Interpon Powder Coating is Helping Portuguese Manufacture With Sustainability
The cycling accessories team at Rodi has found a way of accelerating its environmental ambitions by switching from anodizing to a more sustainable, energy-efficient process using Interpon powder coatings from AkzoNobel.
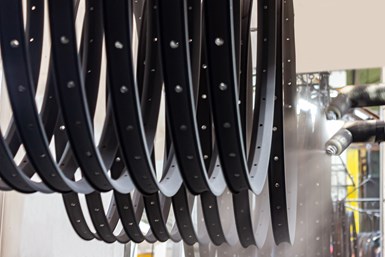
The cycling accessories team at Rodi, a Portuguese manufacturer of aluminum rims and wheels, has found a way of accelerating its environmental ambitions by switching from anodizing to a more sustainable, energy-efficient process using Interpon powder coatings from AkzoNobel.
Rodi sought an alternative to anodizing that was durable, sustainable, and capable of delivering style with a lower gloss finish. The bespoke Interpon powder coating is designed to deliver a smooth, soft ultra matt finish, with just three percent gloss. It also comes with AkzoNobel’s X-Pro technology which is stated to protect against scratches, UV light, and weather.
Rodi and the Interpon team share the ambition to protect natural resources and reduce energy consumption. Rui Mendes, Manager of Rodi’s Rims and Wheels business, says he already has plans to further increase production capacity with the team’s support. “We are serving an environmentally conscious audience who are pushing a more sustainable agenda which we take very seriously. For us, this starts with the suppliers we work with and the products we use, and it is why we use Interpon.” Mendes says that in a typical year, Rodi manufactures 3 million rims and 500,000 wheels at its 60,000 m2 manufacturing site in Aveiro, Portugal.
The partnership began two years ago when AkzoNobel demonstrated how switching from a previous supplier to an Interpon 610 Low-E powder coating reduced Rodi’s energy consumption by 25 percent. Interpon 610 Low-E requires lower curing temperatures and allows them to coat 20 percent more rims per box than was previously possible.
Rodi also became the first manufacturer in its sector to use AkzoNobel’s OptiMesure software which controls paint usage and minimizes any reworking by carefully measuring and managing the thickness of the coating being applied.
Related Content
-
Masking Solutions Provider CFS Dramatically Expands Capabilities and Capacity
Custom Fabrication & Supplies (CFS) completed a new plant expansion packing 10 times the capacity into twice the space. It dramatically enhances the supplier’s custom capabilities to provide extremely precise and cost-effective masking solutions.
-
Selecting the Right Outdoor-Durable Powder Coating
The powder coating industry offers an array of chemistries to provide an excellent match to the manufacturer’s expectations for outdoor durability.
-
Products Finishing Reveals 2023 Qualifying Top Shops
Each year PF conducts its Top Shops Benchmarking Survey, offering shops a tool to better understand their overall performance in the industry. The program also recognizes shops that meet a set of criteria to qualify as Top Shops.