An Interview with Brett Smith, CAR
Brett Smith, director, technology, Center for Automotive Research, discusses his work in the propulsion side of the automotive industry and his thoughts about the future of electric vehicles.
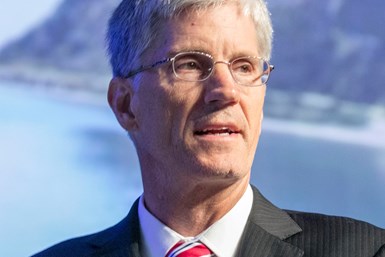
Brett Smith, director, technology, Center for Automotive Research
Center for Automotive Research (CAR) director, technology, Brett Smith’s work has spanned many critical aspects of the automotive industry including vehicle and component manufacturing; materials forecasting; product development and analysis; supplier-manufacturer relations; technology development; facility location analysis; product launch strategy and human resource and talent issues. At this year’s SUR/FIN finishing industry tradeshow, Smith will deliver a keynote on Tuesday, November 2, at 1 p.m. titled “Battery Electric Vehicles…The Tidal Wave of Change.” Smith’s session will address how the advent of electric vehicles (EVs) is putting traditional supply chains, materials and manufacturing methods at risk of being replaced and other implications of developing battery technologies.
Products Finishing sat down with Smith for a quick interview to hear about his work at CAR and his ideas about the future of automotive.
In your own words, describe your work at CAR.
CAR is viewed as a partner by those in the automotive industry. That has allowed us to get a chance to talk with companies on an intimate, friendly basis as confidants over the decades. It’s really been a valuable part of my learning experience and knowledge base. For the last 20 years, I’ve spent a good portion of my job on the propulsion side of the business including technology, strategy, policy and even labor issues related to propulsion.
You’ll be giving a keynote at this year’s SUR/FIN about the changes that battery electric vehicles (BEVs) are bringing about in industries that support automotive. For a long time, detractors have said the EV technology could never replace traditional cars. It seems we’re at a point where people are beginning to better understand the ways EVs will shape what global mobility looks like. Can you paint a bit of a picture about where the industry is at this point?
We haven’t had a recession in a decade — we’re going to have a recession. I think it will be interesting, when the recession comes, how companies will react to these new technologies. Traditionally in the industry, when we get to a recession, we pull back on stuff that isn’t going to make money in the short term. If I have the choice of spending money on a project that may be really cool in five, six or eight years, versus one that I know I'm going to make money on next year, in down times I’m going to spend it on the one I know I’m going to make money on. That’s just the smart thing to do.
The difference here is that historically, we’ve always had the same competitors. This time going into a recession — and no, I wasn’t predicting a pandemic — something interesting was happening. The companies driving the technology discussion weren’t the usual suspects. It wasn’t the car companies. It was the tech companies — who don’t have a history of pulling back during recessions, and who have boatloads of money to keep pushing the technology. And so, I think car companies have decided that EVs are no longer advanced R&D, they are product development.
Many coatings tend to be time-tested processes that don’t evolve too much. Can you address some of the things coaters will need to think about in the future?
There’s a real push, particularly from other parts of the world, for sustainability and environmental friendliness. That applies to all the components and all the processes that contribute to the production of a vehicle.
Something that I think will be exciting to watch over the next five years is the change in how we build cars. If you think about it, we went from decades of building basically the family truckster from “National Lampoon’s Vacation” to building unified body, front wheel drive vehicles. That transition of learning how to build those happened over about a 7-10 year period – and it was driven by fuel economy. I would argue that we are at that next transition point. We’re looking at the question of how to build a better electric vehicle – and those that want to build it the same way that you would a gasoline car may not be successful in this transition.
This is a transitional, generational generation, where we’re seeing the companies start to explore this. I think over the next generation we’ll see the next generation of assembly processes. And it may not look exactly like what we see now. Which, for everybody in the industry, means “how does my part or process fit into that.” From new materials to new shapes, everyone supplying some part or process to the industry needs to ask, “what will this new manufacturing paradigm mean to me?”
Related Content
NASF/AESF Foundation Research Project #121: Development of a Sustainability Metrics System and a Technical Solution Method for Sustainable Metal Finishing - 15th Quarterly Report
This NASF-AESF Foundation research project report covers the twelfth quarter of project work (October-December 2023) at Wayne State University in Detroit. In this period, our main effort focused on the development of a set of Digital Twins (DTs) using the Physics-Informed Neural Network (PINN) technology with application on parts rinsing simulation.
Read MoreCalculating Applied Media Force During Vibratory Finishing
What appear to be identically set-up vibratory bowls will finish identical loads of parts in varying time cycles. This paper offers a new technique to better predict what the operator will produce, by measuring the force applied to the parts. It is the efficiency of that force which controls the efficiency and speed of the refinement cycle.
Read MoreHighlights from SUR/FIN 2023
Products Finishing offers a recap of some of the topics that were top of mind at the SUR/FIN 2023 finishing industry trade show.
Read MoreSUR/FIN 2023: Capsules from the Technical Sessions I: Emerging Technologies
SUR/FIN 2023 in Cleveland this past June was a resounding success. Due to the efforts of the Technical Activities Committee, ably led by Bill Nebiolo this year, an outstanding program of technical presentations was offered. What follows are summaries of selected presentations from the Emerging Technologies sessions. Additional coverage will be provided in this space in the coming months. The full report can be accessed and printed at short.pfonline.com/NASF23Aug1.
Read MoreRead Next
Speedy Growth in EV Batteries Spurs Cleaning Technology
Hubbard-Hall teams up with lithium-ion battery makers to provide cleaning chemistry for electric vehicle batteries.
Read MoreAxalta Launches Mobility Coatings Business
The redefined transportation coatings business will focus on supporting e-mobility and its evolving coatings needs.
Read MoreCoatings Drive Electric Vehicles Further
Electric vehicle batteries depend on coatings to maintain optimal temperatures, reduce the risk of fire damage and electrical interference, and more.
Read More