Evaluation of Atmospheric Corrosion on Electroplated Zinc and Zinc-Nickel Coatings by Electrical Resistance (ER) Monitoring
This paper is a peer-reviewed and edited version of a presentation delivered at NASF Sur/Fin 2013 in Rosemont, Ill., on June 12, 2013.
By Per Møller, Technical University of Denmark
Editor's Note: This paper is a peer-reviewed and edited version of a presentation delivered at NASF Sur/Fin 2013 in Rosemont, Ill., on June 12, 2013. A printable PDF version is available by clicking HERE.
ABSTRACT
Electrical resistance (ER) probes provide a measurement of metal loss, measured at any time when a metal is exposed to the real environment. The precise electrical resistance monitoring system can evaluate the corrosion to the level of nanometers, if the conductivity is compensated for temperature and magnetic fields. With this technique, very important information about the durability of a new conversion coating for aluminum, zinc and zinc alloys exposed to unknown atmospheric conditions can be gathered. This is expected to have a major impact on a number of industrial segments, such as test cars for the automotive industry, off-shore construction or components and devices used in harsh industrial environments. The ER monitoring makes it possible to study the corrosion rate online in remote locations as a function of temperature, relative humidity and changes in the composition of the atmosphere. Different coatings of zinc and zinc/nickel, with and without different Cr+3 conversion coatings, were tested in salt spray, and the corrosion rate was recorded every five minutes. In this paper, the results are discussed and compared.
Keywords: Corrosion measurement, electrical resistance monitoring, electrodeposited zinc, electrodeposited zinc-nickel
Introduction to atmospheric corrosion
Atmospheric corrosion of surfaces such as zinc coated steel with and without conversion coatings is normally difficult to evaluate precisely. Generally, the evaluation is carried out as a simple visual inspection during the test and subjective evaluations based upon appearance according to the ASTM D610 standard (or similar standards), which evaluates the appearance as a function of the duration of the corrosion test. However, the appearance is probably not always giving information about the actual corrosion speed.
It is in general difficult to evaluate the corrosion rate of a zinc coated surface exposed to different atmospheres and temperatures. It is even more difficult to study for instance the durability of different conversion coatings on top of the zinc layer. If the test takes place as an in situ test, it is practically impossible to obtain any information about the corrosion speed.
The corrosivities of indoor atmospheres are generally considered to be quite mild when ambient humidity and other corrosive components are under control. Nevertheless, some combinations of conditions may actually cause relatively severe corrosion problems. Even in the absence of any other corrosive agent, the constant condensation of humidity on a cold metallic surface may cause an environment similar to constant immersion for which a component may not have been chosen or prepared.
Normally, equipment used under dry conditions should not suffer from these problems unless there are large temperature fluctuations that result in condensation. Condensation can be accelerated by the presence of contaminants, especially if the contaminants are hygroscopic and adsorb enough moisture to provide a liquid layer on the surface.
The corrosion rate of zinc coatings in a car treated with different conversion coatings can be hard to evaluate in situ. Factors like chloride from deicing, temperature and moisture combined with the time and location of driving will provide numerous variables to complicate the estimate of the corrosion rate.
Classical method of evaluating atmospheric corrosion
In order to accelerate coating development and provide reliable test methods capable of quantifying the performance of coatings with respect to their corrosion resistance, accelerated corrosion test methods need to be developed. Furthermore, such methods need to be so reliable that they can be integrated into the R&D process, providing not only a better, but also a more fundamental understanding of which coating parameters and formulations have a positive impact on the durability of the developed coatings.
The more accelerated and the more reliable the applied test method is, the more favorable the accelerated corrosion test will be, since it is important to keep the required testing time as short as possible. However, the more accelerated the test method is, the less representative of the real world the test method will be, since it will involve test conditions far from actual environmental conditions. Thus, the more accelerated the test will be, the more severe the corrosion process will need to be, and the more unrealistic the test method will become. This is indeed a paradox, since an accelerated test will never be identical to long-term weathering. Nevertheless, it is important to perform accelerated tests that can simulate real, naturally occurring corrosion processes as accurately as possible. One of the more important effects to take into account is that the corrosion mechanism might totally change when altering the corrosion conditions.
