at a scan rate of 10 mV/sec, with a Ag/AgCl reference electrode. The curves were corrected for ohmic drop with impedance spectroscopy. Composition and thickness were measured using x-ray fluorescence.
Figure 1 shows the polarization curves of (a) Ni-W and (b) Ni deposition with varying amounts of BD. A shift of the polarization curves toward more positive potentials was observed in the Ni-W electrolyte as the BD concentration increased. This unusual polarization behavior is opposite to what is expected in a nickel electrolyte during nickel electrodeposition. Srinivasan and Bapu15 showed an inhibiting effect of the total current density with an increase in BD concentration in a nickel-containing electrolyte. In the low pH region, citrate electrolyte presented here when tungsten is removed, Fig. 1(b), the nickel polarization behavior is indeed similar to prior literature reports, with a decrease in the total current density with increasing amounts of BD. Thus, the introduction of tungstate to the electrolyte creates this unusual behavior. In order to investigate the source of the polarization shift in the Ni-W electrolyte, the partial current densities were determined. The partial current densities can help to indicate if the observed increase in the total current density at a given potential with BD is due to an increase in the metal deposition rate or due to an increase in the side reaction. In order to determine the partial current densities of the overall reactions, both composition and mass measurements are needed over a range of current densities.
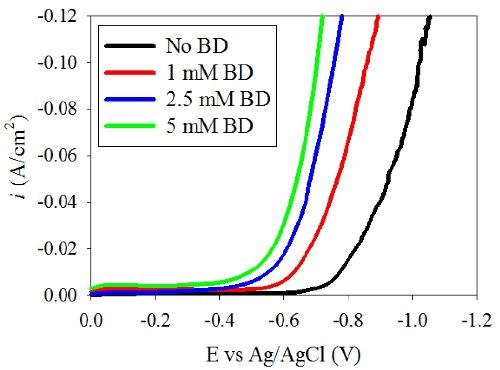
Figure 1(a) - Effect of BD on the polarization behavior of the Ni-W electrolyte.
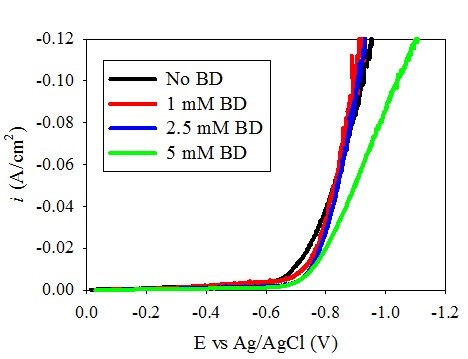
Figure 1(b) - Effect of BD on the polarization behavior of the Ni electrolyte.
Figure 2(a-d) shows images of the Ni-W deposit obtained on the Hull cell with varying concentrations of BD. The deposits without BD appear to be light gray in color with a reflective surface. The deposit appearance tends to increase in brightness at higher current densities with increasing BD concentration. Furthermore, no deposition occurs at lower current densities with increasing BD concentration. At the highest BD concentration examined, [5 mM, Fig. 2(d)], little or no deposit was obtained over a large deposition range. Also, there was an interesting pattern seen in the deposits produced under air agitation. In areas where the air bubbles rose, no deposit was seen. This could indicate that an increase in BD transport to the electrode surface had an inhibiting effect on the alloy deposition.
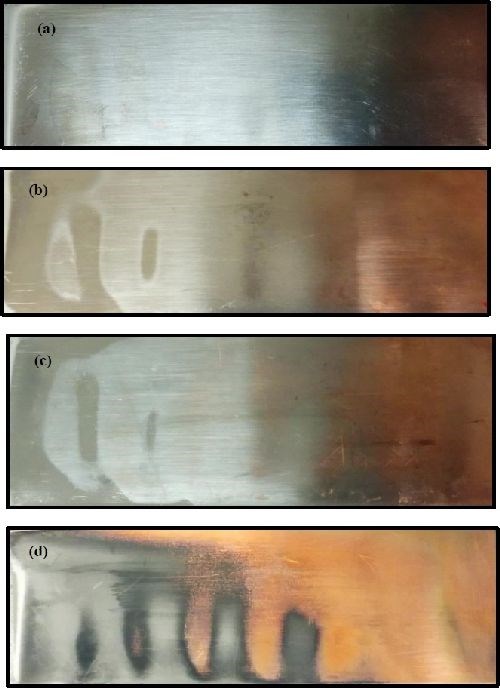
Figure 2 - Photographs of Ni-W deposit with varying amounts of BD at an average current density of -50 mA/cm2: (a) No BD, (b) 1 mM BD, (c) 2.5 mM BD and (d) 5 mM BD.
