Dürr Technology Powers Scalable Paint Shop for Enovate EVs
Dürr says its EcoProFleet AGVs, RoDip E process and EcoDry X system have allowed Enovate to construct a scalable paint shop for its Changsha EV factory.
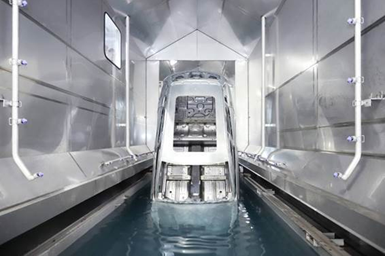
Dürr’s (Southfield, Mich.) technology will allow Enovate (Zhejiang, China) to construct a scalable paint shop, which Dürr says can flexibly grow to meet demand. Particularly important to this capability are Dürr’s EcoProFleet of automated guided vehicles (AGV), RoDip E paint process and EcoDry X system.
The AGVs are a flexible conveyor technology that Dürr says is not restrained by cycle times. Dürr says its EcoProFleet is the first AGV designed specifically for paint shops, that it is resistant to paint and solvents and that it comes equipped with an integrated laser scanner and a speed limit to ensure safety. Enovate has purchased four of these AGVs, with the option to buy more as demand requires.
Enovate’s new paint shop is also the first in China to rely on Dürr’s RoDip E rotational dip process in pretreatment with a thin-film process and cathodic electrocoating. Unlike the established RoDip M, RoDip E is electric, with the electric power source enabling Enovate to program each trolley for a specific car body’s requirements. Per-trolley programming enables Enovate to define optimized immersion curves in terms of turning and travel speeds, improving draining and carryover. Dürr also says the technology has a comparatively short immersion tank with a small tank volume to minimize consumption of water, chemicals and energy.
Dürr’s EcoDry X system is installed for the topcoat spray booth. It uses cardboard filter boxes as a separating agent for overspray, which the company says is more environmentally friendly than processes that use a mixture of water and chemicals. The process air is also redirected to the air recirculation system, which Dürr says reduces the paint shop’s total energy consumption by around 30% compared with a conventional wet scrubbing system.
The new e-car factory is scheduled to start production this year.
Related Content
-
Top Shop Leader Focuses on Its People as Key to Success
Twin Cities job shop, Avtec, was named a Top Shop for the third time in 2022, due in no small part to its commitment not only to the work it produces but to those who produce it — its employees.
-
Take Full Advantage of Industry Events
As travel plans ramp up for the year, what industry events will you attend? Products Finishing offers a quick look at some of the upcoming opportunities for 2024.
-
Professional Plating Expands Zinc, Ecoat Offerings
Ever expanding, Professional Plating of Brillion, Wisc., has announced two capital investments: a second zinc line and an upgrade of its ecoat capabilities.