A classic example of this is that it is easy to believe that an accelerated corrosion test can be performed by simply increasing the concentration of one of the corrosion-accelerating species such as chlorides. However, in many cases, an increase in the chloride concentration might actually change the stability of a surface, and thereby significantly decrease the thickness of a protective layer by changing the thermodynamically stable area for the involved compounds.1
The aggressiveness of the atmospheric corrosivity has resulted in the development of so-called corrosion classes. These corrosion classes are summarized in Table 1, which outlines the five corrosion classes in detail.
Table 1 - Overview of the five corrosion classes according to the classification provided in ISO 12944 Part.
The ISO 9323 standard is well-known within the field of corrosion classes. The standard is based on atmospheric corrosivity for specific locations derived from meteorological data such as time of wetness (i.e., the time where the relative humidity is above 80 percent), different pollution categories (i.e., sulfur dioxide and the concentration of airborne chlorides measured as a deposition rate in mg/m2/day).
The standard was not intended to be used in connection with extreme atmospheres such as those encountered in chemical plants or used in accelerated test methods such as salt sprays. It was not intended to be used to evaluate the corrosion rate in harsh environments such as those encountered by automobiles driving in areas where deicing is used, or locations where additional factors make the corrosion evaluation complicated. This includes industrial areas with the high impact of SO2 and off-shore construction where chlorides may have very high impact, especially in places where the chloride can build up on surfaces and immobilize moisture. This is the case for salts such as MgCl2 and CaCl2.
In Table 2, the corrosion rate (CR) in g/m2/year for short-term corrosion is indicated for four different materials exposed to the five different corrosion classes defined in ISO 9323. The calculations are made assuming uniform corrosion.
Table 2 - The corrosion rate measured in g/m2/year for steel, copper, aluminum and zinc for five different corrosion classes according to ISO 9323.
In Table 2, it is interesting to note the relatively high corrosion rate for steel compared to zinc and aluminum, which are known to be less noble. Furthermore, the most noble metal, copper, corrodes at nearly the same corrosion rate as zinc. It is even more surprising that the least noble metal, aluminum, shows the lowest corrosion rate of all, even under the most severe corrosion conditions in corrosion class C5.
This type of observation can be explained to some degree from studying the thermodynamic behavior of the corrosion products formed during the selected test. Figure 1 shows the multi-element Pourbaix digrams calculated for zinc and other selected elements. In the Zn-Cl-H2O system, it is shown that zinc forms a ZnCl+ species. Chloride ions complex zinc ions and speed up the corrosion kinetics, but do not change the stability. If a zinc surface comes in contact with CO2 in the atmosphere, a "natural" conversion coating consisting of the mineral hydrozincite, Zn5(OH)6(CO3)2, is formed.
Figure 1 - Multi-element Pourbaix diagrams calculated for zinc under three different environmental conditions: (a) Zn-H2O, (b) Zn-Cl-H2O and (c) Zn-C-Cl-H2O. The green shaded area indicates the immune area and the red shaded area indicates the passive area in the diagram. Diagram (c) explains why the corrosion speed of zinc and zinc coatings during atmospheric corrosion is low, according to the data given in Table 2.
Three main components can often be identified among the corrosion products, namely zinc oxide (ZnO), hydrozincite (Zn5(OH)6(CO3)2 and simonkolleite (Zn5(OH)8Cl2•H2O), if chloride is a part of the elements found in the environment and the concentration of the elected elements are high enough.2 In the present case where all tests are carried out in a salt spray according to ASTM B117, chlorides seem to play an important role, and will probably form ZnCl2 compounds such as simonkolleite.
It is known that ZnCl2 is very hygroscopic. From a thermodynamic point of view, it can be shown that zinc forms chloro-complexes such as ZnCl+ ions (Fig. 1) during exposure to salt spray.
Temperature and relative humidity (RH) are easily determined corrosivity factors. Not so easily determined is the time of wetness (TOW) in combination with the surface contamination by corrosive agents. The most important factor in atmospheric corrosion, though, is by far moisture, either in the form of rain, dew, condensation or high RH. In the absence of moisture, most contaminants would have little or no corrosive effect.
How can atmospheric corrosion be evaluated?
Even the ISO 9323 describes and predicts corrosion under well controlled “laboratory” conditions. As discussed above, it is very complicated to evaluate corrosion in situ. Consider a zinc surface treated with different new conversion coatings and placed in remote off-shore construction, in a chemical production plant or in the engine compartment of an automobile, where temperature, relative humidity and chloride contamination is a function of both local and geographical conditions as well as the running conditions of the vehicle.
