A New Dawn for Sunset Industrial Applications
Large coating facility goes online after significant market research.
No one would have blamed Jim Nicklas one bit if he had taken his dream of building a world-class painting facility and shelved it for another tomorrow.
Several years ago, Nicklas saw the need for a large coating operation to serve the multitude of OEMs in and around the Cumberland Valley, Pennsylvania area, which is about 50 miles south of Harrisburg and 90 miles west of Baltimore.
But Nicklas, a U.S. Marine Corps veteran, knew that where there is a need, there should be something there to fill it. “The area lacked world-class painting capabilities and capacities,” Nicklas says.
Sunset Industrial Applications (SIA) now stands proudly with more than 50,000 square feet of space for painting, powder coating and part preparation. The facility opened in April 2014 and is now aggressively seeking both customers and joint venture partners.
“SIA was built to respond to what our customers told us was a significant problem and a critical market need,” he says.

Sunset Industrial Applications’ owners saw the need for a large coating operation to serve the multitude of OEMs in and around the Cumberland Valley area.
Doing the Homework
Market and OEM trends demonstrated this project had strong opportunity, and later Nicklas validated this with customers.
“It was a leap of faith confirmed on trends—a calculated risk to provide a real value to the market,” says Laura Nicklas Sponseller, SIA’s business development guru and also Jim’s daughter. “Many OEMs indicated that this facility was needed and that they would support it. This was a classic ‘build it and we will come’ business case.”
Nicklas spent almost a year studying the industrial trends in the Cumberland Valley area and seeing if economic data would support spending time, money and risk on a new coating facility.
The numbers for the region were impressive. To start, Interstates 83, 81, 76 and 15 all pass through Franklin and Cumberland counties. This highway system gives it close proximity to major cities such as Baltimore, New York City, Philadelphia and Washington D.C., which makes Franklin and Cumberland one of the largest logistic hubs in the U.S., and also made it a prime area for a business looking for a place to locate or combine facilities.
In addition, Cumberland County is just one of about 70 counties in the U.S. with a Triple-A bond rating by Standard and Poor, making it healthy for businesses to locate and do business there.
The Franklin County Area Development Corp. (FDADC) recently brought Procter and Gamble to build a 1.7 million-square-foot facility off of I-81. The FCADC also helped engineer in 2013 the completion of 14 economic development projects resulting in more than $137 million of capital investment and the creation and retention of more than 1,300 jobs.
The Cumberland County Economic Development Department (CCED) has worked hard to attract new industries, bringing in more than 50 businesses over the past 10 years, including Office Depot, Alacer Corp., Campus Door and others.
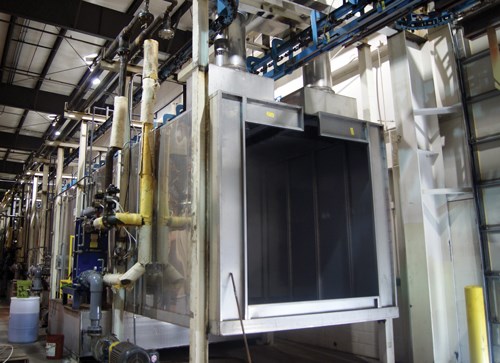
The line has five high-bays and overheads measuring 200 feet by 250 feet, all controlled by a programmable logic controller.
New Growth
“Since August 2005, CCED has attracted approximately $87 million in private sector investment,” says Omar Shute, CCED executive director. “Cumberland County is also recognized by companies for its highly productive and educated workforce, low taxes, outstanding highway infrastructure and exceptional location.”
Nicklas recognized the regional area has experienced significant growth with major OEMs and their supply base localizing.
“OEMs have been trending toward assembly facilities, following the automotive industry,” says Nicklas, who also noticed that many coaters were simply not equipped to handle the demands of increased OEM paint specifications.
As part of the Sunset Industrial Applications business case research, the comapny sat down with the major OEMs and customers to ask direct questions about their markets, trends, supply base and quality. “We recognized that with the rising paint specifications and requirements the OEMs were pushing out to their suppliers, there really wasn’t anyone in the region that could provide that level of service and quality.”