The deposit composition obtained with XRF along the length of the Hull cell is presented in Fig. 3. In all cases, the alloys are nickel-rich. In Fig. 3(a), an increase in nickel content is observed in the alloys with an increase in the amount of BD present in the electrolyte. The composition in this range is relatively unaffected by the total current density. An inverse behavior is seen in the case of tungsten [Fig. 3(b)], with a subsequent reduction in the amount of tungsten with BD.
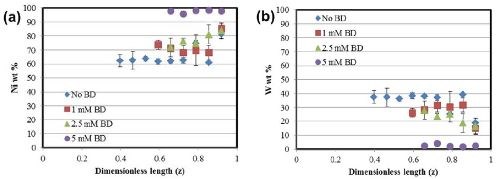
Figure 3 - Alloy composition as a function of cathode length: (a) nickel and (b) tungsten.
In order to estimate the local applied current density along the cathode length, a primary current distribution was assumed (This current distribution is the estimate commonly provided by manufacturers of the Hull cell.). To evaluate the validity of using this approach, the Wagner number was determined at the average current density employed in the Hull cell:
Wa = (∂E/∂i)/(L/κ) (1)
where κ is the conductivity and L is the electrode length. The corresponding Wagner numbers under these conditions are: 0.015 (No BD), 0.0125 (1 mM BD) and 0.0075 (2.5 mM and 5 mM) respectively which are all <<1. Therefore, the total current density distribution along the Hull cell configuration is governed largely by an ohmically controlled resistance, and a primary current distribution is a reasonable approximation of the local current density. The composition data in Fig. 3 then can be translated to show the composition as a function of applied current density, shown in Fig. 4.
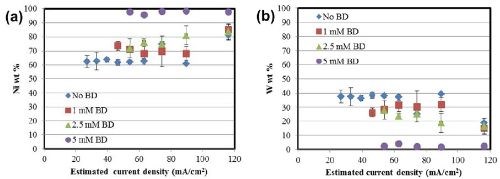
Figure 4 - Alloy composition as a function of current density: (a) nickel and (b) tungsten.
Figure 5 shows the variation in thickness with and without varying concentrations of BD in the electrolyte. The deposit thickness increased with increasing current density in all the examined cases. In the case where BD was introduced into the electrolyte, there was a decrease in the deposit thickness. This can be attributed to an increase in the side reaction.
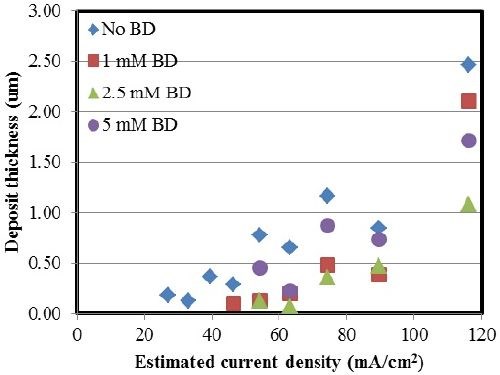
Figure 5 - Ni-W deposit thickness with varying amounts of BD.
In Fig. 6 a comparison is made between the partial current densities for nickel, tungsten and the side reaction with varying concentrations of BD calculated from Faraday’s law. The x-axis in Fig. 6 is the working electrode potential determined by interpolating the potential from the polarization curve in Fig. 1, using the values of the estimated local current density along the length of the Hull cell cathode. From Fig. 6(a), there is a shift in the nickel deposition potential to a more positive value. However, comparably, there is less change of the tungsten partial current density with potential [Fig. 6(b)]. Thus, the shift in the nickel reduction rate is what accounts for more nickel in the deposit. There is also a shift in potential with the side reaction, which is a result of the hydrogen evolution reaction [Fig. 6(c)]. The biggest change in the side reaction is when BD is introduced, but then additional amounts of BD introduce very small effects on the side reaction rate. Thus, the observed thickness decrease with BD present in the electrolyte (Figs. 2 and 5) is due to the increase in the side reaction rate.