By using electrical resistance (ER) probes, which are very sensitive, it is possible to follow the corrosion rate continuously online hour-by-hour and nanometer-by-nanometer. At the same time, humidity and temperature sensors can measure RH (relative humidity) and temperature and a unique relationship between corrosion and varying conditions can be recorded for later evaluation. A GPS system can be used for establishing the geographical position of the vehicle, and it is then possible to obtain very valuable information about the corrosion impact in a way that no previous method has allowed. The data can be recorded or transmitted continuously via wireless systems for servers that can quickly register unexpected deviations, providing an immediate opportunity to register additional events. During the last year a new ER probe system with high precision and sensitivity has been introduced to the market, which has already been adopted by the gas, oil and power plant industries for evaluation of corrosion.
Many ER techniques are available but only a few are precise enough to measure the corrosion of zinc coatings and compare their durability, for instance in cars and off-shore structures on the ocean. Such a high sensitivity sensor is described in US Patent 7,541,817 and may be able to compensate temperature and variation in the magnetic field to overcome magnetoresistive phenomena, caused by small changes in the magnetic field.
In the future such types of corrosion monitoring will be an important factor in the development of new coatings for special applications, and will probably eliminate the use of accelerated tests in the field of R&D. In a few weeks’ time, such probes will be able to indicate the corrosion rate in a special location under special conditions, and different coatings can be compared under exactly the same conditions. The corrosion probes can also be installed in more expensive equipment like large electronic equipment and are already used as corrosion guards, to ensure that the conditions for warranty obligations are met.
In the following study, the corrosion rate of pure iron was compared with that of zinc and zinc-nickel coated steel with and without a conversion coating to compare the behavior of the coatings in a neutral salt spray according to ASTM B117. Nonetheless, the tests could also have been carried out in the engine room of a car or at an oil drilling platform in the ocean.
Test samples: St37 uncoated
St37 with Zn
St37 with Zn (passivation Cr+3)
St37 with ZnNi
St37 with ZnNi (passivation Cr+3)
Description of the ER (Electrical Resistance) sensor
ER sensor design
The corrosion equipment consists of probes, loggers, cables and software (Fig. 2). While loggers, cables and software are well-established, thoroughly tested equipment, the probes are new prototypes made specifically for the investigation of zinc corrosion. The corrosion of the coupon is determined by computing the change in thickness as a function of electrical resistance. When the conductor corrodes, the cross-sectional area is reduced, leading to an increase in the resistivity. This can be measured quite accurately, making it possible to measure the corrosion rate nanometer-by-nanometer and minute-by-minute if necessary. The coupon-conductor is made from a material similar to the subject material and is exposed to the same environment as the subject material to be evaluated. Hence the corrosion of the coupon represents the corrosion of the subject material. A shielded but similar conductor is used as a non-corroded reference.
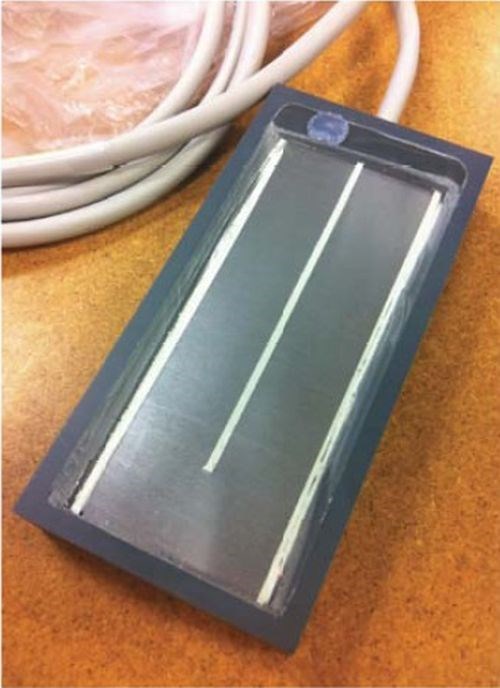
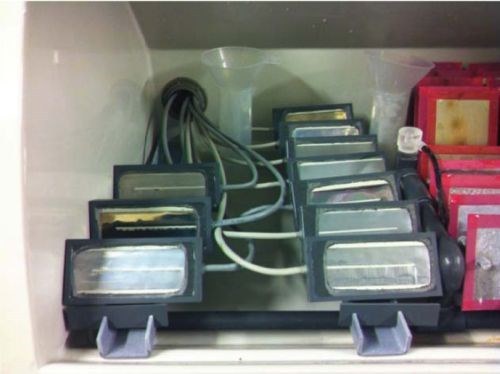
Figure 2 - Probes (L) before and (R) during testing in the salt spray chamber according to ASTM B117.
