Replacement or Reinforcement of DLC Coatings
Expanite, a Danish pioneer of surface hardening of stainless steel and titanium, replaces or supplements the widespread DLC coatings with its technology.
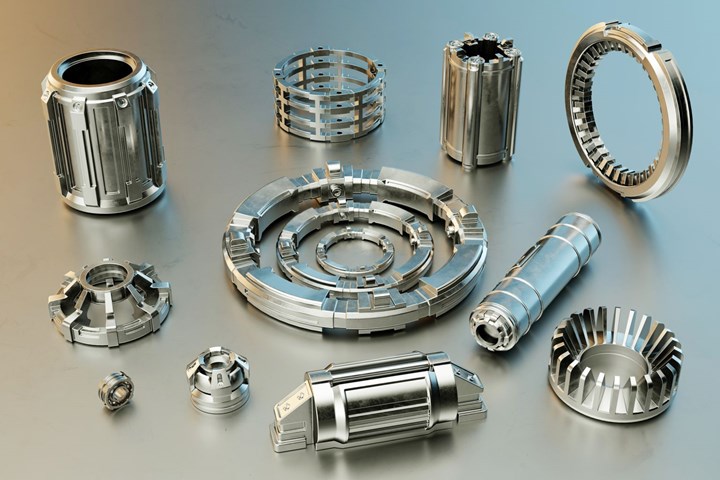
Diamond-like carbon or DLC coatings are today used in many areas where excellent friction properties and good wear resistance are required on component surfaces. The DLC layers applied by complex, time-consuming and costly PVD or PACVD processes are usually only a few micrometers thick. If the part also is required to be corrosion-resistant, making the use of stainless steels mandatory, the DLC system has some weak points. The soft stainless steel as the carrier medium and the correspondingly high hardness gradient to the thin DLC layer promote the eggshell effect this might lead to a defect in the coating, and it will easily start peeling off.
Expanite (Copenhagen, Denmark) offers state-of-the-art solutions for surface hardening treatment of stainless steels and titanium. With Expanite's processes, it is possible to increase the material’s surface hardness tenfold while at the same time maintaining and even increasing its corrosion resistance.
The Expanite technology, specially developed for corrosion-resistant materials, offers a solution for austenitic, martensitic, ferritic and duplex stainless steels as well as for expensive nickel-based alloys such as Inconel and Hastelloy. The new special process ExpaniteHard-Ti, which the Expanite team of experts in Denmark has developed to market maturity in recent years, is used for titanium materials.
Diffusion hardness layer
Surface hardening of Expanite brings the solution using a gas-based diffusion process to store carbon and nitrogen deep in the component surface. This guarantees a better load-bearing capacity and efficiently counteracts the eggshell effect. If defects occur in the hardness layer while the part is in use, this does not lead to further flaking because, in contrast to the applied DLC layer, the Expanite technology is a diffusion hardness layer that is coherent with the base material.
Environmentally friendly
In addition to technical and commercial advantages, the sustainability of the Expanite process is playing an increasing role for customers. The gas-based diffusion process is significantly more energy-efficient and environmentally friendly than comparable wear protection processes and, thanks to the treatment in vacuum, no time-consuming cleaning of the parts, e.g., with aggressive chemicals, is necessary after hardening with the Expanite process.
“We have already replaced the classic DLC coating in various applications, from the typical running and sealing surfaces in bearings, through pump components or knife edges to applications in medical technology,” explains Dr. Holger Selg, application expert and Expanite Sales Director DACH, and continues: “In some cases, the two technologies were also combined and a DLC layer was applied in addition to our Expanite hardness layer in order to obtain a very resilient system.”
Related Content
-
Replacing Discontinued Vapor Degreasing Fluids – 3 Things to Consider
What do you do when you learn your trusted line of vapor degreasing cleaning fluids will soon be discontinued? Elizabeth Norwood of MicroCare discusses what you should keep in mind when replacing discontinued vapor degreasing fluids.
-
Understanding Robotic Vacuum Impregnation
Robotic vacuum impregnation can be used to seal porosity, minimize scrap, increase throughput and reduce costs.
-
Top Shop Emphasizes Dedication, Work Ethic
With a primary focus on aerospace and defense work, American Metaseal Corp. of Arbutus, Maryland, has qualified as a Top Shop on multiple occasions.