Episode 33: An Interview with Hope Dollarhide, FANUC
As attitudes about automation in the finishing industry change, Products Finishing checks in with Hope Dollarhide, project engineer with FANUC, to hear her insights into automation trends in the industry.
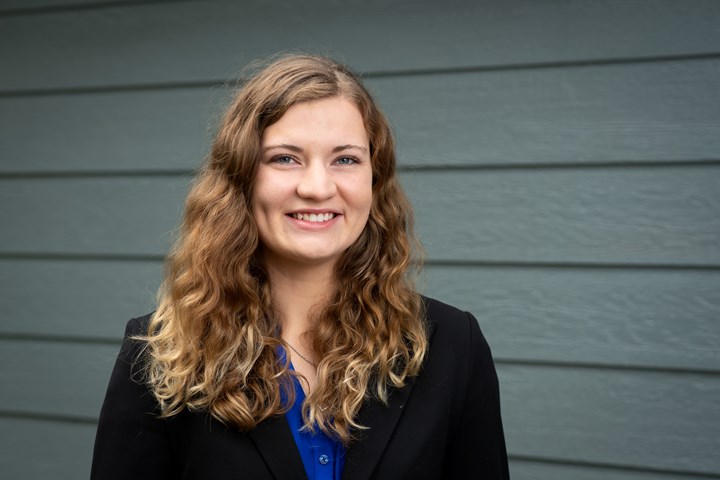
Attitudes about automation in the finishing industry are changing. Once relegated to high-volume production, automation solutions are seeing increasing adoption for finishing applications, driven by shifting trends in the workforce, rapid advances in robotics and smart technology, as well as the need for repeatability and consistency in quality. In this installment of On the Line, Products Finishing sits down with Hope Dollarhide, project engineer for automotive component and industrial paint with FANUC, to hear her insights into automation trends in the industry.
Check out an excerpt from the interview (below) or stream the full podcast interview (above):
What are some of the factors that are influencing trends toward automation, particularly in the finishing industry?
I think across the board, we all know that the economy has changed a lot over the past three years since the pandemic. One of the biggest things we’ve seen is that finishers have a lot of labor shortage issues or a lot of high turnover in their paint shop. That’s putting them in a difficult situation, “What do I do if all four of my best painters have COVID and they can’t come into the facility? Or what if we’re shut down?”
We’re also seeing a change in the identity of the workforce. I think that is a huge factor in the demand for automation. With the younger generation, we’re not seeing a huge group of people who want to go into manual spraying or finishing. That identity of the workforce is making people kind of think outside the box. People are looking to automation as an answer for those challenges.
Traditionally, finishing automation has been most often used for high volume production of dedicated parts, with shops processing a varying mix of parts running on mostly manual processes. How do you see this changing or evolving with automation?
I think that is a really important question. If you paint something different every single day or paint 20 different parts every day, how can you take the time to program? Because programming the robot can be time-consuming — it may take a few hours or a few days, depending on the complexity of your part. With all that programming time, high-mix finishers are struggling to introduce automation. And that’s something we’ve been hearing over the past few decades.
So, we are looking at what we call easy-teach solutions — tools that you can use to minimize that programming time.
FANUC offers lead through teach programming or hand-guided programming. That gives you the ability to actually grab the robot and lead through teach — you don’t have to have the teach pendant in your hand, you just kind of guide the applicator along the part. This allows you to kind of eliminate the actual traditional teach pendant kind of programming.
We also have offline tools — 3D simulation that allows you to do all of your programming offline. So, let’s say you know that next week, you’re going to have a whole bunch of different parts that you’ve never painted before. Without causing your line or paint shop to stop [production], you can do the programming on your PC and then upload the programs to the robot.
We also have other tools such as iRVision, which doesn’t eliminate the programming time, but aids customers who have issues with aligning their parts in the same [orientation] every time. iRVision can help align your process or your paint program to where the part is actually located.
We also are working with third-party integrators and other companies that are introducing artificial intelligence (AI) as a potential tool.
With the increasing adoption of robotics and AI, what do the finishing jobs of the future look like?
One thing here at FANUC that we like to say is that the robots are doing the dull, dirty and dangerous jobs. When you implement the use of robots in a manufacturing facility, you’re introducing new jobs, because we’re not really talking about total lights-out facilities. We still need someone to operate the robot. We still need someone to program the robot and perform maintenance. And, thanks to smartphones, PCs and smart TVs, people are a lot more comfortable around robots and computers than they were, say, 25 years ago.
What advice do you have for traditional finishing operations that might be considering investments in automation?
I would say to definitely reach out to a system integrator — there’s probably someone you’re already working with [at your equipment supplier]. Especially on the finishing side, those integrators are really knowledgeable… they know the painting process and they know paint shops. And on top of that, just to continue to get outside your comfort zone.
Related Content
TTX’s Automated Conveyor Carrier System Offers Wireless, Flexible Operation
ACC system designed for reliable, consistent point-to-point movement of everything from small to heavy parts.
Read MoreFinishing Systems Provider Celebrates 150 Years, Looks to Future
From humble beginnings as an Indiana-based tin shop, Koch Finishing Systems has evolved into one of the most trusted finishing equipment providers in the industry.
Read MoreRobots, AI and Superb BMW Surfaces
There isn’t an automotive paint shop in the world that doesn’t have post-paint inspection and defect processing. But BMW is doing this with levels of technology at a plant in Germany that exceed all other paint shops in the world.
Read MoreSurface Prep Solution for Rusted Rebar in Concrete
Julie Holmquist of Cortec Corporation discusses passivating corrosion on rebar and other reinforcing metals.
Read MoreRead Next
Episode 31: An Interview with Matthew Kirchner, LAB Midwest
PF columnist and host of the TechEd Podcast Matthew Kirchner, president of LAB Midwest, discusses the latest in workforce trends in the manufacturing and finishing industries.
Read MoreEpisode 30: An Interview With Rhonda Dibachi, CEO, HeyScottie
Rhonda Dibachi, founder and CEO of HeyScottie, discusses her new automatic pricing engine designed to help manufacturers find finishing services and streamline the price quoting process.
Read MoreEpisode 32: An Interview with Bobby Haggard, TrinSoft LLC
A wide variety of ERP systems are on the market ranging from off-the-shelf solutions to custom programs. What should finishing operations keep in mind when exploring a new ERP solution?
Read More