Optimizing Your Liquid Electrostatic System
For your electrostatic process to work consistently, there are three primary items to check: voltage at the applicator, part grounding, and compatibility of the coating material. John Owed of Carlisle Fluid Technologies walks you through the process.
Q: We have been operating an automatic liquid electrostatic system for several years and recently have noticed that we need to increase the fluid flow rate to maintain dry film thickness. Overall, we are running about 8-12% higher than when the system was first installed. Our system consists of reciprocating rotary bells coating horizontally oriented aluminum extrusions. How can we optimize efficiency?
A. For your electrostatic process to work consistently, there are three primary items to check: voltage at the applicator, part grounding and compatibility of the coating material. Beyond this, other factors, such as target distance and spray booth conditions, can also impact the efficiency of your application. Let’s review each and discuss how to test for optimal performance.
Applicator voltage: With electrostatic applicators, you must ensure voltage at the applicator. Generally, rotary atomizers (bells) utilize a direct charge process, and the bell cup is at voltage potential. As the coating material exits from the edge of the bell cup, it is electrostatically charged and seeks a ground image. A high-voltage test probe can measure the actual voltage level at the applicator.
Before testing:
- Ensure the voltage is shut off and flush the applicator out with the recommended cleaning solvent.
- Once the lines are flushed, use air to remove any residual solvent and ensure the fluid lines are clean and dry.
- Using a high-voltage test meter/kit, follow the manufacturer’s instructions and test the applicator. This will consist of grounding the test meter, setting it to the appropriate mode, and touching the probe to the applicator’s bell cup (not spinning) with voltage on.
The meter should read within 10% of the applicator set point at the [power supply (if it is a 90Kv applicator, you should read around 80 - 90Kv).
If the voltage is not within 10% of the set point, you need to inspect the various components to isolate where the deficiency is. The most common problem area will be a high-voltage cable that is damaged or not properly seated. If it is a cascade type power supply, the cascade may be degrading. If multiple applicators are used, you should chart the voltage at each and ensure all are within 10% of each other. Multiple applicators also provide an opportunity to swap out components to isolate issues.
Applicator cleanliness should also be evaluated. If the exterior of the applicator is contaminated, this can cause a loss of voltage/efficiency. Electrostatic applicators should always be cleaned with non-conductive solvents.
Part grounding: According to NFPA 33 (Nation Fire Protection Association) Chapter 12, the resistance between the object being sprayed and true earth ground must be 1.0 MΩ (Mega-Ohm) or less. This provides suitable electrostatic attraction and permits the charge from the applicator to dissipate safely. This level of grounding applies to all objects in the spray booth, including the operator.
Ground should be tested with a Meg-Ohm meter (often called a “megger”). A Meg-Ohm meter has an output of 500 – 1,000 volts. This is required to overcome contact resistance through the various attachment points. If a standard VOM (Volt Ohm Meter) is used, inaccurate readings may be obtained. In most finishing systems, the workpiece is hung from a conveyor using load bars and hooks. It is important to ensure that the contact points are clean and that good ground contact can be made through the various attachment points.
Material resistivity: When using electrostatic application equipment, the resistivity of the coating material should be tested to ensure that it is within an acceptable range for the specific manufacturer’s equipment. Generally, the recommended range for resistance is 0.1 MΩ or higher. The primary concern is that the material is not so conductive (very low resistances) that the voltage applied at the applicator follows the fluid column to the grounded fluid supply. When and if this happens, the system current will increase, and the level of voltage at the applicator will be degraded.
In your case, you mentioned that you have had a decrease in efficiency over time, so coating resistivity would only be a potential cause if you have changed your coating material formulation or switched suppliers entirely.
To test the resistivity of the coating material, you need a meter and resistivity probe. The probe is connected to the meter and then inserted to the designed depth into the coating material. The reading is then recorded. As noted above, typically, the resistivity should be 0.1 MΩ or higher.
Other than the Meg-Ohm meter, the high voltage probe and paint resistivity meter are somewhat specialized, so you will need to work through a coating equipment supplier to source. This equipment allows you to troubleshoot and benchmark your settings over time to detect when your process starts to drift.
About the Author
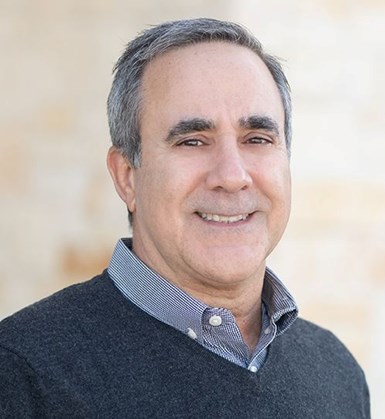
John Owed
John Owed is the finishing SBU director at Carlisle Fluid Technologies. Visit carlisleft.com.
Related Content
Products Finishing Reveals 2024 Qualifying Top Shops
PF reveals the qualifying shops in its annual Top Shops Benchmarking Survey — a program designed to offer shops insights into their overall performance in the industry.
Read MoreFinishing Systems Provider Celebrates 150 Years, Looks to Future
From humble beginnings as an Indiana-based tin shop, Koch Finishing Systems has evolved into one of the most trusted finishing equipment providers in the industry.
Read MoreIntumescent Coating Provides Up to 3 Hours of Fire Protection
PPG Steelguard 951 coating is designed to provide protection against fire and corrosion.
Read MoreTTX’s Automated Conveyor Carrier System Offers Wireless, Flexible Operation
ACC system designed for reliable, consistent point-to-point movement of everything from small to heavy parts.
Read MoreRead Next
A ‘Clean’ Agenda Offers Unique Presentations in Chicago
The 2024 Parts Cleaning Conference, co-located with the International Manufacturing Technology Show, includes presentations by several speakers who are new to the conference and topics that have not been covered in past editions of this event.
Read MoreDelivering Increased Benefits to Greenhouse Films
Baystar's Borstar technology is helping customers deliver better, more reliable production methods to greenhouse agriculture.
Read MoreEpisode 45: An Interview with Chandler Mancuso, MacDermid Envio Solutions
Chandler Mancuso, technical director with MacDermid Envio discusses updating your wastewater treatment system and implementing materials recycling solutions to increase efficiencies, control costs and reduce environmental impact.
Read More