Theory of resistivity
For a given conductor material, it is given that the resistance R is directly proportional to the length l and inversely proportional to the cross-sectional area A:
(1)
where ƍ is the resistivity, which is characteristic for the material concerned. The SI unit is Ω•m, but in practice is often used μΩ•m or nΩ•m. The resistivity is temperature dependent:
(2)
where
ƍ0 is the resistivity at temperature T0 - room temperature; T = 20°C,
αt is the temperature coefficient at the temperature T and
T is the actual temperature.
Values of ƍ and α for different conductor and resistance materials can be found in various tables in the literature. Calculation of the temperature coefficient αt °C is done as follows:
(3)
where
α0 is the temperature coefficient at temperature T0 and
T0 is again room temperature; T = 20°C.
Conductor materials often have a slightly higher resistivity than calculated. This may be due to impurities in the material or stress as a result of mechanical processing. If the conductor leads AC current, there may even appear an (apparent) increase in resistance caused by current displacement phenomena and - in cables - eddy current losses in the cable sheath.
Computation of coupon thickness
Since the steel foils have been plated, there are two metallic layers with different characteristics. Thus, the base and the coating must be treated as parallel-connected resistors:
(4)
and therefore, the change in the total thickness can be computed as follows:
(5)
where w is the width of the conductor.
Corrosion measured by the ER (Electrical Resistance) sensor
Figure 3 shows the recorded decrease in thickness vs. time for the tested probes of uncoated iron, zinc and zinc-nickel coatings with and without passivating layers. All passivated coatings were carried out in a trivalent chromating process. All samples with the exception of zinc were carried out in duplicate. It is of interest to notice the role of the conversion coating on both the zinc-nickel alloy coating (15-16% Ni) and the zinc coating.
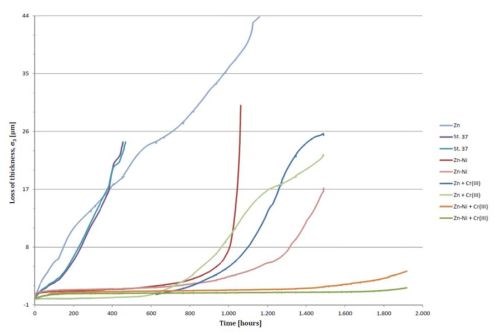
Figure 3 - Recorded decrease in thickness vs. time for the tested probes of uncoated iron, zinc and zinc-nickel coatings with and without passivating layers.
The uncoated mild steel corrodes easily in salt spray. The steel basis material tends to be highly reactive because of its natural tendency to form iron oxide. When it does resist corrosion to some degree, it is due to the formation of a film of protective iron oxide Fe2O3 (“red rust”) on its surface by reaction with oxygen and water. This film can slow down the corrosion to some degree but the corrosion rate is still very high. It appears that the material corrodes at the same rate during the first 400 hr. The uncoated iron probes were removed from the salt spray at this point because they were heavily attacked. The corrosion rate was calculated to be about 63 nm/hr. The unpassivated zinc surface seemed to be more corrosion resistant than the steel. It provided good cathodic protection of the steel, but still corroded at a high rate. The corrosion rate of an electroplated zinc surface was estimated to be 40 nm/hr.
A zinc-nickel coated steel surface exhibited a very low corrosion rate of 4.0 nm/hr during the first 700-800 hr of testing, even without a passivating layer. After 800-1,000 hr, the corrosion speed increased rapidly. It was assumed that that the selective corrosion of zinc from the zinc-nickel alloy enriched the surface with nickel, which, because of the formation of a Raney nickel-like structure, formed a very effective cathode for the reduction of oxygen, which again sped up the selective corrosion of zinc or the dezincification of the alloy.
Figure 3 shows that the introduction of a Cr+3-based passivating surface on top of the zinc coating significantly reduced the corrosion. It seems as if the passivating layer on top of the zinc/nickel alloy coating eliminated the corrosion during the first 1,400-1,600 hr.
Figure 4 shows the Pourbaix diagram for chromium showing the immune area of zinc, in green shading. Cr(OH)3 was selected as the species for the calculation of this area. During the passivation treatment in the Cr+3 conversion bath, the cathode reaction (hydrogen reduction) increased the pH at the surface, and a coating consisting of Cr(OH)3 and ZnO was formed (see reaction equations below). The coating inhibited the oxygen reduction at the active cathode site, when the coating was further exposed to atmospheric corrosion.
