Capital Cost Considerations in Finishing Projects
In Part 2, we discuss considerations for cost estimates over the life cycle of a surface finishing project.
Capital and operating and maintenance (O&M) cost estimates are important for project planning, development and implementation when building new process lines or for renovating/replacing existing process lines. With an overview of AACE International capital cost estimate classifications now established, in Part 2 we can discuss considerations for cost estimates over the life cycle of a surface finishing project.
Table 2 below shows capital cost accuracy ranges at the lowest and highest expected certainties for each of the five AACE cost estimate classes — for example, an aerospace surface finishing project with a capital cost expected value, assumed to be constant for each estimate class, of ten million dollars ($10.0M).
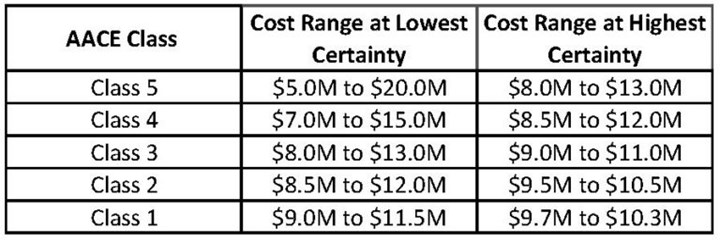
TABLE 2: AACE Low and High Expected Ranges for Surface Finishing Project Expected Value Capital Cost Estimate of $10.0M. NOTE: In millions of dollars (including contingency). See Table 1, Part 1 for AACE range percentages.
Table 2 shows large differences in accuracy ranges for each AACE Estimate Class from lowest to highest certainty levels. Note that the cost ranges are the same (around the $10M estimated expected cost) comparing a Class 5 estimate with high certainty and a Class 3 estimate with low certainty and also comparing a Class 4 estimate with high certainty and a Class 2 estimate with low certainty. As discussed in the March 2019 AACE 18R-97 reference for process industries:
- For complex or risky projects, the cost uncertainty ranges can increase by 2X to 3X.
- Estimate accuracy ranges can be impacted by systematic project risks, including level of familiarity with technology; unique/remote project locations and conditions and availability of relevant cost data; project complexity; quality of reference cost data; quality of cost estimate assumptions; estimator experience and skill; estimating techniques and budgeted time and effort; market and pricing conditions; currency exchange; and accuracy of process definition.
The following lists for each AACE cost estimate class, typical percentage completion of surface finishing project engineering deliverables (in parenthesis – see Part 1 for full ranges), key project engineering definition at the time of the estimate, typical cost estimate methodology and typical estimate uses:
- Class 5 (2%): Initial project high-level scoping walk through and owner discussions are complete and preliminary surface finishing project location, automated processes and process lines (anodizing line, nickel plating line, and specialty electroless and electroplating line), and ancillary systems to be included in the project identified. A Class 5 capital cost estimate is prepared based on extrapolation/interpolation from completed costs from similar projects, with adjustments for comparative scope differences and cost factors, such as project location, complexity and inflation over time. Class 5 capital cost estimates are used to identify potential alternate project scenarios and for some initial project screening and strategic business planning.
- Class 4 (15%): Process sequence diagrams are complete for surface finishing processes and preliminary process flow diagrams are complete for surface finishing and major ancillary processes. Preliminary layouts and elevations are developed to assess space requirements and clearances. The Class 4 capital cost estimate is used to confirm project feasibility, select or narrow major process/configuration options, and prepare preliminary budgeting.
