Connecticut Businesses Join Forces for Educational Program
A group of rival businesses comes together to educate the next generation of metal finishers.
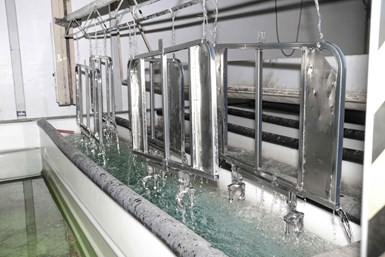
Connecticut manufacturing is known for providing finishes for some of the most impressive products in the world including aerospace components, submarines, automobiles, electronics, medical equipment and hardware, as well as decorative finishes for everyday items that touch our daily lives.
The Northwest Regional Workforce Investment Board (NRWIB, Waterbury, Conn.) has announced that a group of businesses — often metal finishing industry competitors — are working together to pioneer a new educational program for the metal finishing industry. Known as METAL (Master Electroplating Through Applied Learning), the program will launch in the Fall of 2023.
The initiative, which is supported by the Northwest Manufacturing Regional Sector Partnership, is pioneered with the expertise of local metal finishers: Metal Finishing Technologies (Bristol, Conn.), UniMetal Surface Finishing LLC (Thomaston, Conn.), Summit Plating (Thomaston, Conn.), American Electro Products (Waterbury, Conn.), Waterbury Plating (Waterbury, Conn.), and Pape Electroplating (New Britain, Conn.), and with support from chemical manufacturers Hubbard-Hall (Waterbury, Conn.) and MacDermid Enthone Industrial Solutions (Waterbury, Conn.).
“It was important for us to create this now,” says George A. LaCapra Jr., President, UniMetal Surface Finishing LLC. “The market needs skilled workers and people are looking for ways to grow in their careers. The skills offered through this class are highly transferable and offer a career filled with technical growth in a fascinating highly stable industry that very few know about.”
The curriculum of METAL will be practical and straightforward, offering real life hands-on applied learning. The NRWIB says that those going through the program will learn theory (need, opportunity and finishing’s key role in the future), science (the fundamentals behind the art of transforming metals) and applied learning (skills for applying finishes and launching a career).
“If the participant has the right attitude and puts in the effort to combine the skills taught at METAL, they will be given the opportunity to grow their career,” says Catherine Awwad, president/CEO, NRWIB.
“When we set out to create METAL, one thing has always been clear, the next generation of workers needs to know – your success and career are important to us,” adds Pete Mirabello, Chairman, Metal Finishing Technologies LLC.
The NRWIB is the primary convener of the manufacturing regional sector partnership and played an essential role in connecting this group of manufacturers to develop a solution to address the workforce challenges in metal finishing. The group says METAL offers interested individuals a head start on growth in a career path ripe with opportunity. The program is designed to help individuals learn through hands-on experience and hard work, and to earn their way to important roles in plating, engineering, chemistry, quality, maintenance, or production and sales.
Related Content
-
Products Finishing Reveals 2023 Qualifying Top Shops
Each year PF conducts its Top Shops Benchmarking Survey, offering shops a tool to better understand their overall performance in the industry. The program also recognizes shops that meet a set of criteria to qualify as Top Shops.
-
Troubleshooting Alkaline Zinc
One of the most common problems that can arise when plating with alkaline zinc is an imbalance of brightener in the solution. In this helpful Ask the Expert article, Chad Murphy of Columbia Chemical discusses how different zinc metal concentrations and brightener concentrations can impact efficiency.
-
Products Finishing Reveals 2024 Qualifying Top Shops
PF reveals the qualifying shops in its annual Top Shops Benchmarking Survey — a program designed to offer shops insights into their overall performance in the industry.