Dürr Builds Two Paint Shops for Heavy Truck Manufacturer in China
The two paint shops for Sinotruk are being built in the eastern Chinese province of Shandong. Cabs for various trucks and other commercial vehicles – including Sinotruk’s Yellow River, Sitrak and Howo – will be painted at the new shops.
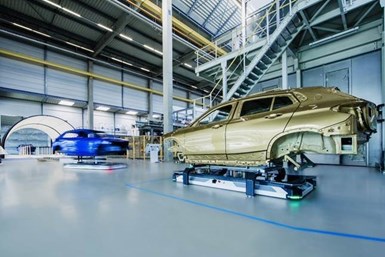
EcoProFleet AGVs are already in use in passenger car production and will be transporting truck cabs for the first time at Sinotruk. Photo Credit: Dürr
Dürr is currently building two paint shops for Sinotruk, a manufacturer of heavy trucks in the eastern Chinese province of Shandong. The paint shops will be used to coat truck cabs and pick-ups of Sinotruk’s premium brands.
The two paint shops for Sinotruk’s subsidiaries, Ji’nan Truck and Ji’nan Commercial Vehicle, are being built in Laiwu and Zhangqiu. Cabs for various trucks and other commercial vehicles – including Sinotruk’s Yellow River, Sitrak and Howo – will be painted at the new shops. The site in Zhangqiu will also manufacture pickup trucks.
Dürr says its automated guided vehicles (AGV) are an important building block for a flexible plant layout, which Sinotruk can expand at a later date or integrate new models into. Dürr developed its flexible conveyor technology, EcoProFleet, specifically for use in paint shops. In order to move the heavy loads, the technology has been designed with an unladen weight of 850 kg with a maximum load capacity of 1,000 kg. The fleet is controlled by Dürr’s DXQcontrol software, and AGVs can reportedly charge within 1.5 minutes.
An energy efficient painting process
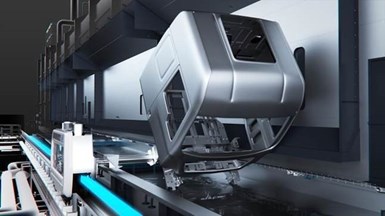
Sinotruk uses Dürr’s RoDip E for pretreatment and cathodic electrocoating. Photo Credit: Dürr
At the beginning of the painting process, the electric rotational dip system, RoDip E, enables individual dip curves for pretreatment (PT) and cathodic electrocoating (EC), which is said to optimize the coating quality between different cab models. With this method, each cab is transported through the complete PT and EC process using a freely programmable trolley. Each trolley has a conveying drive and a rotating drive, which enable horizontal and rotating movements to be controlled independently of each other for each cab. The immersion tanks for the rotational process are smaller than with a traditional pendulum conveyor, which means that less energy and chemicals are required.
In each of the two paint shops, two of Dürr’s EcoRS sealing robots seal the inner seams, and another two apply liquid sound deadener in a fully automatic process. The base coat and clear coat in each paint shop are applied by 19 EcoRP painting robots, which are equipped with EcoBell3 high rotation atomizers. Dürr claims this technology enables Sinotruk to achieve the best possible painting results in terms of color shade and flow values, as well as creates uniform layer thicknesses. Dürr also says the application technology creates less of an impact on the environment due to high rotation atomizers with electrostatic charging. With the color change technology and the EcoBell Cleaner D2 for cleaning atomizers, paint loss during color changes and consumption of flushing agent and solvent – and thus volatile organic compound (VOC) emissions – are reportedly minimized.
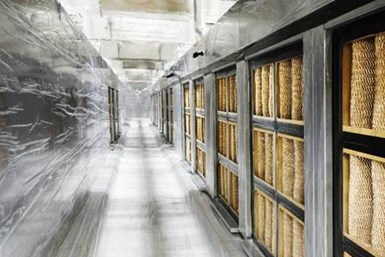
EcoDry X uses cardboard filter boxes as a separating agent for overspray. Photo Credit: Dürr
The EcoDry X dry separation system, which Dürr says doesn’t require water or chemicals, is another technology used in the new Sinotruk paint shops. The system uses inexpensive cardboard filter boxes to efficiently separate overspray, and, if necessary, operators are able to remove saturated filter boxes during production time.
Automated quality control
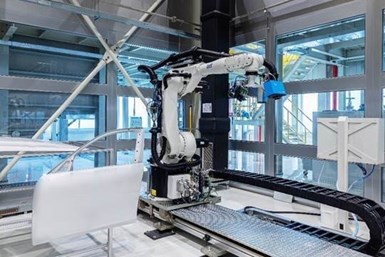
Robot-controlled sensor technology checks defined points on the truck cabs fully automatically. Photo Credit: Dürr
At the end of the painting process, the body surface is checked at an automated quality control station. Here, a robot follows defined checkpoints on the truck cabs and uses sensors to record data about color variations, surface texture and layer thickness. This data is then transferred to the database and visualized digitally for the operator.
Outside of the painting process, Dürr will also supply the plants with end-of-line testing technology. In Laiwu, four x-wheel truck D test stands equipped with 3D measurement technology will be used to measure and adjust the vehicle axis geometry. The safety-relevant driver assistance systems of the trucks are precisely adjusted using Dürr test technology. With the modular test stand concept x-DASalign, the sensor technology for the lane departure warning system and the advanced emergency braking system are aligned in relation to the geometric driving axle of the vehicle. In addition, Sinotruk’s production plant for light trucks in Zhangqiu will use the x-wheel alignment stand with the latest x-3Dsurface measurement technology and the multifunctional roll, brake and ABS test stand.
Sinotruk’s plants are scheduled to start production in 2021 and 2022.
Related Content
10 Ecoat Best Practices
Following this list of guidelines can help to increase the performance, cost effectiveness and quality for your ecoat operation.
Read MoreTTX’s Automated Conveyor Carrier System Offers Wireless, Flexible Operation
ACC system designed for reliable, consistent point-to-point movement of everything from small to heavy parts.
Read MoreProfessional Plating Expands Zinc, Ecoat Offerings
Ever expanding, Professional Plating of Brillion, Wisc., has announced two capital investments: a second zinc line and an upgrade of its ecoat capabilities.
Read MoreMasking Solutions Provider CFS Dramatically Expands Capabilities and Capacity
Custom Fabrication & Supplies (CFS) completed a new plant expansion packing 10 times the capacity into twice the space. It dramatically enhances the supplier’s custom capabilities to provide extremely precise and cost-effective masking solutions.
Read MoreRead Next
Delivering Increased Benefits to Greenhouse Films
Baystar's Borstar technology is helping customers deliver better, more reliable production methods to greenhouse agriculture.
Read MoreA ‘Clean’ Agenda Offers Unique Presentations in Chicago
The 2024 Parts Cleaning Conference, co-located with the International Manufacturing Technology Show, includes presentations by several speakers who are new to the conference and topics that have not been covered in past editions of this event.
Read MoreEducation Bringing Cleaning to Machining
Debuting new speakers and cleaning technology content during this half-day workshop co-located with IMTS 2024.
Read More