- Class 3 (30%): Process deliverables (including piping and instrumentation diagrams (P&IDs), major equipment lists, functional description, preliminary 3D model, and energy and material balances) are developed to a point where the process design basis is “frozen,” allowing subsequent release to multidiscipline engineering design team to develop design details. The Class 3 estimate is prepared using line item costs for major equipment and systems, plus percentage or lump sum line items and allowances for balance of systems (for example, miscellaneous mechanical, electrical and I&C), installation, freight, taxes, engineering and professional services, and markups that are based on similar project/location experience. The Class 3 capital cost estimates are often used to support full project funding requests and for initial project budget and schedule controls (until replaced with more detailed estimates). From the March 2019 AACE International 18R-97 reference for Process Industries, “In many owner organizations, a Class 3 estimate is often the last estimate required and could very well form the only basis for cost/schedule control.”
- Class 2 (60%): An intermediate level 3D model and intermediate design deliverables for all engineering disciplines are complete, including plans, schedules and lists with the final level of details to be added following Intermediate Design review. The Class 2 estimate is prepared using detailed cost line items from vendor quotes and relevant cost references. For scope areas still remaining to be detailed, assumed levels of line item breakout and detail takeoff (forced detail) are used. The Class 2 capital cost estimate is used as the detailed contractor control baseline.
- Class 1 (95%): All Prefinal engineering design documentation is complete, including detailed 3D model and process, structural, mechanical, electrical and instrumentation and control (I&C) drawings; specifications; schedules; diagrams; and lists. The Class 1 estimate is prepared using detailed line item breakouts for all relevant project scope areas and using quantities measured or calculated in the design documentation. The Class 1 capital cost estimate is used by owners and contractors to support the change management process and for vendor/contractor negotiations. The Class 1 capital cost estimate is used by construction contractors to support their bids and for final control baseline and change management support.
Setting surface finishing project scope early is important to establish sufficient budgets and to avoid project disruption in detailed design phases. Early consideration of process equipment quality and durability, robust materials of construction, critical equipment and systems redundancy, project phasing and delivery logistics, and flexibility for future production and process changes are important to avoid oversights and shortfalls on project budget planning. Potential project scope variances for surface finishing projects should be identified based on a depth of industry process experience and alternatives with separate cost estimates should be developed, where applicable. Project life cycle costs can be minimized by cost effectively adding capital costs for systems and quality that minimize future process/production disruption and maintenance/repair costs, as well as reducing costs for anticipated future process modifications. Expert cost estimating and process engineering support, through the development and delivery of surface finishing projects, are valuable for defining and expediting quality projects with strong life cycle benefits.
__________________________________________________
Peter Gallerani is president and chief technology officer at Integrated Technologies, Inc., an engineering, design and consulting solutions firm based in Burlington, Vermont, that offers project planning and development, full-service engineering and design, project and construction management, and services during construction to the surfacing finishing and industrial manufacturing industries. Visit processengineer.com
Related Content
Anodizing for Bonding Applications in Aerospace
Anodizing for pre-prep bonding bridges the gap between metallic and composite worlds, as it provides a superior surface in many applications on aluminum components for bonding to these composites.
Read MoreChicago-Based Anodizer Doubles Capacity, Enhancing Technology
Chicago Anodizing Company recently completed a major renovation, increasing its capacity for hardcoat anodizing and Type II anodizing.
Read More10 Anodizing Best Practices
Following this list of guidelines can help to increase the performance, cost effectiveness and quality for your anodizing operation.
Read MoreCalifornia Public Hearing to Decide Fate of Hex Chrome Plating and Anodizing
Metal Finishing Association of California urges all members of the metal finishing community to submit comments prior to the hearing.
Read MoreRead Next
Education Bringing Cleaning to Machining
Debuting new speakers and cleaning technology content during this half-day workshop co-located with IMTS 2024.
Read MoreDelivering Increased Benefits to Greenhouse Films
Baystar's Borstar technology is helping customers deliver better, more reliable production methods to greenhouse agriculture.
Read MoreEpisode 45: An Interview with Chandler Mancuso, MacDermid Envio Solutions
Chandler Mancuso, technical director with MacDermid Envio discusses updating your wastewater treatment system and implementing materials recycling solutions to increase efficiencies, control costs and reduce environmental impact.
Read More