Silane-based Multimetal Pretreatments for Powder Painting
When looking to switch from phosphate conversion coatings, Stewart Tymchuk from Dynamix suggests looking at silane-based products for powder coating pretreatments.
Q: We are considering switching from phosphate conversion coatings for our surface pretreatments. What are some replacement pretreatments we should consider?
A: Powder painting is a widely used method for corrosion protection and decorative purposes in various industries. However, corrosion is still a major problem for all of them. Different surface pretreatments prior to powder painting are being applied for better corrosion resistance and better paint adhesion properties. Phosphate conversion coatings are often used for this aim. However, industries continue to abandon using these coatings because regulations are forcing them to do so due to health and environmental concerns.
Environmentally friendly, strong pretreatment alternatives have been the subject of research in this area for many reasons. The environmental pollution caused by phosphorus, particularly in aquatic environments, has increased the interest in this element for several decades. It is considered to be responsible for the eutrophication process. The term eutrophication refers to the consequence of hyperfertilization of water into nutrients (phosphorus and nitrogen), the ultimate point of which is dystrophication (ecological imbalance). Eutrophication manifests itself in an increase in algal biomass and deoxygenation of the water column. Eutrophication affects rivers, lakes and coastal areas.
Pretreatments have to provide strong adhesion to metal and topcoat in applications and simultaneously act as a strong corrosion barrier for the metal substrate. New-generation pretreatments continue to be developed by suppliers and they are providing advantages such as lower energy consumption, low material consumption, low process cost, no heavy metal incorporation, low sludge production and better worker safety. They are advantageous both economically and environmentally.
Silanes are monomeric chemicals, often used as coupling agents and were first discovered in the 1940s. Silanes are classified, both according to their structures and their hydrophobicity. According to the chemical structure, silanes are divided as monosilylfunctional and bis-silylfunctional (the number of silicon atoms per molecule). Monosilanes only contain one silicon atom per molecule, while bis-silanes have two silicon atoms per molecule. Because bis-silanes have functional groups at both ends, they provide higher crosslink density inside the coating and more surface bonding at the metal-coating interface.
Therefore, bis-silanes generally show better anti-corrosion performance when compared to monosilanes because they have more hydrolysable groups per molecule, which leads to denser films. They can also enhance adhesion between dissimilar materials because of their low surface tension, which ensures good surface wetting. Because of the silanes’ functionality, they are known to provide great benefits as an adhesion promoter and corrosion resistant layer. Hot-dip galvanized, electrogalvanized, aluminum, low-carbon steel, castings, magnesium and zinc-alloy substrates are all of interest for silane pretreatments.
Silanes go through different reactions during preparation and application of pretreatment — specifically, hydrolysis and condensation reactions. These reactions are crucial and they result in a siloxane (Si-O-Si) network structure. There are many theories as to how the silane coating is bonded to the metal substrate. Silanes are known as coupling agents, which is defined as a compound that provides a chemical bond between two dissimilar materials, usually an inorganic and an organic. Organofunctional silanes have a functional group on one end and a hydrolyzable Si ester group on the other end.
Once hydrolysis is complete, condensation to oligomers occurs. Once the metal substrate is submerged in the hydrolyzed silane solution, the oligomers form a hydrogen bond with the OH groups of the substrate. Then, during the curing process, water is removed and a covalent linkage is formed with the substrate. Although the steps are described sequentially, these reactions can all occur simultaneously after the initial hydrolysis step. It is assumed that the metallosiloxane (Me-O-Si) and siloxane (Si-O-Si) covalent bonds are responsible for the bonding of the silane to the metal substrate.
One of the most important features of the silane and when it bonds to its substrate is that it assembles a very dense self-assembled silicon and oxygen-rich network. This film is homogenous, hydrophobic and resists water uptake and has chemical stability. This allows for a great corrosion resistance. The thickness of the siloxane layer is determined by the concentration of the siloxane solution, hydrolysis pH and silane type. For many of the silanes used for pretreatment purposes, the process time is found to have the least significant effect on the coating characteristics.
