Regenerating Aqueous Cleaning Solution Could Save Time and Cost
Hubbard-Hall has developed an emulsifying cleaner that is optimized for filtration. In conjunction with its membrane filter, the solution enables users to regenerate cleaning solution.
Parts cleaning systems work by transferring soil into the cleaning solution. Those solutions have a finite capacity so they must be replaced periodically. That process can be costly and disruptive but, until now, the alternative of regenerating the cleaning solution through filtration was difficult to achieve on a reliable, cost-effective basis.
An emulsifying cleaner developed by Hubbard-Hall (Waterbury, Conn.) addresses this problem with a formulation paired with proprietary membrane filtration technology. This match of cleaner characteristics to filter design offers parts cleaners a way to reduce downtime, improve efficiency and lower costs.
Aqueous cleaning fundamentals
Finishing processes, such as plating, galvanizing, painting and coating, demand clean surfaces, as do customers and end users. To achieve this, industrial parts cleaning systems are incorporated into manufacturing processes. These systems are engineered to remove soil present on incoming materials or added at previous manufacturing operations. That soil includes drawing compounds, buffing compounds, machining oils, corrosion-preventatives and even fingerprints.
Two types of cleaning are used in manufacturing: immersion (rack or barrel) and impingement (spray). Both combine a cleaning solution with agitation, and usually heat, to remove soil from the part surface.
Cleaning solutions use a combination of solubilization, wetting, emulsification and saponification to draw soil away from where it’s attached.
In solubilization, a cleaning agent dissolves the soil. An example is using an acid to dissolve rust on steel.
Wetting uses differences in surface tension to pull soil into solution from the surface.
Used when soil won’t dissolve, emulsification is where a surfactant or emulsifying agent with hydrophobic and hydrophilic elements pulls soil from the surface. Surfactants are characterized by their hydrophilic-lipophilic balance (HLB), which defines their relative attraction to oil and water. A high HLB value signifies a greater tendency towards solubilization while a low value indicates more emulsification.
Saponification is a chemical process where fatty acids, such as lard oil on stamped steel, are reacted with an alkali to form soap. Being water-soluble, this makes the soil easier to remove.
With both emulsification and saponification, the soil stays in the bath. Over days or weeks, the solution becomes saturated and less effective, increasing the risk of re-soiling parts as they move through. When this happens, the only option is to dump the bath.
Non-emulsifying cleaners avoid this problem by using oil splitters — coalescers or skimmers — to remove the oil. However, these cleaners don’t remove all soil types. Furthermore, some soils show a tendency to emulsify without help from the solution.
Filtering soil from emulsifying cleaners
A good filter must be able to withstand high temperatures, pH values ranging from highly acidic to strongly alkali and thermal shock. It should be durable so as to minimize replacement frequency, and must have pores sized to remove oil but not surfactant.
Three types of filter are used with emulsifying cleaners. These are:
- Ultrafiltration membrane-style filters
- Polymeric filters
- Ceramic filters
Each type has its own advantages and drawbacks. Ultrafiltration, as used in reverse osmosis, works via molecular weight rejection. This has the downside of stripping out surfactants from the cleaner, which renders it ineffective.
Polymeric filters have limited capabilities in the necessary pH and temperature ranges. They are also easily damaged, can’t be back-pulsed and need frequent replacement. Ceramic filters handle a wider range of pH and temperature and can be back-pulsed but are fragile and susceptible to thermal stress cracking.
Innovative filtration technology
Hubbard-Hall’s addition to filtration technology is a combination stainless steel and metal oxide membrane (MOM) filter. Coating 316 stainless with MOM results in a filter with controlled pore size. It withstands temperatures over 200° F and pH values from 0 to 14. It’s durable, can be back-pulsed and is cleaned rather than replaced.

The match of cleaner characteristics to filter design offers parts cleaners a way to regenerate aqueous cleaning solutions.
As dirty cleaner is pumped over the membrane, two things happen. First, the cleaning solution is cleaned by passing through the pores while the larger, emulsified oil molecules are rejected. Second, the membrane breaks the emulsion between cleaner and oil, allowing more of the cleaner to be recovered.
Improved filtration is only part of the answer to improved bath remediation. The other component is a cleaner formulated to work with the stainless MOM filter.
Breaking the emulsion requires precise control over HLB value, cloud point (the water solubility of the surfactant at temperature), electrical charge and micelle formation. Aquaease-Infinity from Hubbard Hall has all these properties.
Aquaease is designed to allow cleaned to flow continuously from the parts-washing tank to a separate process tank without the need to stop the cleaning line. From here, it is pumped into the membrane filter. Reject (the soil) is returned to the process tank while regenerated cleaner goes back into the wash tank.
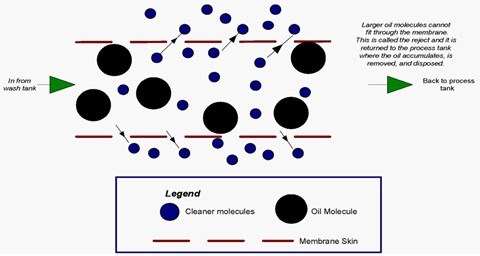
With Aquaease, the soil is returned to the process tank while regenerated cleaner goes back into the wash tank.
Benefits of this system include extending cleaning solution life by three to four times. By reducing the frequency of bath remediation, it also reduces downtime, halves consumption of cleaning solution and saves on energy and water. Re-soil rejects and problems at downstream operations (or the customer) are eliminated and there’s less waste to dispose of or treat.
A typical large cleaning line might consume $100,000 worth of cleaner per year. Dragout typically accounts for 35% of the loss. Of the other 65%, with Aquaease allows 95% to be recovered. This could cut annual expenditure on cleaner by up to $62,000. Reduced downtime and lower hazardous waste disposal costs may also contribute to savings.
Less downtime, more run time
Emulsification and saponification cleaning processes are essential in many industries and businesses, but they create cost and complexity for management. Switching to an aqueous cleaner that’s optimized to work with new filtration technology extends the time between cleaner replacement. That results in higher operational efficiency and lower costs.
Related Content
Solvent Versus Aqueous: Busting the Myths
Is aqueous cleaning “greener” than solvent cleaning? Is solvent a more effective cleaner than aqueous? These and many other questions are answered here to debunk the misconceptions that many manufacturers have held onto for years.
Read MoreTesting Safe Alternative Conversion Coatings
A joint test protocol was developed by a hex chrome-free consortium to best evaluate the most recent commercially available alternative conversion coatings. This article reveals the findings.
Read MorePretreatment of Black Oxide
Having issues achieving a consistent color with the application of black oxide? Start by looking at your pretreatment. Connor Callais of Hubbard-Hall offers advice for troubleshooting your black oxide process.
Read More3-Stage Versus 5-Stage Washers
Columnist Rodger Talbert explains the difference between a five-stage washer and a three-stage washer, and how one provides better corrosion protection over the other.
Read MoreRead Next
A ‘Clean’ Agenda Offers Unique Presentations in Chicago
The 2024 Parts Cleaning Conference, co-located with the International Manufacturing Technology Show, includes presentations by several speakers who are new to the conference and topics that have not been covered in past editions of this event.
Read MoreEpisode 45: An Interview with Chandler Mancuso, MacDermid Envio Solutions
Chandler Mancuso, technical director with MacDermid Envio discusses updating your wastewater treatment system and implementing materials recycling solutions to increase efficiencies, control costs and reduce environmental impact.
Read MoreEducation Bringing Cleaning to Machining
Debuting new speakers and cleaning technology content during this half-day workshop co-located with IMTS 2024.
Read More