Wagner Refines Wiegand-Glas Group's Liquid Coating System
Wagner’s high-speed rotation atomization concept gives Wiegand-Glas’ operators permanent and safe access to the paint supply, which the previous system denied them.
Wiegand-Glas Group (Steinbach am Wald, Bavaria, Germany) manufactures and sells individual packaging concepts made of glass and polyethylene terephthalate (PET) for the beverage and food industries. At its site in Steinbach am Wald, Wiegand-Glas produces around 3.5 million glass containers per day. It also provides services related to finishing, logistics and recycling. The company recently decided that its electrostatic coating system was inefficient and unsustainable, leading it to update its system with equipment from Wagner (Markdorf, Germany).
Wiegand-Glas’ previous system for electrostatic liquid coating was highly complex because it processed conductive, water-based paint in combination with electrostatics. Because of the internal charging of the application equipment, the entire system was permanently under high voltage during production, and the paint supplies stood on insulated pedestals. In order for operators to access the components during production, they had to be separated into two paint kitchens. The company desired a control system that was more intuitive in order to minimize operating errors, which led them to Wagner.
Wagner supplied Wiegand-Glas with electrostatics for its updated liquid paint system, which includes the application equipment, paint supply and associated control system. The liquid coating booth of the previous system remained in place.
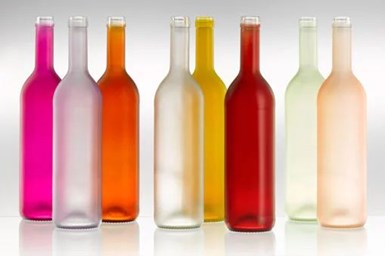
In the first step of the new process, the glass bottles are processed in the paint booth with GA 1030 automatic airspray guns. The upstream guns generate an initial paint film on the glass. Due to the conductive water-based paint, the paint film forms a bridge to the ground potential. According to the company, this makes the glass electrically conductive and creates an electrostatic effect. Airspray guns then paint the bottom of the bottle in a different color from the main bottle.
The subsequent electrostatic coating uses Wagner’s TopFinish Bell 1S ECH, a high-speed rotation atomizer with external charging that is mounted on a linear axis. The high voltage emitted via the electrode ring creates ambient ionization, which charges the sprayed material.
Compared to the version with internal charging, the new system does not have to be specially insulated. Wagner says the Bell 1S ECH can be adapted to suit the coating and the respective bottle shape by means of different disk sizes and adjustable steering airs. According to the company, the very fine atomization enables application efficiency of over 80 percent to be achieved, depending on the material, the flow rate and workpiece. Therefore, the liquid paint system also contributes to sustainable production.
In addition, Wagner says its Zip 52 double diaphragm pumps ensure a reliable paint supply to the coating system. The system is managed by an intelligent control system that has been specially tailored to the needs of Wiegand-Glas and, among other things, allows all parameters to be stored in a recipe management system. This control is designed to support users in achieving repeatable coating results in consistently high quality.
Wagner’s high-speed rotation atomization concept gives Wiegand-Glas’ application engineers permanent and safe access to the paint supply, which the previous system denied them. Line lengths were optimized and changeover times between colors and paint stations were reported to be significantly reduced. In addition, the intelligent control system is designed to minimize operating errors. In the previous system with internal charging, there was a risk of leakage currents due to contamination on the insulated platform. Since this is eliminated in an external charging system, it is easier to maintain and clean. With the new application equipment, high material efficiency and surface quality are able to be sustainably achieved.
Related Content
TTX’s Automated Conveyor Carrier System Offers Wireless, Flexible Operation
ACC system designed for reliable, consistent point-to-point movement of everything from small to heavy parts.
Read MoreMasking Solutions Provider CFS Dramatically Expands Capabilities and Capacity
Custom Fabrication & Supplies (CFS) completed a new plant expansion packing 10 times the capacity into twice the space. It dramatically enhances the supplier’s custom capabilities to provide extremely precise and cost-effective masking solutions.
Read MoreShedding Light on Surface Inspection
State-of-the-art reflector-based lighting system improves luminosity and ergonomics for surface inspection tasks while reducing energy usage.
Read MoreFinishing Systems Provider Celebrates 150 Years, Looks to Future
From humble beginnings as an Indiana-based tin shop, Koch Finishing Systems has evolved into one of the most trusted finishing equipment providers in the industry.
Read MoreRead Next
Education Bringing Cleaning to Machining
Debuting new speakers and cleaning technology content during this half-day workshop co-located with IMTS 2024.
Read MoreA ‘Clean’ Agenda Offers Unique Presentations in Chicago
The 2024 Parts Cleaning Conference, co-located with the International Manufacturing Technology Show, includes presentations by several speakers who are new to the conference and topics that have not been covered in past editions of this event.
Read MoreDelivering Increased Benefits to Greenhouse Films
Baystar's Borstar technology is helping customers deliver better, more reliable production methods to greenhouse agriculture.
Read More