AkzoNobel Invests in Coatings Technology to Support Beverage Can Industry
AkzoNobel’s two products in its Accelstyle range and building of a production plant in Spain aim to support the beverage can industry while shifts between materials.
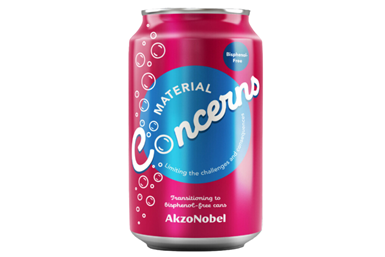
Photo Credit: AkzoNobel
The beverage can industry’s ongoing efforts to move to products free from materials of concern are being boosted by coatings technology from AkzoNobel. The support comes in the form of the development of two products in its Accelstyle range and the construction of a production plant in Vilafranca, Spain.
The two developed products belong to the company’s packaging coatings business’ Accelstyle range. Designed for the exterior of conventional two-piece aluminum beverage cans, both are free from bisphenols, styrene and PFAS. They follow the release of Accelshield 700, an internal coating for beverage can ends that is free of intentionally added bisphenols, which complies with U.S. Food and Drug Administration (FDA) and European Union regulations. Both Accelstyle 100 and 200 are said to be able to be introduced into existing production processes.
Simultaneously, AkzoNobel is investing €32 million in a plant in its Vilafranca site, which will ultimately produce bisphenol-free coatings for the metal packaging industry in the Europe, Middle East and Africa (EMEA) region. The facility will use advanced automation and has been designed according to high ecoefficiency standards, enabling the company to make a step change in energy and material efficiency. The plant is expected to be operational by mid-2025 and create around 40 jobs.
“The Vilafranca plant will allow us to offer leading-edge products to any customer and country in EMEA, responding to the most stringent bisphenol regulations in force in Europe,” says Jim Kavanagh, director of AkzoNobel’s industrial coatings business. “The investment is in line with our view that bisphenols are no longer required to create safe food contact coatings for metal packaging.”
AkzoNobel says its approach to the bisphenol transition of metal cans prioritizes consumer safety and sustainability with responsible material substitutions while also taking care to limit disruption to the value chain. The company continues to work closely with customers to help accelerate adoption of bisphenol alternatives.