The Tafel slopes for each of the reactions were estimated within the potential range of -0.6 and -1.1 V, which is a kinetically-controlled region for nickel and tungsten deposition, and the values are shown in Table 1. While the presence of BD in the electrolyte seems to enhance the nickel deposition kinetics, shifting the deposition to more positive values with increasing concentrations of BD, it does not significantly affect the Tafel slopes.
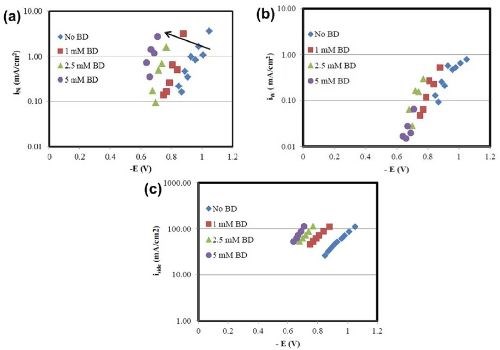
Figure 6 - Effect of BD concentration on (a) nickel, (b) tungsten and (c) side reaction partial current densities.
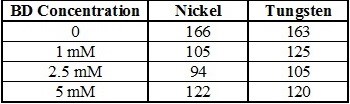
Table 1 - Tafel slopes (mV/dec) of Ni-W alloys with varying concentrations of BD.
Conclusions
An initial assessment of the effect of BD on the deposition behavior of Ni-W alloys was examined using the Hull cell and polarization curves. Together these experiments can be used to assess the partial current densities during deposition. The presence of BD in the electrolyte shifts the nickel deposition potential to more negative potentials, resulting in more nickel deposited into the Ni-W alloy. The presence of BD however, increases the side reaction (hydrogen evolution reaction) which results in lower deposit thickness. While the addition of BD in the electrolyte can result in more corrosion resistant alloys, this study found that it does indeed change the deposit composition and current efficiency.
References
1. K.R. Sriraman, et al., Mater. Sci. Eng. A, 460-461, 39-45 (2007).
2. H. Alimadadi, et al., Materials & Design, 30 (4), 1356-1361 (2009).
3. S. Yao, et al., Corrosion, 52 (3), 183-186 (1996).
4. L. I. Stepanova & O.G. Purovskaya, Met. Finish., 96 (11), 50, 52-53 (1998).
5. A. Brenner, Electrodeposition of Alloys, Vols. I & II, Academic Press, New York, 1963.
6. M.A. Hegazy, M. Abdallah & H. Ahmed, Corrosion Sci., 52 (9), 2897-2904 (2010).
7. A. Popova, et al., Corrosion Sci., 46 (6), 1333-1350 (2004).
8. J. O'M. Bockris & B. Yang, J. Electrochem. Soc., 138 (8), 2237-2252 (1991).
9. M.G. Hosseini & M.R. Arshadi, Int. J. Electrochem. Sci., 4 (9), 1339-1350 (2009).
10. Y. Lui, et al., J. Alloys Compd., 478 (1-2), 750-753 (2009).
11. D. MockutÄ— & O. NivinskienÄ—, Chemija, 3, 218-229 (1998).
12. Y. Wu, et al., Surf. Coat. Technol., 162 (2-3), 269-275 (2003).
13. M. Zheng & R.D. Hilty, ECS Trans., 25 (41), 117-123 (2010).
14. S. Miura, M. Kiguchi & K. Murakoshi, Surf. Sci., 601 (1), 287-291 (2007).
15. R. Srinivasan & G.N.K. Ramesh Bapu, Trans. Inst. Met. Finish., 91 (1) 52-56 (2013).
Presentations [where AESF was acknowledged for support (work from prior reports)]:
1. A. Kola and E.J. Podlaha, “Electrodeposition of Ni-W, Ag-W and Ag-Ni-W Alloys from Citrate-Thiourea Electrolytes,” presented at the 224th Electrochemical Society (ECS) Meeting, (A1) San Francisco, CA, October 2013.
2. M. Silva, A. Alamansure, K. Duarte, A. Kola and E. Podlaha “Plating of NiW, NiMo and NiMoW with and without Fe: Induced Codeposition Mechanism,” presented at SUR/FIN 2014, Cleveland, OH, June 11, 2014.
