Technical Cleanliness Expert Days Brings Together Cleaning Community for Learning and Networking
The second Technical Cleanliness Expert Days event this year expanded to one-and-a-half days, with the theme of “Cleanliness in Production and Critical Processes.”
The expectation of shipping clean machined parts to customers or cleaning parts prior to a coating process is a reality for many companies. But it’s not easy to find information on best cleaning practices. Two companies that offer cleaning technologies to the industry—Glaeser Inc. and Jomesa North America—have recognized this issue, and therefore partnered for the second consecutive year to host a conference focused on education in the field. On Oct. 29-30, in Aurora, Ohio, 33 attendees, including specialists and executives who manage quality requirements of technical cleanliness within their companies, gathered at the Bertram Inn & Conference Center for the second Technical Cleanliness Expert Days event. This year the event expanded to one-and-a-half days, with the theme of “Cleanliness in Production and Critical Processes.” The event was again sponsored by Production Machining and Products Finishing magazines.

Markus Roessler, one of the event coordinators, gave several presentations, one of which was about monitoring a cleaning environment and cleaning processes using particle traps.
With 15 speakers presenting (six of whom came all the way from Germany), many areas of expertise were covered throughout the conference. Attendees had plenty of opportunities to ask questions and network with other attendees and speakers, including at lunch, a cocktail reception and dinner, all included with the conference cost. Several presenters also set up tabletops outside of the auditorium to offer further information about the cleaning processes supported in their presentations.
The event opened with Claudia Glaeser, CEO, Glaeser Inc. (Germany), explaining her company’s business and summarizing the presentation topics for the conference.
Next, Dominick Schlipf, technical cleanliness manager for the Continental Automotive Business Unit, spoke about “Technical Cleanliness Inside R&D: Definition and Implementation.”

Attendees learned about technologies and processes of industrial cleaning systems in John Filip’s presentation.
“Technologies and Processes of Industrial Cleaning Systems,” was presented by John Filip, account manager at Ecoclean Inc. Mr. Filip talked about the characteristics of cleaning fluids, machine characteristics of aqueous and solvent machines, recovery of cleaning media and the different cleaning processes.
Clay Bielo from Pamas USA’s presentation, “Liquid Particle Counters and In-Process Particle Monitoring,” walked attendees through the company’s particle counter applications, described the technology and how these products function.
In Patrick Brag’s (project manager, cleanliness technology, Fraunhofer IPA—Germany) presentation, “Cleaner Production with VDA 19 part 2—A Classification,” attendees not only learned what VDA 19.2 is, but also about tools and techniques necessary for reaching these specification requirements. He spoke about process chain analysis, data acquisition and interpretation, data reliability, and more.
Then, in his presentation “Precision Scan for Elements: Extended Analysis for Process Improvements,” Peter Feamster, product manager, Jomesa North America, and one of the event organizers, talked about optical analysis
Mirco Nowak explained managing technical cleanliness and its requirements, and implementing technical cleanliness in his presentation.
advantages and limitations using automated optical microscopes, the disadvantages of SEM/EDX microscopes, and correlative microscopy advantages. He also spoke about production and post-production contamination.
Mirco Nowak, auditor, trainer and consultant with TopQM Systems in Germany, explained managing technical cleanliness and its requirements, and implementing technical cleanliness in his presentation, “Technical Cleanliness in Production Assembly.” He assessed technical cleanliness risks and optimization.
“Monitoring Environment and Processes with Particle Traps,” was presented by one of the event’s coordinators and Glaeser Inc.’s V.P., North America, Markus Roessler. He talked about the advantages of using particle traps, how to use them and the sedimentation analysis for production floors.
On day two of the event, Mr. Brag from Fraunhofer IPA returned to kick off the session and present, “Insights into Chemical-Filmic Contaminations,” followed by Hans-Joerg Woessner, chief technology officer at ACP Systems AG (Germany), who presented “Integrated Cleaning in Automated Production Lines with CO2 Snow Blasting.”
Dr. Martin Fahr, head of development at Naegele Engineering in Germany, joined the conference via web conferencing to talk about his company’s PuriCheck device for automated particle analysis. He gave several application examples using the device.
Cleanroom environments were explained in relation to particulate control, temperature, humidity, humidification, and so on, by Trip Textoris, president at Vernick & Associates, during his presentation, “Cleanroom Environment and Handling Concepts.”
Next, Arthur Kasson, technical sales, Northeast U.S., at Kruess, gave his presentation on “Using Analytical Tools and Measure Contact Angle, and How Surface Energy Can Be Affected by Both Surface Cleanliness and Surface Roughness.”
Mr. Roessler again took the stage to give another presentation called, “Simple Contamination Control by Visualization and Determination of Required Actions.”
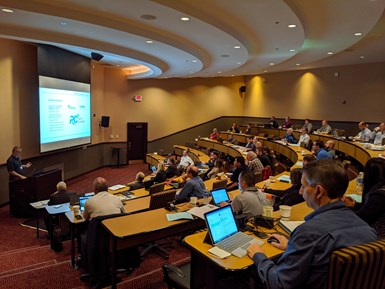
Among the attendees at the event were specialists and executives who manage quality requirements of technical cleanliness within their companies.
For the final presentation, Mr. Roessler stood in for Tatjana Qadada, general manager and owner of Lotar LLC, and gave her presentation on test pen and ink testing of plastics and metals. Ms. Qadada was unable to attend the conference at the last minute.
If you missed this year’s Technical Cleanliness Expert Days, be sure to check out the Parts Cleaning Conference at IMTS 2020, Sept. 16, at McCormick Place, Chicago, Illinois. The conference will feature a line-up of technical experts that will review everything from applications and best practices to chemistry and environmental regulations.
Also, revisit Production Machining’s and Products Finishing’s websites for information on Technical Cleanliness Expert Days in 2020.
Related Content
Solvent Versus Aqueous: Busting the Myths
Is aqueous cleaning “greener” than solvent cleaning? Is solvent a more effective cleaner than aqueous? These and many other questions are answered here to debunk the misconceptions that many manufacturers have held onto for years.
Read MorePretreatment of Black Oxide
Having issues achieving a consistent color with the application of black oxide? Start by looking at your pretreatment. Connor Callais of Hubbard-Hall offers advice for troubleshooting your black oxide process.
Read MoreImproving Wastewater Management Efficiency
Don’t find yourself underwater when managing wastewater processes. Follow these steps to improve efficiency and determine the best ROI.
Read More3-Stage Versus 5-Stage Washers
Columnist Rodger Talbert explains the difference between a five-stage washer and a three-stage washer, and how one provides better corrosion protection over the other.
Read MoreRead Next
VIDEO: Vapor Degreasing Process Uses TCE Replacement to Eliminate Hazardous Waste
A solid relationship with a solvent manufacturer has aided Electro-Spec Inc. with the implementation of a trichloroethylene replacement material in its vacuum degreasing unit to clean a customer’s micromachined parts more efficiently.
Read MoreCleanliness Compliance is Critical for Automotive Suppliers
Although not every shop has been affected by cleanliness specifications, many suppliers to automotive OEMs are already complying with stringent cleanliness standards. In Ford Motor Co.’s case, it has created its own cleanliness standards in order to save money and credibility.
Read More6 Things to Know about Ultrasonic Cleaning
I revisit an ultrasonic cleaning article to explain six main ideas that jumped out at me as points for shops to remember when selecting ultrasonic equipment.
Read More