Developing Business Case Study
The company started holding several focus groups in 2012 to talk with OEMs and then commissioned a feasibility study to determine if industry trends would support a large-size coating facility.
What they found among several OEMs were identifiable market issues:
--‘Direct-to-Metal’ coating processes and improper substrate preparation,
--Problems with laser edges, skip welds, seam and lap joints,
--Hundreds of millions of dollars in rework, freight and handling costs.
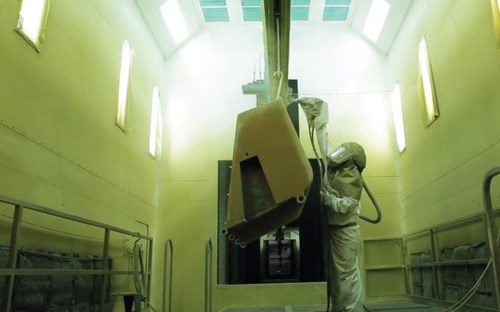
The business case was becoming clear: Save the OEMs and their suppliers’ time and money, while improving their quality at competitive pricing. With the opportunity realized, Nicklas set about conducting feasibility studies to explore options for a facility and the paint lines.
The company worked with the FCADC to lease a facility in the Chambers-5 Business Park in the heart of Chambersburg. The facility provides convenient and quick access to major truck routes. SIA is located within 30 minutes of major operations for OEMs such as Volvo Construction Equipment, Manitowoc Cranes and JLG Industries.
Located in a bustling industrial park, SIA is situated on Sheffler Drive in Chambersburg. The plant is 50,000sf and the 10-acre campus offers opportunity for outdoor storage or future expansion. Sponseller also indicates there are significant warehousing opportunities in the immediate area, even across the street.
Working with Herr Industrial from Lancaster, Pennsylvania, Nicklas commissioned an extensive feasibility study. The study explored buying and constructing new paint lines, or option B—he knew one of his customers, JLG, had decommissioned an impressive powder coating line sitting idle and unused in its Shippensburg facility, just 20 minutes away.
After negotiations with JLG, Nicklas agreed to purchase, deconstruct, re-engineer and reinstall the 100,000-square-foot line. JLG had been interested in the floor space for assembly capacity since it had shut the line down two years prior as it outsourced painted parts and kits. This further validated the opportunity for SIA.
It was no easy feat to cut a 100,000 square foot line into thousands of pieces, then stage, re-engineer and reinstall in a space half the size. But the value in the power and free conveyor and other controls on the line justified the extensive construction plan through the efforts of Herr’s project manager, who decided to stay on with SIA and is now the maintenance supervisor. The results of these efforts offer SIA customers a superior painting operation.
The line itself is unique in that it provides a large part-size envelope (12 × 12 × 6 feet / 3,000 pounds per carrier) in a controlled process environment and flexibility on the power and free conveyor. All parts are hung on designated carriers and barcoded at point of entry. The system captures all specifications—paint type, color, and other aspects of each job. And the data of each carrier and job can be captured.
“This feature really allows us to document and demonstrate to our customers that we do what we say we do. The test results and quality we express are true and proven,” says Sponseller.
Parts then make their way through the metal substrate preparation, one of the true differentiators of this process.

Sunset Industrial Applications has 17 carriers, each of which can handle up to 3,000 pounds.
Preparation Process
One of the companies that helped SIA through the construction and installation of the new facility was Coral Chemical Co., which has helped manage its pretreatment systems. Coral Sales Representative Ed Besterfeldt has known Nicklas for many years and helped design the processes that make up the backbone of the SIA operation.
Nicklas tasked Coral Chemicals with coming up with effective and green ways to pretreat a variety of surfaces, including metal fabrications and castings. The result was an acid cleaning process that removes the organics and takes care of laser scale, too.
“It’s essentially two chemical stages, and the rest rinses,” Besterfeldt says. “It handles both liquid and powder coatings now, and there’s some dialogue on future needs, too.”
The system uses Coral Eco-Treat, which essentially eliminates phosphate wastewater. It is a green technology that makes it easier for Sunset Industrial Applications to meet tighter environmental regulations, since the sludge generated from the treatment of phosphate-free wastewater is no longer automatically classified as hazardous waste, Besterfeldt says.