Zn + H+ + H2O Zn+2 + H2(g) + OH‾ ; ∆G = -67.893 kJ at 20°C (6)
The formation of hydroxide initiates the following precipitation reaction of chromium (III) hydroxide, according to the Pourbaix diagram in Fig. 4.
Cr+3 + OH‾ CrOH+2
CrOH+2 + OH‾ CrO+ + H2O
CrO+ + OH‾ + H2O Cr(OH)3 (7)
The overall reaction according to the precipitation of chromium hydroxide is:
Cr+3 + 3OH‾ = Cr(OH)3, showing a Gibbs free energy ∆G = -166.449 kJ (8)
and Zn-hydroxide precipitation according to the Pourbaix diagrams present in Figs. 1a and 1b:
Zn+2 + OH‾ ZnOH+; ZnOH+ + OH‾ = Zn(OH)2 (9)
The overall reaction according to the precipitation of zinc hydroxide is:
Zn+2 + OH‾ = ZnO + H2O; ∆G = -90.712 kJ at 20°C (10)
Based on the thermodynamic calculations for all reactions, the reaction seems energetically possible and a complex but dense conversion coating consisting of Cr+3 and Zn+2 compounds will be formed, giving the zinc basis material optimal corrosion protection with high durability under near neutral pH conditions.
The passivating effect of Cr+3 conversion coatings are widely used for passivation, as they generally improve the resistance of zinc to atmospheric corrosion. According to Fig. 3, the corrosion rate of passivated zinc is less than 1.0 nm/hr for the first 600-700 hr. An explanation can be found by taking the thermodynamic conditions into consideration (Fig. 4).
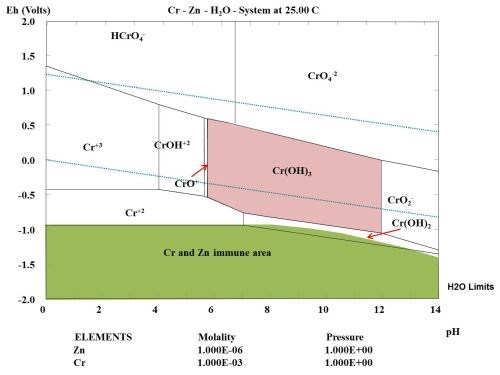
Figure 4 - Pourbaix diagram for chromium calculated showing the immune area of zinc (in green shading).
During the passivation of a zinc layer with Cr+3 ions and some suitable oxidation agents, a Cr(OH)3 layer is formed on the active cathode sites, where the Cr(OH)3 will precipitate during the conversion bath treatment caused by a change in pH. After the treatment, the active cathodes will be inhibited during an exposure of the treated zinc coating to atmospheric corrosion. If the zinc coating is exposed to an acidic atmosphere the thermodynamic calculations indicate that Cr(OH)3 will not be stable below pH 6.0, based upon the selected concentration of chromium in the multi-element diagram.
References
1. P. Møller and L.P. Nielsen, Advanced Surface Technology: A Holistic View on the Extensive and Intertwined World of Applied Surface Engineering, Chapter 36; ISBN 978-87 - 92765-17-18; http://astbook.com/, 2013.
2. F. Zhu, et al., Corrosion, 56 (12), 1256 (2000).
Related Content
Material Database Enables Coating Thickness Measurement Without Calibration
The database from Coatmaster AG has calibrations of over 400 different RAL colors.
Read MoreCalculating Applied Media Force During Vibratory Finishing
What appear to be identically set-up vibratory bowls will finish identical loads of parts in varying time cycles. This paper offers a new technique to better predict what the operator will produce, by measuring the force applied to the parts. It is the efficiency of that force which controls the efficiency and speed of the refinement cycle.
Read MoreRead Next
Delivering Increased Benefits to Greenhouse Films
Baystar's Borstar technology is helping customers deliver better, more reliable production methods to greenhouse agriculture.
Read MoreEducation Bringing Cleaning to Machining
Debuting new speakers and cleaning technology content during this half-day workshop co-located with IMTS 2024.
Read MoreA ‘Clean’ Agenda Offers Unique Presentations in Chicago
The 2024 Parts Cleaning Conference, co-located with the International Manufacturing Technology Show, includes presentations by several speakers who are new to the conference and topics that have not been covered in past editions of this event.
Read More