3. E.J. Podlaha, A. Kola and S. Sun, “NiWAg, NiWMo and NiW Electrodeposition,” presented at SUR/FIN 2013, Chicago, IL, June 12, 2013.
4. S. Sun and E. J. Podlaha, “Examination of Induced Codeposition by Intensity Modulated Photocurrent Spectroscopy (IMPS),” presented at the Gordon Research Conference on Electrodeposition, Biddeford, ME, July 27-31, 2014 (poster).
5. A. Kola and E. J. Podlaha, “A First Investigation of Ag-Ni-W Ternary Alloy Electrodeposition,” presented at the Gordon Research Conference on Electrodeposition, Biddeford, ME, July 27-31, 2014 (poster).
6. S. Sun and E.J. Podlaha, “Examination of NiW Induced Codeposition by Intensity Modulated Photocurrent Spectroscopy (IMPS),” presented at the 225th Electrochemical Society (ECS) Meeting, (E3) Orlando, FL, May 2014.
About the authors:
Avinash Kola is a Ph.D. student in the Department of Chemical Engineering at Northeastern University. He received his M.S in Chemical Engineering at Louisiana Tech University in 2010, and his B.S from Jawaharlal Nehru Technological University, India in 2006.
Footnotes
*Corresponding author:
Prof. E.J. Podlaha-Murphy
Professor of Chemical Engineering
Northeastern University
Boston, Massachusetts 02115
Phone: (617) 373-3796
E-mail: e.podlaha-murphy@neu.edu
**Quarter 1 (January-March 2013): Summary: NASF Report in Products Finishing; NASF Surface Technology White Papers, 78 (1), 11-17 (October 2013); http://short.pfonline.com/NASF13Oct2.
Quarter 2 (April-June 2013): Summary: NASF Report in Products Finishing; NASF Surface Technology White Papers, 78 (2), 18-27 (November 2013); http://short.pfonline.com/NASF13Nov2.
Quarter 3 (July-September 2013): Summary: NASF Report in Products Finishing; NASF Surface Technology White Papers, 78 (4), 11-16 (January 2014); http://short.pfonline.com/NASF14Jan2.
Quarters 4-6 (October 2013 - June 2014): Summary: NASF Report in Products Finishing; NASF Surface Technology White Papers, 79 (2), 1-14 (November 2014); http://short.pfonline.com/NASF14Nov1.
Quarter 7 (July - September 2014): Summary: NASF Report in Products Finishing; NASF Surface Technology White Papers, 79 (7), 1-9 (April 2015); http://short.pfonline.com/NASF15Apr1.
Related Content
NASF/AESF Foundation Research Project #121: Development of a Sustainability Metrics System and a Technical Solution Method for Sustainable Metal Finishing - 15th Quarterly Report
This NASF-AESF Foundation research project report covers the twelfth quarter of project work (October-December 2023) at Wayne State University in Detroit. In this period, our main effort focused on the development of a set of Digital Twins (DTs) using the Physics-Informed Neural Network (PINN) technology with application on parts rinsing simulation.
Read MoreCalculating Applied Media Force During Vibratory Finishing
What appear to be identically set-up vibratory bowls will finish identical loads of parts in varying time cycles. This paper offers a new technique to better predict what the operator will produce, by measuring the force applied to the parts. It is the efficiency of that force which controls the efficiency and speed of the refinement cycle.
Read MoreTin-Zinc Alloy Electroplating and Its Corrosion Behavior
An NASF/AESF Foundation Research Program Retrospective
Read MoreRead Next
A ‘Clean’ Agenda Offers Unique Presentations in Chicago
The 2024 Parts Cleaning Conference, co-located with the International Manufacturing Technology Show, includes presentations by several speakers who are new to the conference and topics that have not been covered in past editions of this event.
Read MoreDelivering Increased Benefits to Greenhouse Films
Baystar's Borstar technology is helping customers deliver better, more reliable production methods to greenhouse agriculture.
Read MoreEpisode 45: An Interview with Chandler Mancuso, MacDermid Envio Solutions
Chandler Mancuso, technical director with MacDermid Envio discusses updating your wastewater treatment system and implementing materials recycling solutions to increase efficiencies, control costs and reduce environmental impact.
Read More