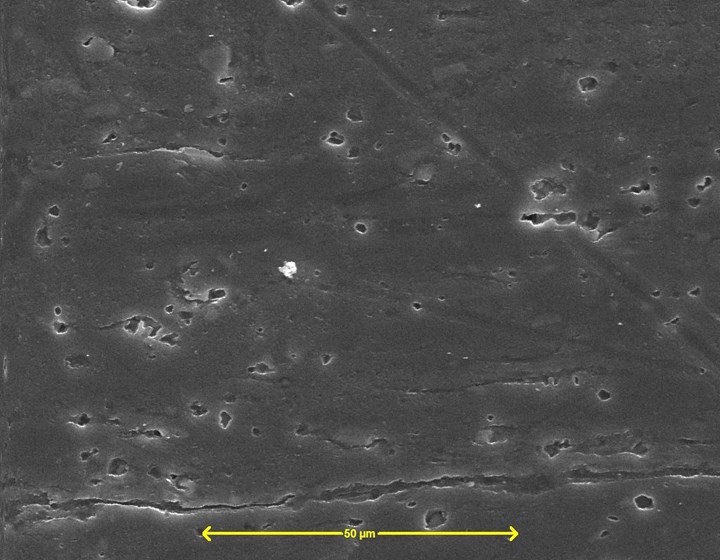
Figure 1 - Silane-based pretreatment Dynaprep PFL on aluminum SEM (SE) image, 20 keV, 1000×
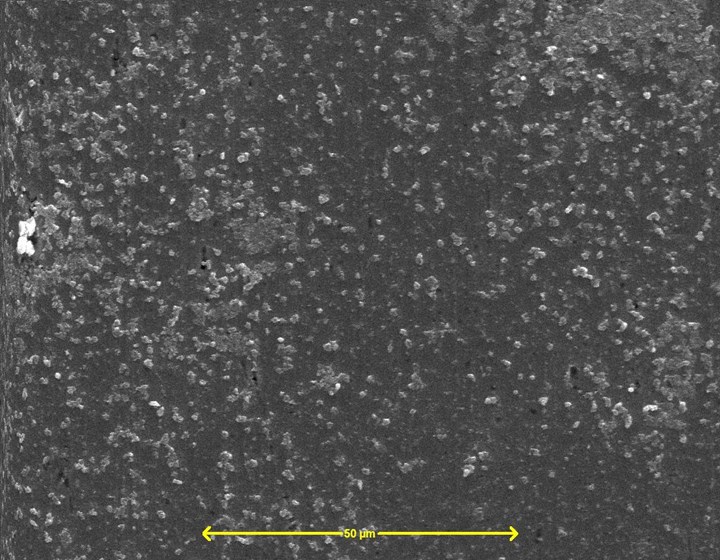
Figure 2 – Silane-based pretreatment Dynaprep PFL on steel SEM (SE) image, 20 keV, 1000×
For a successful pretreatment application, the first essential step is metal substrate cleaning to obtain a wettable surface prior to silane coating. Otherwise, contaminants can affect Si-OH adsorption during coating application. The metal surface has to be chemically activated to supply a basis for strong covalent interaction of Si-O-Si groups of coating on top. This step also helps the coating to build a uniform homogeneous distribution. Higher pH values for cleaning solutions reveal more homogeneous and finer surface morphology.
A typical procedure of silane surface pretreatment begins with degreasing the metal surface by alkaline degreasing, followed by water rinsing, sealing (optional) and, finally, drying. Many silane pretreatments today incorporate a detergency package in with the pretreatment to simultaneous clean and coat the metal substrates. Silanes are applied from dilute water solutions onto the metal substrates, mostly by immersion or spray processes. However, there are also studies using electrodeposition as well.
The use of silane mixtures, along with certain inhibitors, wetting agents and inorganic compounds, enhance coating properties and their morphologies.
Apart from additives used for better corrosion protection properties, there has become an increasing need for coloring silane films for various purposes. The demand for adding color that reacts with the Si-OH groups so that they cannot be leached out is presently in the development stage with some suppliers. This can be a useful and robust way of inline quality control of silane pretreatment application processes in industry. The development requirements set for the dyes to be incorporated into silane films are: (a) they should be water soluble; (b) they should not react with the silane or destabilize it; (c) they should become part of the silane network and should not diffuse out; and (d) different colorants, their homogeneous dispersion into the silane matrix and their effect on the overall paint system properties need to be studied in order for these materials to be used in industry.
Easy monitoring of the coating in a continuous conveyor line would be valuable because other new-generation pretreatment alternatives such as hexafluorozirconic (zirconium) acid-based pretreatments cannot provide this type of traceability. Zirconium coatings are also prone to flash rusting as a result of formulary inadequacies and poor bath control; iron buildup in the bath is a common reaction and byproduct of zirconium process, thereby reducing salt spray performance and increasing chemical consumption; high coating weights greater than 30 mg/ft2 can result if the bath’s concentration is too high or the dwell time in the coating stage is too long; alkaline drag-in may occur if there is not sufficient rinsing between the alkaline cleaner stage and the zirconium coating stage. Unlike iron phosphate coatings, zirconium coatings are very sensitive to alkaline contamination.
Stewart Tymchuk is co-president and lead formulator for silane-based pretreatment chemistry at Dynamix Inc. Visit Dynamix-inc.com.
Related Content
Corrosion Resistance Testing for Powder Coating
Salt spray can be useful to help compare different pretreatment methods and coatings but it does not tell us much about the corrosion resistance of a part over time in the field. Powder coating expert Rodger Talbert offers insights into how to get a better idea of how to improve a part’s corrosion resistance in the real world.
Read MoreSurface Preparation for Best Adhesion for Powder Coating
Kevin Biller with ChemQuest recommends the proper way to prepare a surface for powder coating that leads to excellent adhesion on 304SST.
Read MoreMasking Solutions for Medical Applications
According to Custom Fabricating and Supplies, a cleanroom is ideal for converting, die cutting, laminating, slitting, packaging and assembly of medical-grade products.
Read MoreHow to Address Declining Powder Coating Coverage Over Time
Fine particles from reclaim could be to blame for powder coating problems that emerge over time. Avoid problems by keeping hooks clean, maintaining guns and using reclaim powder quickly to avoid accumulation of fines.
Read MoreRead Next
Delivering Increased Benefits to Greenhouse Films
Baystar's Borstar technology is helping customers deliver better, more reliable production methods to greenhouse agriculture.
Read MoreEpisode 45: An Interview with Chandler Mancuso, MacDermid Envio Solutions
Chandler Mancuso, technical director with MacDermid Envio discusses updating your wastewater treatment system and implementing materials recycling solutions to increase efficiencies, control costs and reduce environmental impact.
Read MoreA ‘Clean’ Agenda Offers Unique Presentations in Chicago
The 2024 Parts Cleaning Conference, co-located with the International Manufacturing Technology Show, includes presentations by several speakers who are new to the conference and topics that have not been covered in past editions of this event.
Read More