In addition, Eco-Treat—a fluorozirconium-based conversion coating—operates at ambient temperatures, which helps save energy and reduce sludge and scale formations.
Fluorozirconium-based conversion coatings use the transitional metal vanadium, which is commonly used as an alloying element in steel that's used for making high-quality tools and rust-resistant springs. Vanadium compounds also have been used to improve the corrosion protection provided by anodized coatings; small amounts added to sulfuric acid anodizing solutions usually makes the anodized coating much more protective after hydrothermal sealing.
Sponseller says that one of SIA’s advantages she has been touting to would-be customers is the green technology the company is using, as well as the zero-discharge wastewater system.
“We make our own distilled water from the reverse osmosis process; any excess water is evaporated,” Sponseller says. “OEMs have high standards when it comes to quality and process control, including the environment. We are responding to their expectations for superior quality while lessening the impact on our environment.”
Liquid and Powder
Once the substrate prep is completed, every carrier passes through a dry-off oven and a manual inspection and masking stage. The system has sophisticated readers that send every carrier through the paint line it requires—liquid or powder.
The liquid line includes prime and top coat booths with Graco ProMix systems. This allows SIA to include as many as 30 colors and four catalysts in its paint kitchens.
“Each carrier can be painted a different color, like red, white and blue, one after another,” Nicklas says. “It also gives us visibility in terms of paint usage and VOC contents.”
Powder coating offers a similar configuration with two booths. Currently, they are both used for single-coat powder, but SIA is poised and ready for new industry processes and customer specifications calling for universal primers, dust-on-dust or gel fusion primers with a return through the cure oven.
Once the coating is applied, all carriers reach the cure stage, which includes two large ovens that are currently configured for individual wet and powder coatings to prevent particle contamination.
Results
“Overall, these lines are sophisticated and flexible. The quality results coming from our facility are exceeding 1,000 hours salt spray and other more aggressive testing. Sometimes with paints which are meant to fail more than half the time,” says Nicklas.
SIA is an approved paint operation for global OEMs such as Volvo, Manitowoc and JLG / Oshkosh.
“We were excited to receive a perfect audit score from Oshkosh,” says Sponseller. “With the exceptional quality, available capacity, throughput and proven processes, this facility will be a success.”
Sales are growing, but the business development cycle with larger corporations is much longer than the management team expected.
“It makes you feel like someone all dressed up for a New Year’s party but with no invitation,” Sponseller says.
For more information on Sunset Industrial Applications, contact Laura Sponseller at lsponseller@sunsetia.com or 717-263-1550 ext 211. For information on Coral Chemicals, visit coral.com. For information on Herr Industrial, Inc., visit herrindustrial.com.
Related Content
Masking Solutions Provider CFS Dramatically Expands Capabilities and Capacity
Custom Fabrication & Supplies (CFS) completed a new plant expansion packing 10 times the capacity into twice the space. It dramatically enhances the supplier’s custom capabilities to provide extremely precise and cost-effective masking solutions.
Read MorePowder Coating 4.0: Smarter, Faster, More Efficient and Connected
New tools reduce cost and waste, lower manufacturing footprint of powder coating operations.
Read MoreProducts Finishing Reveals 2024 Qualifying Top Shops
PF reveals the qualifying shops in its annual Top Shops Benchmarking Survey — a program designed to offer shops insights into their overall performance in the industry.
Read MoreLow-Temperature-Cure Powder Coatings Offer Unique Opportunities
An in-depth look at the advantages of low-temperature-cure powder coatings and the considerations for incorporating them into your process.
Read MoreRead Next
Price is Finally Getting It Right With Coral Chemicals
How one company changed chemical baths and saw improved products and cost savings.
Read MoreA ‘Clean’ Agenda Offers Unique Presentations in Chicago
The 2024 Parts Cleaning Conference, co-located with the International Manufacturing Technology Show, includes presentations by several speakers who are new to the conference and topics that have not been covered in past editions of this event.
Read MoreEducation Bringing Cleaning to Machining
Debuting new speakers and cleaning technology content during this half-day workshop co-located with IMTS 2024.
Read More