P&C Fabrication and Coating Adds Titan Blast Room to Powder Coating Operations
Titan Abrasive Systems has supplied P&C Fabrication and Coating with a blast room, bringing blasting operations indoors for powder coating.
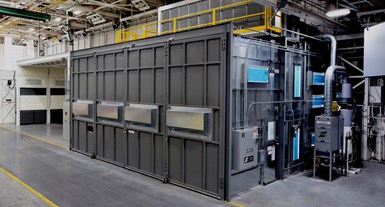
The Titan Blast Room at P&C Fabrication, like the one pictured above, enables the company to bring its abrasive blasting operation indoors, avoiding any weather-related delays. Photo Credit: Titan Abrasive Systems
Titan Abrasive Systems, a designer and manufacturer of quality surface preparation, surface finishing and sandblasting equipment, has supplied a fully equipped blast room to P&C Fabrication and Coating. The blast room, which measures 10 × 10 × 15', is located in a building dedicated to P&C’s powder coating operation. This includes parts brought to the company from its customers, as well as pieces it creates in a second building dedicated to fabrication and welding.
Abrasive blasting is performed on all metal parts that come through the shop for powder coating, resulting in a better surface for coating adhesion. Occasionally, P&C blasts outside parts that are not going to be powder coated — mainly car parts that will be painted in a body shop.
According to Tara Cerar, co-owner of P&C, the purchase of the Titan Blast Room was necessitated by two critical factors. “Since we began powder coating, we’ve been doing all our blasting outdoors, which makes the operation completely weather-dependent,” Cerar says, noting that the company is using blasting equipment purchased from Titan back in 2018. “When it rained — or even when there was high humidity — we couldn’t get any blasting done, which delayed other parts of the operation and slowed delivery times. What’s more, we were not able to reclaim our blasting media. All the media we purchased was for one-time use, which became quite costly.”
With the Titan Blast Room, blasting can be performed at any point throughout the workday (as well as during a second shift when the workload requires it). With no environmental issues to deal with, Cerar expects productivity to increase while also promoting that on-time delivery of completed projects is easier to achieve.
Cerar also pointed out that the Titan reclaim system purchased with the blast room will enable the company to reclaim its media, meaning it can use higher-quality materials. “We’ll be primarily using aluminum oxide in the new room,” Cerar says. “It’s a very abrasive material that creates excellent adhesion for the powder coating process. It’s an expensive media, but because we can reclaim and reuse it, the cost goes down substantially.”
Because of increased productivity, P&C will be in a position to take on more work, further increasing profitability. “There have been times we had to turn down jobs because of the volume we already had,” Cerar explained. “But since our blasting operation will no longer be slowed down by weather, we’ll be getting jobs out faster, creating open slots for more new work.”
Related Content
-
Products Finishing Reveals 2024 Qualifying Top Shops
PF reveals the qualifying shops in its annual Top Shops Benchmarking Survey — a program designed to offer shops insights into their overall performance in the industry.
-
Products Finishing Reveals 2023 Qualifying Top Shops
Each year PF conducts its Top Shops Benchmarking Survey, offering shops a tool to better understand their overall performance in the industry. The program also recognizes shops that meet a set of criteria to qualify as Top Shops.
-
Reduced, Reused and Recycled Powder Coatings Are the Future
They say necessity is the mother of invention, and with millions of pounds of powder coating going into landfills a year, these two companies have found novel approaches to dealing with this waste stream.