More to Masking
How finding the right masking solution impacts your finishing operation.
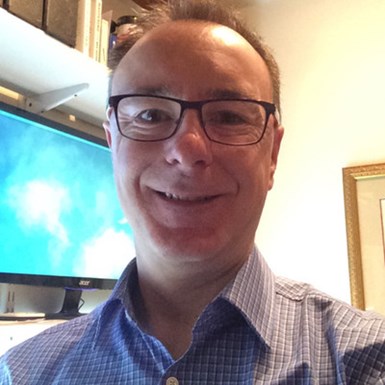
John Gill is the international sales engineer at Caplugs. Visit caplugs.com.
Photo Credit: Caplugs
Simplicity is the key to successfully streamlining production processes, no matter what product is being manufactured. Reducing complex steps in favor of straightforward solutions leads to greater consistency and higher quality end results. This is equally true in masking operations, though in many cases, the simplest and most effective solution may be passed over in favor of what may initially appear to be the most economical option based on upfront costs.
Cost cutting or cost increasing?
Many times, a manufacturer may choose to use imperfectly fitting solutions or manually hand tape any areas that need to be protected during the finishing process. When looking at initial part and material costs, this seems like the most effective choice. However, labor and failure factors can actually make this option more costly.
Adapting imperfect parts or taking time to manually tape parts by hand can lead to significant manual labor and time to complete, meaning a higher employee cost for masking preparation and removal work. Depending on the complexity of the masking work, taping by hand may also require several elaborate steps — like cutting and trimming to size — that can be difficult to consistently replicate. In turn, labor costs and lead times can rise, quality and consistency can be compromised, failure rates and reworking costs can increase and soon, the “cheap” solution suddenly becomes a costly one.
Stepping up standards and production
By working with a reputable masking partner, customers can find a wide range of catalog caps, plugs and die-cuts to suit most standard masking applications. Caps are often available in an array of standard sizes to cover studs, tube ends and other protrusions, while plugs are optimal for protecting plain or threaded, through or blind holes. Die-cuts are also extremely effective for any flat masking surface, as they can be quickly applied and cleanly removed without leaving behind any adhesive residue. They are also often available in common shapes to easily mask barcodes, serial numbers or other standard features and streamline the masking process.
Many standard masking products are also available with specialized material features, such as temperature- and abrasion-resistant materials that can withstand harsher finishing processes. You may also find parts with convenient features like ventilation, pull tabs or a tapered design that can not only provide a more secure or exact fit, but also reduce removal or installation times to further expedite masking work. Compared with standard rolls of tape, these parts may cost more upfront, but with the significant savings they can bring through reduced labor expenses, decreased lead times and less waste and loss, switching to masking parts can result in substantial overall savings.
The best solution? Customize it
Naturally, not every standard masking part will be the right solution for every product line. Products with uncommon shapes, contours or fittings may require a modified standard part or a completely custom design for full coverage. While it can be tempting to adapt an existing part to simply get to a closer-to-exact solution, this can still leave operators with a need to perform “last mile” masking work to complete the solution — reducing time, but still requiring additional labor and leaving open the possibility of masking failures or errors. A custom solution can be tailored for your specific work, and can be further improved with additional features to offer added convenience.
When working with a molding partner, customers can explore different options that not only deliver a custom solution, but one that offers added convenience, new capabilities or features that streamline the workflow. For example, if masking is done on a part for electronics, using conductive or static dissipative materials in the custom part may be required. Other features like ventilation or pre-cut holes can make masking work better for your specific application, while other options like magnetic masking or pull tabs can be used to make application and removal a faster and easier process for operators.
Is custom an affordable option?
Custom masking is generally a simple, straightforward process. First, the specific requirements for your operation or part must be clearly defined with your supplier. This will include understanding the part, the masking work that is being performed and any other special considerations that need to be accounted for in the design. With this information, an engineer can understand your needed volume and material considerations, and offer a better idea of the expected costs and production times needed to determine what kind of savings to expect. You can even get a general idea of what kind of cost benefit that custom masking offers with tools like Caplugs’ custom masking calculator, available online (smartermasking.com/calculator.php).
After this review and approval, the supplier will create a design or develop a prototype part to test the fit and ensure that the custom part meets all the user’s requirements. Once the design is confirmed, manufacturing can begin, and the operator can soon begin to enjoy the cost savings.
Work with a partner to find the right solution
Whether an off-the-shelf solution or a custom-designed part, working with a trusted masking partner can help you determine the best option for your specific masking application. Depending on the complexity of your needs, working with masking experts can help you review standard, modified or custom options and assess what is best for your operations. Drawing on a wealth of knowledge from working with hundreds or thousands of customers and unique designs, let them put their experience to work for you and help find new savings to reduce costs, streamline masking operations and deliver more consistency and quality in your finished parts.
Related Content
Prevent Plating Problems with Critical Inspections
Tanks and their contents should be regularly inspected visually and analytically. When a quality issue arises, it is important to quickly pinpoint where the main problem is by checking which parameter is out of line.
Read MoreTroubleshooting Alkaline Zinc
One of the most common problems that can arise when plating with alkaline zinc is an imbalance of brightener in the solution. In this helpful Ask the Expert article, Chad Murphy of Columbia Chemical discusses how different zinc metal concentrations and brightener concentrations can impact efficiency.
Read MoreLiquid Chrome Vs. Chromic Acid Flake
Contemplating how to continue offering chromic acid services in an increasingly stringent regulatory world? Liquid chrome products may be the solution you’re looking for.
Read MoreMasking Solutions for Medical Applications
According to Custom Fabricating and Supplies, a cleanroom is ideal for converting, die cutting, laminating, slitting, packaging and assembly of medical-grade products.
Read MoreRead Next
A ‘Clean’ Agenda Offers Unique Presentations in Chicago
The 2024 Parts Cleaning Conference, co-located with the International Manufacturing Technology Show, includes presentations by several speakers who are new to the conference and topics that have not been covered in past editions of this event.
Read MoreDelivering Increased Benefits to Greenhouse Films
Baystar's Borstar technology is helping customers deliver better, more reliable production methods to greenhouse agriculture.
Read MoreEducation Bringing Cleaning to Machining
Debuting new speakers and cleaning technology content during this half-day workshop co-located with IMTS 2024.
Read More