Henkel and BTG Labs Partner to Establish Surface Measurement Standards
With the inclusion of water contact angle recommendations for surfaces to the Henkel Technical Data Sheets (TDSs), the TDSs are now more comprehensive.
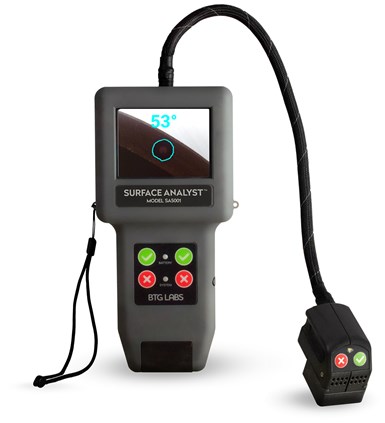
BTG Labs Surface Analyst
Photo Credit: BTG Labs
Highly engineered products, such as radar, guidance, and communication systems for commercial and defense aerospace applications use highly engineered materials when building products. Providing technical guidance on the proper handling and use of products is critical to success in the field. Standardization of training, including a consistent approach with clear technical documentation on proper handling techniques, will provide guidance in the adhesives industry.
Vendors who supply highly engineered materials, such as adhesives, to sophisticated manufacturers understand that providing a high-quality product is not enough, clear user guidelines are critical to maximize performance and minimize failures.
Providing Sophisticated Surface Preparation Guidance
Henkel (Madison Heights, MI) has the initiative to provide more sophisticated guidance regarding surface preparation to maximize the performance of adhesives. Within their Loctite product line, three products now have water contact angles (WCAs) included on their technical datasheets. These products, Loctite Ablestik 8175, Loctite Ablestik CF3350 and Loctite Ablestik 5025E, are used in a variety of applications including solder replacement in microelectronic interconnect applications, electrical, thermal and mechanical assembly applications, and bonding “hot” devices onto heatsinks.
With the inclusion of water contact angle recommendations for surfaces to the Henkel Technical Data Sheets (TDSs), the TDSs are now more comprehensive.
To achieve effective adhesive bonding, surfaces need to be free from contamination. Water contact angles can provide an objective measurement of whether a surface is properly prepared for adhesive bonding. In an effort to help their customers obtain effective bonding results for each and every product, Henkel partnered with BTG Labs (St. Bernard, Ohio) to update their TDSs to include contact angle specifications.
“As a result of including WCAs on the Henkel Technical Data Sheets, we have seen a strong uptick in customer satisfaction and a marked decrease in technical support tickets for these products,” said Doug Katze, Market Segment Manager, Defense & Space, Henkel Corporation. “This initiative has been so successful that we plan to include WCAs on more of our Technical Data Sheets.”
Depending on the industry, designing a new product can take months to years. Going forward, there is an opportunity to include successful adhesion best practices in the TDSs for new products. Before going to market critically assess the adhesive bonding processing conditions that are prevalent in the industry. Invest the time necessary to develop objective WCA standards to include on the TDSs. Taking these steps will help ensure a clear understanding of how to use the new product in a way that will help ensure manufacturing success.
Most organizations have policies in place regarding appropriate “triggers” for updating existing specifications. This updating process may also be impacted by external sources — including certifying bodies, like ISO, or regulated industries with formalized requirements for making any changes within their supply chains.
Common reasons that corporations might choose to update existing specifications include changes in raw material availability, changes in supply sources, or feedback from the field that organizations are trying to proactively mitigate through enhanced internal education and customer training. Other triggers include customers’ increased focus on quality. They expect their incoming raw materials to have consistent reliability and to be manufactured to comply with published specifications.
Related Content
Wall Colmonoy Hires Business Development Manager, Surfacing Products
Wall Colmonoy welcomes Josh Gardner as its business development manager of surfacing products.
Read MoreLapping, Polishing Film Maximizes Strengths, Maintains Flexibility
Dia-Strip and Dia-Sheet film from Titan Tool Supply has a distinct construction that the company says makes it durable while remaining flexible, bendable and formable.
Read MoreBlasting Beads Made of Lead-Free Natron Glass
SwarcoBlast blasting media are made for use in a multitude of surface refinement applications.
Read MoreRobot-Ready Grinding Systems for High-Speed Production
Advanced rotary surface grinders now come “robot-ready” to facilitate integration with third party robotic arms and fully automate the process from loading to unloading.
Read MoreRead Next
A ‘Clean’ Agenda Offers Unique Presentations in Chicago
The 2024 Parts Cleaning Conference, co-located with the International Manufacturing Technology Show, includes presentations by several speakers who are new to the conference and topics that have not been covered in past editions of this event.
Read MoreDelivering Increased Benefits to Greenhouse Films
Baystar's Borstar technology is helping customers deliver better, more reliable production methods to greenhouse agriculture.
Read MoreEpisode 45: An Interview with Chandler Mancuso, MacDermid Envio Solutions
Chandler Mancuso, technical director with MacDermid Envio discusses updating your wastewater treatment system and implementing materials recycling solutions to increase efficiencies, control costs and reduce environmental impact.
Read More